-
- News
- Books
Featured Books
- pcb007 Magazine
Latest Issues
Current IssueThe Hole Truth: Via Integrity in an HDI World
From the drilled hole to registration across multiple sequential lamination cycles, to the quality of your copper plating, via reliability in an HDI world is becoming an ever-greater challenge. This month we look at “The Hole Truth,” from creating the “perfect” via to how you can assure via quality and reliability, the first time, every time.
In Pursuit of Perfection: Defect Reduction
For bare PCB board fabrication, defect reduction is a critical aspect of a company's bottom line profitability. In this issue, we examine how imaging, etching, and plating processes can provide information and insight into reducing defects and increasing yields.
Voices of the Industry
We take the pulse of the PCB industry by sharing insights from leading fabricators and suppliers in this month's issue. We've gathered their thoughts on the new U.S. administration, spending, the war in Ukraine, and their most pressing needs. It’s an eye-opening and enlightening look behind the curtain.
- Articles
- Columns
- Links
- Media kit
||| MENU - pcb007 Magazine
Estimated reading time: 6 minutes
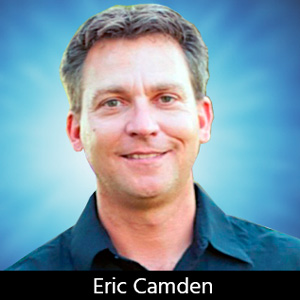
Quest for Reliability: Correlating COVID-19 With Reliability?
I submit this month’s column from my secure bunker while safely—and smartly, if I may say so myself—practicing social distancing. The word quarantine is more “popular” than ever in that I hear it upward of 4,562 times per day. Before COVID-19, the first thing that popped into my mind when I heard the word “quarantine” was the cages in the receiving area for non-conforming products or similar spaces for built hardware that doesn’t pass some sort of inline test. Having said that, I certainly don’t think of non-conforming products now, but I do think I can make some apt comparisons. Stay with me, though; some of this may be a stretch, but it’s not like I’m keeping you from a hot date.
I am certainly not suggesting that a PCB with misaligned fiducials is the same thing as a global pandemic; again, I said some of this was a stretch. But the similarity of not being part of normal production and sheltering in place isn’t that big of a stretch. Putting yourself in quarantine is to make sure you aren’t in the general population and possibly spreading the virus. Keeping bad raw materials in the quarantine cage prohibits it from being built only to find out there is a flaw that prevents it from functioning as expected—giving a PCBA a 104°F fever, if you will. (Okay, that was yet another stretch. I’ll try to do better.)
Just as the states have their list of milestones that must be accomplished before lifting the quarantine, there is (or should be) a list for material disposition. Number one on many states’ lists is the need for testing, which can certainly apply to questionable material as well. Testing might be the only way to determine if a product is acceptable for use as-is or if it needs to be returned to the manufacturer for repair and/or replacement. (I do not have a comparison for that one, so feel free to insert your own.)
When dealing with a non-conformance issue, you need to lay out a good testing strategy for disposition. Many companies—too many, if you ask me—rely on the material supplier to include a certificate of conformance with every shipment and never question it. This goes back to one of my biggest industry peeves: just checking a box. In the lab, we have tested many failures that were shipped with a certificate of conformance. What this tells me is that historical pass/fail criteria imposed by the customer or offered from the suppliers may not be sufficient for your product.
Segregation of material from standard production normally falls into one of three buckets: releasing, reprocessing/reworking, and rejecting. I mostly think of issues around quarantine to be related to incoming raw materials as they are received and go through the standard paperwork checks. You can certainly use the same word for an assembly during the build process.
Most times, the assembly in question will be segregated from the line and put into a special tray or rack for further review and disposition. When raw materials are received and don’t conform to the specs on the drawing or the purchase documents for one reason or another, that material needs to be segregated to a part of your receiving area and tagged so that it is not used in normal production until disposition is decided.
This also applies to raw materials used directly for assembly like bare boards, raw components, solder paste, and fluxes, but should also apply to anything that can have an impact on your product. Often, handling materials like gloves, finger cots, pink foam, and ESD bags are overlooked when there isn’t a direct measurement for accept or reject conditions. All of these materials will most likely come into contact with your product at some point. Any material that contacts your product will always be a risk for contamination, but that isn’t what this column is about, so I digress.
Releasing is easily the best of the three buckets, as the material will be reviewed by a supplier quality engineer (SQE) or someone similar and, if deemed acceptable for use, released into production. With incoming raw materials, the best-case scenario is a typo on the paperwork side where the shipping documents don’t match the purchase order. Remember, I don’t work in purchasing, which might be why I think that is the better option. When inspecting assemblies that have been deemed out of specification for some reason during the build process, it may be a more difficult call to just release it. Testing of some sort like functional or possibly more strenuous environmental exposure might need to be done before a decision can be made.
The second bucket—reprocessing/rework—is normally reserved for work in progress assemblies that fail some sort of ICT, visual inspection, or other end-of-line testing. An assembly that fails some inspection during the build can be sent to a rework and repair area and brought back into spec for use. Issues are caused by conditions like insufficient solder joints or misplaced components, among others.
There are many variables to consider when determining if it is acceptable or not, and many times—especially in the case of high-reliability products—rework and repair may not even be allowable. Form, fit, and function will always be the first criteria, but beyond that, it’s important to see if the customer has imposed any other metrics you need to meet. Bucket number two is normally reserved for assemblies, but it could apply to incoming raw materials too. If bare boards or components need to be cleaned before use due to some issue at the supplier, it would be considered a reprocessing/rework. This is not something I have seen on a regular basis, but we have seen it, so there’s a chance.
The last bucket is rejecting the material and returning to the supplier for replacement. This is normally the worst of all buckets. Rejecting incoming materials is never fun because that can cause delays in your build schedule while you wait for new conforming material. That is a snowball that causes a lot of issues all the way downstream.
When you have to reject an assembly and send it to scrap, the issues can be just as great. There is an added financial consideration since most or all of the components have already been installed, and it reduces the number of parts ready to be shipped. It is very important to perform root-cause analysis on any assemblies that have been rejected to determine if this is a one-off issue, or if it is something much more systemic. Systemic may be the easier of those two options since the failure would be more repeatable and most likely easier to correct, but the cost of getting to that point might be considerable.
It seems I ran out of steam on the coronavirus/reliability comparisons, and I can only assume we are both thankful for that. The point remains that keeping suspect material away from normal production until deemed fit for use will have a gigantic impact on reliability. Now go wash your hands.
This column originally appeared in the June 2020 issue of SMT007 Magazine.
More Columns from Quest for Reliability
Quest for Reliability: Here We Go (Virtual) AgainQuest for Reliability: Put Your Operators in the Driver’s Seat
Quest for Reliability: What’s Lurking in the Shadows?
Quest for Reliability: Reliability Starts at the Bottom
Quest for Reliability: Big Trouble Comes in Tiny Packages
Quest for Reliability: New Solder, Same Old Testing
Quest for Reliability: Improving Reliability for Free
Quest for Reliability: Sunshine and Circuit Boards