-
- News
- Books
Featured Books
- design007 Magazine
Latest Issues
Current IssueProper Floor Planning
Floor planning decisions can make or break performance, manufacturability, and timelines. This month’s contributors weigh in with their best practices for proper floor planning and specific strategies to get it right.
Showing Some Constraint
A strong design constraint strategy carefully balances a wide range of electrical and manufacturing trade-offs. This month, we explore the key requirements, common challenges, and best practices behind building an effective constraint strategy.
All About That Route
Most designers favor manual routing, but today's interactive autorouters may be changing designers' minds by allowing users more direct control. In this issue, our expert contributors discuss a variety of manual and autorouting strategies.
- Articles
- Columns
- Links
- Media kit
||| MENU - design007 Magazine
Estimated reading time: 2 minutes
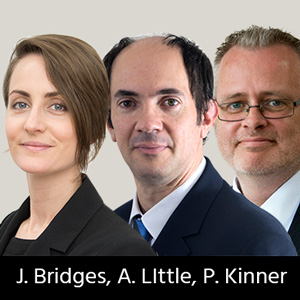
Resins: Cutting Through the Technical Jargon
You only have to visit my company’s website to find out that resins come in many forms, with a list of properties that would challenge even a chemist graduate. Well, I do appreciate that most PCB manufacturers have little time to dwell on the subtleties—they just want a resin that will do the job. But with so many products on offer, how do you find time to wade through the jargon, make your choice and be confident that it will perform as expected?
Unquestionably, product detail is important to the user and will be his or her initial guide to making an appropriate choice; however, this month, I’m going to cut through some of the more heavy-going tech-speak, taking a few of my customers’ more frequently asked questions about resins to try to help you refine your selection process. There’s a lot of ground to cover, but for the purposes of this column, let’s concentrate on the PCB’s operating environment, caring for the components that are to be encapsulated, and the special needs of applications like LED lighting and RF systems.
Q. What exactly constitutes “general purpose” protection? Can we take this to mean that a general-purpose resin will meet most environmental conditions, or should we be more cautious if the operating environment is a little more challenging?
A. “General purpose” means that the resin offers good protection against the effects of temperature and humidity over a broad range, as well as providing good resistance to a wide range of chemicals. They also provide protection against vibration and shock, but when it comes to making a choice, you will need to be specific about the resin chemistries—polyurethane or epoxy—as they differ in terms of the types of protection they offer. In general, polyurethanes are better at protecting against vibration/cyclic mechanical shock and thermal cycling within an operating temperature range, as they retain their flexibility over their working life. Epoxies, on the other hand, can tolerate higher operating temperatures than polyurethanes, but they are more rigid and brittle when cured. While they are able to withstand higher mechanical shock, they are not as effective under conditions of high vibration or cycling shock.
Q. What are the main parameters to consider when making a resin selection and what pitfalls should I look out for?
A. The size and geometry of a PCB assembly are important parameters to consider before you choose an encapsulation/potting resin. Size will dictate the required usable life and gel time of a two-part resin, and it will also have quite a big impact on cure time.
Usable life and gel time data are typically calculated on a 100g mix size at room temperature (20-23°C). Short gel times are good for rapid turnaround of units, but may cause problems by allowing air to be released; long gel times, on the other hand, can extend production cycle times and introduce bottlenecks into the manufacturing process.
It is important to note here that very small volumes of resin will take longer to cure and special care should be taken to ensure that the correct mix ratio is maintained. In the case of larger volumes of resin, while the cure times will be reduced, the user must consider the corresponding rise in temperature of the resin/hardener mix, the “exotherm,” which may be high enough to damage vulnerable components. Epoxy resins are much more exothermic than polyurethanes.
To read this entire column, which appeared in the July 2017 issue of The PCB Design Magazine, click here.
More Columns from Sensible Design
Sensible Design: Automotive Conformal Coating ApplicationsSensible Design: Green Coats Are In
Sensible Design: Encapsulation Resins—PU vs. Epoxy
Sensible Design: Avoiding Conformal Coating Pitfalls
Sensible Design: Comparing Traditional and Bio-based Resins
Sensible Design: All Resins Are Not Created Equal
Sensible Design: Can Solvent-free UV-cure Coatings Increase Stability and Throughput?
Sensible Design: Optimize Your Thermal Management