-
- News
- Books
Featured Books
- pcb007 Magazine
Latest Issues
Current IssueThe Hole Truth: Via Integrity in an HDI World
From the drilled hole to registration across multiple sequential lamination cycles, to the quality of your copper plating, via reliability in an HDI world is becoming an ever-greater challenge. This month we look at “The Hole Truth,” from creating the “perfect” via to how you can assure via quality and reliability, the first time, every time.
In Pursuit of Perfection: Defect Reduction
For bare PCB board fabrication, defect reduction is a critical aspect of a company's bottom line profitability. In this issue, we examine how imaging, etching, and plating processes can provide information and insight into reducing defects and increasing yields.
Voices of the Industry
We take the pulse of the PCB industry by sharing insights from leading fabricators and suppliers in this month's issue. We've gathered their thoughts on the new U.S. administration, spending, the war in Ukraine, and their most pressing needs. It’s an eye-opening and enlightening look behind the curtain.
- Articles
- Columns
- Links
- Media kit
||| MENU - pcb007 Magazine
Estimated reading time: 4 minutes
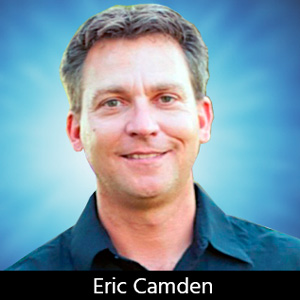
Quest for Reliability: Put Your Operators in the Driver’s Seat
There are countless ways to optimize equipment and material to increase the quality and reliability of electronics. Millions of dollars are spent every year on measurement equipment to look at solder joint quality, part placement, solder paste application, and basically every possible measurable aspect of an assembly.
One part of the process that should receive an equal amount of time and attention is staffing and training, which is this month’s topic. What a coincidence! Operator proficiency in larger contract manufacturers is most often an internal function with certified trainers overseeing classes of employees on a regular basis. From my experience, the most common type of training is IPC J-STD-001 Requirements for Soldered Electrical and Electronic Assemblies and IPC-A-610, Acceptability of Electronic Assemblies. The J-STD-001 is how you build, and IPC-A-610 is what it should look like after the product has been built.
As part of my job, I have been either a CIT or CIS for both J-STD-001 and IPC-A-610 for pretty much the last 15+ years. That is a big requirement when I am tasked with putting my hands elbow deep in your process for evaluation and optimization. Most often, the teacher is a Certified IPC Trainer (CIT) and, if they pass, the students will be a Certified IPC Specialist (CIS) with the skills to build and inspect electronic assemblies.
There are other levels of certification available to include a new certification, Certified Standards Expert (CSE), which is specific to a single standard. This makes you an “expert” on a particular standard and can give you the ability to make final referee calls. There is also the Master IPC Trainer (MIT), which is the top of the training food chain. They are the ones who certify the trainers that train the specialist.
J-STD-001 and IPC-A-610 courses do not encompass every aspect of building or inspecting electronic assemblies, but they cover most topics. If need be, you can certify inspectors to look at bare boards, wire harnesses, rework and repair, and/or design, among others. No matter the size of the CM, it is imperative to have properly trained operators on the floor doing the work and inspecting it to make sure it meets whatever acceptance criteria are called out on the drawing.
Just as important as having training done to some standard like the IPC is having the operators trained to look at your specific assembly and knowing where to start looking when something is out of control. This goes back to another column I wrote some time ago talking about tribal knowledge. In lieu of a copy/paste situation, the CliffsNotes version is the industry is constantly losing more experienced employees who have been part of the build since its inception. With age comes experience, and often, that experience includes time on the equipment used to build your product. You can’t teach experience, but you sure can write it down for others to learn from.
Assembly process equipment is often like driving a 1974 Buick Regal (which is not a random choice, by the way; that was my first car). By that, I mean it would make certain noises that I only learned the root cause of after driving it for many months ( in the off chance I heard it between Mötley Crüe songs). I knew that one certain sound meant I was low on oil. Another sound meant my tire with the constant slow leak needed a few pounds of air.
In the same way, an experienced operator knows that when they see a bad solder joint or some other anomaly, they need to look at reflow profile, belt speed, or some other parameter. That is the type of thing that IPC (or any other industry body) cannot teach. That is the definition of tribal knowledge, and it’s being lost all the time.
My point is that beyond the structured training sessions, there needs to be internal “lessons learned” training specific to your facility and equipment. Many times, this type of knowledge can play as big of a role in your product’s reliability—that, and a 1974 Buick Regal that, while reliable, requires a lot of attention to stay that way. Just like an assembly line! Whew, that was certainly a drive to connect those dots.
Staffing is the second part of this month’s topic, and having never been in the position to directly hire anyone, what I have to offer should be taken with a grain of salt. What I can say from personal experience is you don’t need to hire anyone who automatically has every skill you are looking for. I was a drywall finisher for five years before being hired at Foresite. I started as a bench tech in the chemistry lab in a time before autosamplers, which afforded a lot of time for reading up on both the electronics assembly process and at the root cause of the failures we were testing.
Even back in the early 2000s, we had a few pretty good microscopes to go along with some experienced engineers who would take time from their busy schedules to teach me a thing or two here and there when time allowed. Sure, I had the luxury of time that others might not have, but the point is to hire people with a desire to learn more about what they are doing and why, beyond just being their job. There are no bad car puns or musical memories from the 1980s here—just a recommendation to hire people who are naturally inquisitive whenever possible.
Your assembly floor managers and line operators are the first and last line that steer your reliability numbers. (I knew I could get one more in there.)
This column originally appeared in the December 2020 issue of SMT007 Magazine.
More Columns from Quest for Reliability
Quest for Reliability: Here We Go (Virtual) AgainQuest for Reliability: What’s Lurking in the Shadows?
Quest for Reliability: Reliability Starts at the Bottom
Quest for Reliability: Correlating COVID-19 With Reliability?
Quest for Reliability: Big Trouble Comes in Tiny Packages
Quest for Reliability: New Solder, Same Old Testing
Quest for Reliability: Improving Reliability for Free
Quest for Reliability: Sunshine and Circuit Boards