-
- News
- Books
Featured Books
- smt007 Magazine
Latest Issues
Current IssueMoving Forward With Confidence
In this issue, we focus on sales and quoting, workforce training, new IPC leadership in the U.S. and Canada, the effects of tariffs, CFX standards, and much more—all designed to provide perspective as you move through the cloud bank of today's shifting economic market.
Intelligent Test and Inspection
Are you ready to explore the cutting-edge advancements shaping the electronics manufacturing industry? The May 2025 issue of SMT007 Magazine is packed with insights, innovations, and expert perspectives that you won’t want to miss.
Do You Have X-ray Vision?
Has X-ray’s time finally come in electronics manufacturing? Join us in this issue of SMT007 Magazine, where we answer this question and others to bring more efficiency to your bottom line.
- Articles
- Columns
- Links
- Media kit
||| MENU - smt007 Magazine
Estimated reading time: 5 minutes
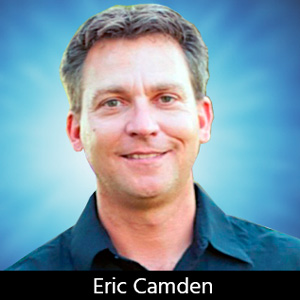
Are Megatrends Putting Your Product at Megarisk?
"Mega" is a fun word to use because it elicits thoughts of grandeur and impressiveness regarding the topic at hand. From megaton to megalomaniac, when you use "mega" as a prefix, you know it's going to be big. A simple trend can only speak to two or three things going in the same direction, but a megatrend is a completely different ball game. In my exhaustive research (one hour on the Internet, so I am officially an expert), I found this fact in a paper by two researchers from Finland: “It took 38 years for radio to get 50 million users, television made it in 13 years, Internet in four, iPod in three, and Facebook in only two years”. As a dad of a 10-year-old son, I would guess that Fortnite made it to 50 million in about 12 minutes.
What these numbers mean to our industry is the need to create electronics at blazing speeds that we haven’t seen before. I have seen customers increase their demand on throughput without any thought to how that will affect reliability. If it takes one hour at 350°C to bake a cake, why can’t we do it in 30 minutes at 700°C and get the same quality? I wish it worked that way, but it doesn’t—trust me.
When the demand is higher than normal, you can’t simply increase the belt speed on your soldering equipment and expect to make the same high-quality product. To be fair, the majority of handheld or consumer electronics fall into the Class I category, which aren’t necessarily that reliable to start for long term, on-demand use. In the Class II and Class III world, it’s a megadifferent story. For example, demands for safety and hardware reliability in the military and aerospace segments are everything.
Assembly parameters are traditionally determined using manufacturers recommendations, trial-and-error methods, and in some cases, tribal knowledge. No matter how you go about that task, the important part is to look at supporting analytical data. No-clean flux is a prime example of a material that needs to be exposed to enough thermal energy for enough time to render the residues near benign. When you increase the belt speed to increase numbers, you will also alter the chemical composition after reflow soldering.
A few years ago, I put together a study to determine the effect of speeding up the belt on a reflow oven on cleanliness. With the first group of test boards, I used the manufacturer’s recommendation—maximum ramp of
Table 1: Ion chromatography for the first group of test boards.
With the second group of test boards, I used a belt speed of 2.0 FPM and a peak temperature 10°C lower than the manufacturers recommendation. The integrated circuit (IC) analysis in Table 2 shows elevated ionic content that is meant to be outgassed under temperature or fully bound in the outer resin/rosin shell of the flux. Ionic content at these levels increases the risk for electrical leakage with normal available atmospheric moisture.
The increase of belt speed will pump out more parts, but at what cost? Being able to produce more parts in the same amount of time is always going to look great to the customer but needs to be judged against the amount of returns with “no-trouble-found” (NTF) designations or hard failures. NTF is a megabad condition because when a part fails in the field, it can’t be reproduced, which makes finding the root cause nearly impossible. When a part returns to a repair depot, the low hanging fruit becomes items such as missing components, ICs that needs to be flashed, or beer stains on the board—you know, standard stuff you see from field returns.
Table 2: Ion chromatography for the second group of test boards.
Active flux residues aren’t something you can see under a scope at 10x. You can see flux residues, but visual inspection alone isn’t enough to determine if they are conductive or corrosive. When a board gets labeled with the NTF designation, many times, it’s chalked up as a loss with no further follow up. That is most likely because the active flux residues will absorb loads of moisture and create an electrical leakage plate that will disappear as soon as the moisture dries out during shipping. The repair depot looks at the return and everything seems to be in working order. This condition will only increase with the act of increasing throughput without doing any of the hard work to determine if it’s detrimental to the product.
However, there are probably parameters that will allow you to increase the throughput while not producing PCBAs that aren’t megaquestionable. Increasing the temperature in the preheat zone is one way to do it, but it’s important to look at the recommended rise rate from the manufacturer of the flux and the component manufacturers. Sudden increases in temperature can crack some types of components, including LEDs, aluminum capacitors, fuses, inductors, and transformers with wire coils. It will do you no good to increase the throughput if you are destroying the components.
Using a thermal profile system on the actual product is the only way to effectively monitor the temperatures at locations that are known to be temperature sensitive. Using a bare board or thermocouples in air will tell you what the temperature is in the oven, but not what the actual temperature is on your product. This will certainly be a trial-and-error effort until you find the sweet spot of throughput, acceptable solder joints, and benign flux residues.
The megatakeaway from this month’s column is the final reliability level of an assembly relies heavily on the thermal profile used for soldering. When the peak temperature is too low, excess amounts of active flux residues are left behind, and when ample moisture is available from a normal operating atmosphere or from condensing moisture anomalies, there is a greater risk of failure due to electrical leakage and/or electrochemical migration. Active no-clean flux residues are conductive in general and when moisture is absorbed into the residue across non-common conductors, voltage easily flows between the two. This is why it’s so important to monitor the effect of your throughput speeds when ramping up to meet the 50 million requested pieces to support the megatrends in the electronics industry.
I want to close with a megapology for using the word “mega” incorrectly so many times. As I said, it’s a mega fun word to say.
More Columns from Quest for Reliability
Quest for Reliability: Here We Go (Virtual) AgainQuest for Reliability: Put Your Operators in the Driver’s Seat
Quest for Reliability: What’s Lurking in the Shadows?
Quest for Reliability: Reliability Starts at the Bottom
Quest for Reliability: Correlating COVID-19 With Reliability?
Quest for Reliability: Big Trouble Comes in Tiny Packages
Quest for Reliability: New Solder, Same Old Testing
Quest for Reliability: Improving Reliability for Free