-
-
News
News Highlights
- Books
Featured Books
- pcb007 Magazine
Latest Issues
Current IssueThe Hole Truth: Via Integrity in an HDI World
From the drilled hole to registration across multiple sequential lamination cycles, to the quality of your copper plating, via reliability in an HDI world is becoming an ever-greater challenge. This month we look at “The Hole Truth,” from creating the “perfect” via to how you can assure via quality and reliability, the first time, every time.
In Pursuit of Perfection: Defect Reduction
For bare PCB board fabrication, defect reduction is a critical aspect of a company's bottom line profitability. In this issue, we examine how imaging, etching, and plating processes can provide information and insight into reducing defects and increasing yields.
Voices of the Industry
We take the pulse of the PCB industry by sharing insights from leading fabricators and suppliers in this month's issue. We've gathered their thoughts on the new U.S. administration, spending, the war in Ukraine, and their most pressing needs. It’s an eye-opening and enlightening look behind the curtain.
- Articles
- Columns
- Links
- Media kit
||| MENU - pcb007 Magazine
Estimated reading time: 4 minutes
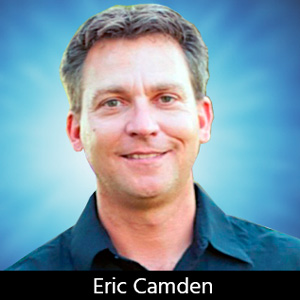
Quest for Reliability: Big Trouble Comes in Tiny Packages
When it comes to making consumers happy and electronic assemblers miserable, nothing achieves both quite like miniaturization. With our ever-increasing demands to house a full-size movie theater with surround sound and limitless digital storage in the palm of our hands, the only way for CMs to respond is with miniaturization (and cursing—lots of cursing). In this installment, I’ll revisit the history of shrinking packaging and lessons learned.
The move to make products smaller isn’t anything new, but, at this point, it is a matter of scale. Making a computer’s physical footprint fit inside a room smaller than the size of a football field was a big leap, but a lot of the technology required to do that didn’t exist until that happened. There was a healthy amount of new component technology being introduced into the industry at the time that made that process much easier in comparison to what the industry is working with today. When the size of a product has already been reduced to the smallest thing you’ve ever seen, making that even smaller will require shrinking of every component that is already being used.
Any time you reduce the spacing between leads or contacts with bias differential, you increase the risk of electrical leakage and electrochemical migration. Using parts with tighter spacing, or lower standoff will most likely require multiple rounds of verification testing to ensure proper processing of the flux activators. As mentioned in previous columns, the product’s end-use environment plays a very large role in reliability. This puts the focus on cleanliness after the assembly process.
When the lead pitch is reduced, lower levels of conductive residue are required to create electrical leakage paths. When discussing the end-use environment, the main parameter we look at is available atmospheric moisture. The leakage fire triangle requires conductive residues, atmospheric moisture, and electrical bias. Of those three ingredients, the one that is easiest to control is the residues.
The reduction in component pitch puts a premium on cleanliness to reduce the risk of dendrite growth-related field returns. When processing with no-clean flux, the focus is on the thermal profile for ensuring that all flux activators are properly complexed with the activators outgassed as designed by the flux manufacturers. Conversely, when an aqueous wash process is used after assembly, it is important to be sure the process is fully removing all of the residues. If you are washing a water-soluble flux, any remaining residue will be conductive without question, and if washing no-clean flux, any remaining residue may or may not be conductive.
Washing a no-clean flux is especially challenging when parts with tight pitch spacing are used because the outer shell of the flux can effectively create a dam between the leads and prohibit the wash solution from penetrating under the part as necessary to remove all the residues. Far too often, we see customers that had been using a water-soluble flux migrate over to a no-clean flux and use the same recipe that was previously effective without understanding the differences in the materials. The problem with that is the extra energy required to break through the outer resin shell that is created through the thermal excursion that is meant to help prohibit moisture from reaching any active residues.
If the process is only breaking down that outer shell, it will often leave behind the residues that were meant to be protected and can be just as conductive as water-soluble flux. This is why testing at the specific fine pitch component locations with ion chromatography is so important whether you are cleaning or not. IC testing will yield data that tells you the type and amount of ionic content present. That tells you if you are at an increased risk of electrical leakage in the field. This all speaks to your product’s reliability, which, of course, speaks to your company’s bottom line and reputation.
Cleanliness is one of the most important aspects to consider when using these types of components but certainly not the only aspect. Another thing to consider is the paste printing process. When you print solder paste for these parts, there is an increased risk of bridging after reflow soldering. This can increase hand rework after reflow, and every time you subject your product to a human, you increase the risk of damage. When a machine is making a mistake, it will normally make that mistake repeatedly, and those types of issues are fairly easy to discover and fix.
When you send your assemblies to one of many operators in the rework area, the risk of one-off damage increases because it is much harder to control each operator’s process. There may even be a need to evaluate the paste flux currently being used to determine if that is still a viable material for your process. All major flux manufacturers offer a range of options that specially address fine-pitch components, so if you need to make a change, there should be no shortage of materials available.
The bottom line, from my point of view regarding reliability on miniaturization, is the same as with any assembly process; you have to do the required chemical and environmental testing to determine if your assembly parameters are properly processing the chosen material set in a way that does not increase the risk of electrical leakage in the field. Now, we just need to work on a popcorn popper that fits in my other pocket.
This column originally appeared in the February 2020 issue of SMT007 Magazine.
More Columns from Quest for Reliability
Quest for Reliability: Here We Go (Virtual) AgainQuest for Reliability: Put Your Operators in the Driver’s Seat
Quest for Reliability: What’s Lurking in the Shadows?
Quest for Reliability: Reliability Starts at the Bottom
Quest for Reliability: Correlating COVID-19 With Reliability?
Quest for Reliability: New Solder, Same Old Testing
Quest for Reliability: Improving Reliability for Free
Quest for Reliability: Sunshine and Circuit Boards