-
- News
- Books
Featured Books
- pcb007 Magazine
Latest Issues
Current IssueThe Hole Truth: Via Integrity in an HDI World
From the drilled hole to registration across multiple sequential lamination cycles, to the quality of your copper plating, via reliability in an HDI world is becoming an ever-greater challenge. This month we look at “The Hole Truth,” from creating the “perfect” via to how you can assure via quality and reliability, the first time, every time.
In Pursuit of Perfection: Defect Reduction
For bare PCB board fabrication, defect reduction is a critical aspect of a company's bottom line profitability. In this issue, we examine how imaging, etching, and plating processes can provide information and insight into reducing defects and increasing yields.
Voices of the Industry
We take the pulse of the PCB industry by sharing insights from leading fabricators and suppliers in this month's issue. We've gathered their thoughts on the new U.S. administration, spending, the war in Ukraine, and their most pressing needs. It’s an eye-opening and enlightening look behind the curtain.
- Articles
- Columns
- Links
- Media kit
||| MENU - pcb007 Magazine
Estimated reading time: 8 minutes
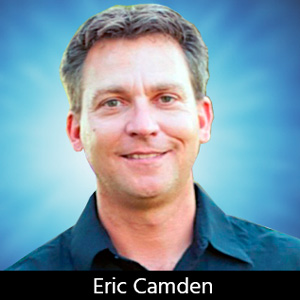
Quest for Reliability: Improving Reliability for Free
While implementing a digital factory for assembly will help predict measurables like cost and throughput, can you also rely on that data to predict your product reliability? Admittedly, I am not an expert on the implementation of a digital factory, so if you decide to move onto the next article, my feelings will not be hurt.
I know that words and phrases like 3D motion simulation, integration, and virtual models are used, but I honestly don’t have a clue what the meaning of those words are in this context. Please don’t hire me to help you with your digital factory implementation. I mean, it’s your money, and I’ll probably take the job, but I can guarantee we will both regret that decision.
The good news is that I do have quite a bit of experience with reliability, so let’s stick with that for now. I have seen more than a few factories make the move to use more and more automation that has indeed improved production numbers but has done very little to address cleanliness and reliability. If you are building a thousand pieces per hour of reliable products, that is a good thing.
However (and you knew the "but" was coming), if you have an unknown issue in your process, and it goes undetected because you are solely relying on your system, you might be producing a thousand failures per hour. If this is the case, you might be lucky enough to catch the product while it is still in-house and direct it to quarantine for disposition—that is, if you are lucky enough to catch the problem before it heads out to its next destination.
To help reduce the risk of producing a questionably reliable product, I am going to take this opportunity to pretty much completely disregard this month’s topic and offer up a few easy steps you can take to reduce that risk. Remember, what I know about implementing a digital factory would maybe fill a thimble, so this will be time better spent for both of us.
One thing I have learned after 20 years is that while there are endless combinations of materials that could be used for an assembly, the number of actual assembly process steps is fairly low and consistent. There are a few exotic processes that won’t be covered today, but if you have one, I would love to see it. I will address the basics that seem to be consistent with 99% of all manufacturing I see on a regular basis. As with all good stories, let’s start at the beginning.
Receiving materials is a step of the process that is not always thought to be directly related to reliability, but it’s just as important as any other step. I was in a facility just last week that had one of the biggest issues I see with receiving where the dock doors open directly to the warehouse racks. I was in a normally arid part of the world, and the issue is if the doors are open to the outside environment, and a wind kicks up, there is a real opportunity for dust that might be laden with ionics to come right in and deposit on the racks or even to the production floor. This could pose a threat to solderability if there are any open packs of bare boards or parts.
If the process is truly no-clean, there may also be an issue with the adhesion of conformal coating if that is to be used. Further, there is an issue with spikes in the amount of available atmospheric moisture when it rains. This can cause the same issues as dust, but you can also add in problems like an under-cured solder mask absorbing moisture into the board and causing more problems down the road when that moisture comes into contact with other process residues.
The one thing that is normally covered and exempt from the dock doors being open is parts that have a moisture sensitivity level. The impact would be on the dry cabinet and how hard it works to maintain a low percentage of relative humidity. In general, you want to segregate the receiving area and the storage areas to be sure that the outside environment has as little impact as possible.
Normally, in the same part of the facility, you will find solder paste and epoxy storage. You want to be sure that your refrigerator temperature and relative humidity are being monitored with a calibrated device with alarms for exceeding the upper and lower control limits. It is always recommended to have a system for monitoring the temperature and humidity in all parts of the facility, and receiving is no exception to that.
Now, let’s move onto the surface-mount solder process as it is normally next in line, and this is where the real action starts. The first part of this process is, of course, the solder paste printing process. When it comes to paste printing, I can only recommend a few tips, as we don’t see a lot of problems stemming from this process. What we see on a regular basis are poorly cleaned stencils that collect paste in the corners of the apertures that can cause skips in paste deposition. A good paste process will include automated solder paste inspection (SPI) to find anomalies. If a misprint is discovered, the board should only be cleaned with an aqueous wash process of some sort if cleaning of misprints is allowed at all. The same goes for the stencils.
We now have properly pasted boards, and parts are placed properly I assume, it’s time to get them into the oven for reflow. The thermal profile is pretty much the most important part of this process, so it’s imperative to do it right. Doing it right includes taking a look at the paste manufacturer’s recommendation, and then realizing they have no idea what you are building.
The reflow profiles on most of the tech datasheets, and the correlating analytical data, are based on bare test boards that don’t represent the thermal mass or complexity of your product. When determining the profile parameters, you must use an actual assembly—most often, a first article or prototype unit. The thermocouples need to be placed at locations with the highest areas of thermal mass and areas with components that are difficult to process like QFNs and other bottom-terminated components.
Another good idea is to keep up on machine maintenance. If the exhaust ducts are clogged, the airflow will be restricted, and flux activators won’t be drawn out of the machine and can collect on the inner surfaces. When enough of this material collects, it can drip back onto the surface of the board in a form that is basically pure activator and extremely conductive and corrosive.
Now, we move onto the plated through-hole process, where applicable, of course. Wave soldering can be the dirtiest of all solder processes, and this is normally because of the liquid flux application process. The standard process is an indexing spray flux at the opening of a wave solder machine. The problems we see with this process is excess flux being drawn to the top side of the assembly through the vias and up the part leads. The issue with this is that the flux may or may not reach the required temperature to render it near benign as designed by the manufacturer. This is especially a problem if a selective solder pallet is used.
When flux is drawn into areas that are designed to keep flux out, it is shielded by the pallet from the proper temperatures. The same can be said for other types of selective solder using robotics or humans. Humans are normally the worst of the worst when it comes to causing electrical leakage and electrochemical migration. This is usually associated with the use of a bottle of liquid flux for hand solder of PTH parts. Generally, extra flux will make a nice shiny solder joint, but it will also leave a lot of active flux residues causing issues.
The next assembly category is what I consider most of the miscellaneous processes that aren’t standard. This is where the conformal coating, various epoxies for staking, underfill, etc., are applied. Each of these processes have their own inherent problems, and the preceding soldering processes can have a huge impact if not properly done. Excessive flux residues will impact the adhesion of any subsequent application on top of the electrical leakage issues.
Then, the parts need to be installed into their housings in the case of facilities doing a full box build or into boxes for shipping to the next supplier. Yes, even this process can impart enough contamination and handling residues to facilitate the dreaded dendrite growth. The simple tip I have for this process is to be sure and only handle the assemblies by the edges. I assume you’ve always only handled them by the edges, right? RIGHT? The other thing to keep at the top of your mind is to only use new, or provably clean, ESD bags for packaging.
Those are just a few simple things that can be done to help reduce the number of detrimental residues on your assemblies, and none of them cost a dime. I do apologize if you came to my column this month, hoping to see some detailed dive on the implementation of a digital factory. I’d have been interested in reading what I had to say about that as well. Maybe next time this topic rolls around.
This column originally appeared in the April 2020 issue of SMT007 Magazine. Eric Camden is a lead investigator at Foresite Inc.
More Columns from Quest for Reliability
Quest for Reliability: Here We Go (Virtual) AgainQuest for Reliability: Put Your Operators in the Driver’s Seat
Quest for Reliability: What’s Lurking in the Shadows?
Quest for Reliability: Reliability Starts at the Bottom
Quest for Reliability: Correlating COVID-19 With Reliability?
Quest for Reliability: Big Trouble Comes in Tiny Packages
Quest for Reliability: New Solder, Same Old Testing
Quest for Reliability: Sunshine and Circuit Boards