-
- News
- Books
Featured Books
- pcb007 Magazine
Latest Issues
Current IssueThe Hole Truth: Via Integrity in an HDI World
From the drilled hole to registration across multiple sequential lamination cycles, to the quality of your copper plating, via reliability in an HDI world is becoming an ever-greater challenge. This month we look at “The Hole Truth,” from creating the “perfect” via to how you can assure via quality and reliability, the first time, every time.
In Pursuit of Perfection: Defect Reduction
For bare PCB board fabrication, defect reduction is a critical aspect of a company's bottom line profitability. In this issue, we examine how imaging, etching, and plating processes can provide information and insight into reducing defects and increasing yields.
Voices of the Industry
We take the pulse of the PCB industry by sharing insights from leading fabricators and suppliers in this month's issue. We've gathered their thoughts on the new U.S. administration, spending, the war in Ukraine, and their most pressing needs. It’s an eye-opening and enlightening look behind the curtain.
- Articles
- Columns
- Links
- Media kit
||| MENU - pcb007 Magazine
Estimated reading time: 5 minutes
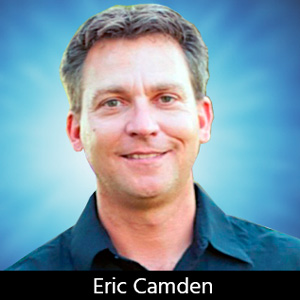
Quest for Reliability: What’s Lurking in the Shadows?
There are two terms in the electronics industry that I feel need to be in wide use. The first is an acronym for “violates minimum electrical clearance,” which is obviously, and simply, VMEC. It has always confused me why this isn’t already in heavy use. We use TLAs for everything (TLA is an acronym for three-letter acronyms, by the way).
The second term I use on a regular basis, and the focus of this month’s column, is “contamination relocation.” I use this term mostly when I test a PCBA that has gone through some sort of localized cleaning process after a manual or selective soldering operation. In most of the cases I have seen, when a no-clean flux is used, localized cleaning is a totally useless practice intended to only improve a cosmetic issue. Cosmetic issues are usually just that and don’t have any impact at all on functionality or reliability. I’d rather have an ugly, reliable board than a sparkling clean field failure.
In some cases, there are legitimate reasons to perform localized cleaning. The number one reason is if you are using a water-soluble flux for the soldering process. As with any water-soluble flux, the activators are never rendered near benign through a thermal excursion and will always be hygroscopic, as well as corrosive. That means you don’t only have to worry about electrical leakage failures. The residues can cause corrosion without any bias differential or available atmospheric moisture. That’s one reason I really like working on PCBA failures if they were built with a water-soluble flux. If you see flux residues, that’s more than likely your root cause of failure. It’s a short day, and I can go fishing in no time.
Another valid reason to perform localized cleaning is if you are planning to use conformal coating on the PCBA. Flux residues can cause adhesion issues in some cases, and if you use parylene, a full cleaning is required. You may also need to clean the residues to access test points if you’re not using a probable flux. Sensitive RF circuits can also be affected by flux residues and need to be removed to ensure proper operation. I think that pretty much exhausts the good reasons to perform localized cleaning. It’s not a long list. Please note that cosmetic appearance did not make the list.
What is lurking in the shadow? It is most likely active flux residues spread around by the localized cleaning process. And much like a teenager standing on your porch, trying to score some candy from you by stuffing a few pens in their shirt pocket and saying they’re a nerd, you just don’t want that. And ouch, by the way, that’s just rude. This month, I want to highlight localized cleaning that is performed correctly and incorrectly and the impact on cleanliness and reliability.
I often go into a production facility for a process review and see operators using an acid brush of questionable cleanliness dipped in IPA scrubbing away after a manual soldering process and then inspecting the area of concern for residues. If none are found, they simply pass the boards down the line for subsequent processing. What I never see is that the same operator looking in the adjacent areas for residues. Those areas are the shadows I mentioned. In almost every case, you can’t inspect monolayers for residue under components with low standoff height for some time.
That same low standoff height makes them very difficult to clean under the best of circumstances. When you add IPA or other solvents to the flux residue, all that does is make it soluble. What it does not do is magically make detrimental flux residues disappear like many seem to think it does. Don’t believe me? Let’s look at some ion chromatography (IC) data from a field failure.
Touch-up soldering was done to an SMT component, and according to the work instruction, this process includes a quick cleaning with IPA. The boards are already built with no-clean flux, but any touch-up requires cleaning. Figure 1 shows the SMT part that was cleaned, as well as the capacitor and PTH pins that were tested.
The IC data in Table 1 shows low levels of ionics at the SMT location, but much higher levels are now present in the other two areas. Performing localized cleanliness testing was key to shining light on those “shadows.” The chemical signature shows that the flux uses a weak organic acid, and at these levels in the PTH/capacitor, areas are at an increased risk of electrical leakage or even dendrite growth. This same board was put through an inline wash process, and the second set of IC data shows acceptable levels of ionics across the board.
A large batch of boards processed like this had to be recovery cleaned before shipping to the customer because of that increased reliability risk. It’s what we had to do to get that darn teenager off the porch. This method of localized cleaning is like running your vacuum without a bag, or you could also say contamination relocation. Please say it as a matter of fact. It’s my "Git-r-done" if you will. The similarities stop there.
The good news is there is a simple way to enhance this same basic cleaning method while reducing the spread of IPA and solubilized residues onto neighboring components. Instead of dipping the end of the acid brush into a bottle, soak a lab wipe with IPA and then place that wipe over the area that needs to be cleaned. Then, you use the brush on top of that wipe to clean as normal (Figure 2). The wipe will absorb the flux/solvent mixture (Figure 3), not allowing the solution to transfer to neighboring components and become a potential risk for electrical leakage in the field.
The wipe is then simply discarded. It’s important that a new wipe is used for each individual cleaning process. A wipe or brush will collect residue over time, so using a new wipe eliminates cross-contamination. As with any assembly process, you need to create objective evidence that the process is effective using some sort of cleanliness or environmental exposure testing.
Conclusion
It might be close to Halloween, but there isn’t any reason to be afraid of what your cleaning process is doing to reliability if you shine enough light on the process. And should teenagers try and haunt your porch this year, give them full-size candy bars instead of a hassle. Everyone likes candy.
This column originally appeared in the October 2020 issue of SMT007 Magazine.
More Columns from Quest for Reliability
Quest for Reliability: Here We Go (Virtual) AgainQuest for Reliability: Put Your Operators in the Driver’s Seat
Quest for Reliability: Reliability Starts at the Bottom
Quest for Reliability: Correlating COVID-19 With Reliability?
Quest for Reliability: Big Trouble Comes in Tiny Packages
Quest for Reliability: New Solder, Same Old Testing
Quest for Reliability: Improving Reliability for Free
Quest for Reliability: Sunshine and Circuit Boards