-
- News
- Books
Featured Books
- smt007 Magazine
Latest Issues
Current IssueMoving Forward With Confidence
In this issue, we focus on sales and quoting, workforce training, new IPC leadership in the U.S. and Canada, the effects of tariffs, CFX standards, and much more—all designed to provide perspective as you move through the cloud bank of today's shifting economic market.
Intelligent Test and Inspection
Are you ready to explore the cutting-edge advancements shaping the electronics manufacturing industry? The May 2025 issue of SMT007 Magazine is packed with insights, innovations, and expert perspectives that you won’t want to miss.
Do You Have X-ray Vision?
Has X-ray’s time finally come in electronics manufacturing? Join us in this issue of SMT007 Magazine, where we answer this question and others to bring more efficiency to your bottom line.
- Articles
- Columns
- Links
- Media kit
||| MENU - smt007 Magazine
Estimated reading time: 6 minutes
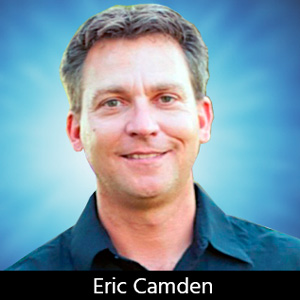
Cleaning a No-clean Flux: The Worst Decision You’ve Ever Made?
Cleaning a no-clean flux is not a task for the uninitiated or uneducated; it is a task for those who like to run into brick walls with blindfolds on. It can be as fun as it sounds, or with the proper knowledge and a little experience, it can be merely terrible.
There are a few reasons to choose to clean a no-clean flux (and even fewer are actually good reasons). One good reason to clean is when the assembly requires conformal coating, especially when using Parylene. Another reason is when probes are required for testing. The flux residue can inhibit a good contact surface. Other than that, I struggle to think of another good reason to clean a no-clean flux.
From where I sit here in the failure analysis (FA) lab, the main reason for cleaning no-clean is that if flux residues are not fully removed, what is left behind will be of no concern since they were intended to be left fully intact to begin with. As an employee at an analytical test lab with kids to send to college, I couldn't agree more—no further research is necessary. As an objective observer, there are several problems with this theory (which we will touch on in this month's installment).
Let's start with a brief explanation of no-clean flux. Traditional water-soluble flux formulations have approximately 10–40% solids. Flux activators at these levels might burn through the containers they are shipped in if not used within a week or two after receiving them, so they need to be cleaned right away. These residues can be effectively removed with a standard in-line wash process using only high-quality deionized (DI) water, or with the addition of a saponifier to lower the surface tension to get under low-standoff components such as quad-flat no-leads (QFNs) and other bottom-terminated components (BTCs).
Some companies have made the switch to no-clean flux because they can use the same wash parameters as with water soluble. Let me reiterate that I have kids to send to college, so I won't argue too much with this position. The problem with this approach is the fact that no-clean flux formulations use either rosin or resin to help bind any oxides and contamination from the surface of the metallized surfaces to be soldered. The rosin also acts as a "poor man's coating" because it is a retardant for moisture ingression when properly processed. That last part is very important because if any of the chemistries are left in an active state, it is hygroscopic. Given enough time and available atmospheric moisture, it is possible to set up an electrical leakage path and eventually electrochemical migration.
When no-clean flux is not properly processed with sufficient thermal exposure to render it near benign, it remains active. If you ineffectively clean it, you open the active part directly to the atmosphere. I always equate this to ripping off a bandage and exposing a wound. I have seen a shift from the component manufacturers to assemble certain parts, like QFNs, with only no-clean flux because they are aware of the difficulty in cleaning under those.
Now that I’ve covered why it’s a terrible idea to try and clean no-clean flux, let’s discuss some of the most effective ways I have found to achieve this fool’s errand. As previously mentioned, every effective wash process requires a high-quality DI water system. The minimum quality should be in the resistivity range of 10 megaohms—not 2-megaohm dummy light water—because as soon as the DI water hits the air, the resistivity drops, which isn’t as good of a solvent. Many wash machines have an onboard resistivity measurement system so consider making 10 megaohms the lower end for acceptable wash water.
You will also need to introduce some sort of cleaning chemistry to your system. This will aid in reducing the surface tension and help to soften those residues that hardened after assembly—even more so with higher temperature lead-free processes. The higher the reflow/wave solder temperature, the more difficult the residues are to remove. There are a number of high-quality options for a saponifier. Consult your cleaning chemical supplier to determine the best chemistry for your specific flux and assembly process.
The next thing to think about is the wash parameters. The temperature of the wash and rinse solutions should be around 60°C. This will further lower the surface tension of the solution. The spray pressures shouldn’t be so high because they atomize immediately and lose much of their energy. High volume, low pressure is a good rule to wash by. This means using larger openings on your spray nozzles—around 2.0 gpm is a good place to start—to soak the assemblies and create more of a horizontal flow pattern. This will keep the flux exposed to the chemistry and allow it to better soften and remove better than 400-PSI blasters. Spray nozzle impingement angles should be canted about 20° inward on both the entry and exit bars to help increase the horizontal flow of the wash and rinse solutions. This is necessary to help clean under those pesky BTCs.
Belt speed is another important consideration because if you have gone through all the trouble of increasing the nozzle flow and pressures, if you whip assemblies through at 5.0 FPM to increase throughput, you effectively negate all the other work. I have found that 2.0 FPM is about as fast as you want to push product through to give the chemistry time to do its job. It’s all about exposure time to the thermal and chemical energy combination.
These are general recommendations, and as with all assembly materials, it may vary depending on your actual product. It’s important to remember that none of the material suppliers know exactly what you are building. When their tech data sheets show a recommended profile or application, it is just that—a recommendation. After cleaning no-clean flux processed assemblies, it is also important to do some destructive physical analysis. You will need to mechanically remove some parts to take a closer look at the interface between the pads and component bodies. This is where the vast majority of flux residue will remain if it is to be found. Removing a few QFNs on the actual product and instead of just testing the boards is a great place to start. I recommend focusing on these parts because they are so difficult to clean; if you are successful, the rest will most likely fall in line.
Further, it is highly recommended to use ion chromatography on the parts and pads to determine the amount of each specific ion used in the flux activator. You won’t necessarily be able to see the residues; it may look fine but could still have a thin film invisible to the naked eye or someone looking through a microscope. You will most likely be able to see no-clean flux residue because it normally absorbs moisture from the wash process and will have a milky haze. If you see this hazy residue, go back and start optimizing your wash parameters, such as slowing the belt speed, increasing the percentage of chemistry, temperatures, etc. You will find the sweet spot, and once you do, remember it is most likely only going to be effective for that specific board style.
Much like swimwear, one size does not fit all.
More Columns from Quest for Reliability
Quest for Reliability: Here We Go (Virtual) AgainQuest for Reliability: Put Your Operators in the Driver’s Seat
Quest for Reliability: What’s Lurking in the Shadows?
Quest for Reliability: Reliability Starts at the Bottom
Quest for Reliability: Correlating COVID-19 With Reliability?
Quest for Reliability: Big Trouble Comes in Tiny Packages
Quest for Reliability: New Solder, Same Old Testing
Quest for Reliability: Improving Reliability for Free