-
- News
- Books
Featured Books
- smt007 Magazine
Latest Issues
Current IssueMoving Forward With Confidence
In this issue, we focus on sales and quoting, workforce training, new IPC leadership in the U.S. and Canada, the effects of tariffs, CFX standards, and much more—all designed to provide perspective as you move through the cloud bank of today's shifting economic market.
Intelligent Test and Inspection
Are you ready to explore the cutting-edge advancements shaping the electronics manufacturing industry? The May 2025 issue of SMT007 Magazine is packed with insights, innovations, and expert perspectives that you won’t want to miss.
Do You Have X-ray Vision?
Has X-ray’s time finally come in electronics manufacturing? Join us in this issue of SMT007 Magazine, where we answer this question and others to bring more efficiency to your bottom line.
- Articles
- Columns
- Links
- Media kit
||| MENU - smt007 Magazine
Estimated reading time: 4 minutes
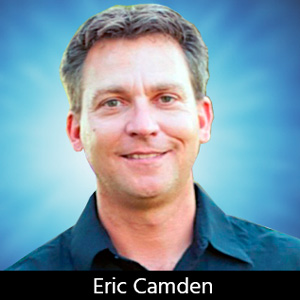
Are You Connected to Reliability?
The topic this month is the Connected Factory Exchange (CFX)—the IPC initiative for manufacturers to become smart factories. From my understanding, the underlying thought for CFX is communication from business to machine and machine back to business. CFX will help streamline parts of the assembly process related to supply and projected throughput. But how will CFX help with reliability?
As someone who works more often on the back end of the assembly process diagnosing failures or qualifying the assembly process to specific requirements, I have no idea. I can tell you that in both of those avenues, communication is key. The need for communication between every operator on the floor can be a critical difference between a reliable piece of hardware and one that presents some level of unexpected performance. Every time an operator does something out of the ordinary in the assembly process, doesn’t make a note of it in a way that can be traced back to the PCBA by its serial number, and that piece of hardware comes back for a performance issue, it is very easy to be lumped into the dreaded “no trouble found” (NTF). Since I don’t have a strong tie to speak directly to reliability and CFX, I will instead cover a few things not commonly communicated, which can cause performance issues.
Figure 1: Liquid flux used for rework.
Touch-up soldering is something I have seen many times during regular process audits. The assembly comes off the reflow or wave solder equipment, and the inspector sees something that doesn’t meet the requirement. Easy fix, right? Just grab some wire and fix the solder joint. However, the problem with this particular solder joint is the fact it ties to a large thermal mass, so a little wire won’t do the job. The operator can fix this by grabbing a bottle of flux from the bottom drawer to help that solder to do its job.
The problem is this becomes a different rework process than what is in the work instruction. While the solder joint is now acceptable, the amount of flux residue could be drastically different than what is typically present after using only a cored wire solder. When a bottle of flux is used to help speed up the normal rework process, you will see an increase in the amount of active flux residues. Figure 1 shows how liquid flux migrates into the neighboring component, and if there is no contact with the soldering iron, it will remain conductive and corrosive. Further, Table 1 shows the high levels of ions on the surface of the PCBA, which significantly increases the risk for electrical leakage and/or electrochemical migration.
The secondary risk is increased contact time with the solder iron to the PCB. This can cause internal delamination within the fiberglass and if your board is multilayer—which it probably is—delamination can cause connectivity issues between the internal interconnects, such as vias and ground pads. If the deviation from the standard touch-up process isn’t communicated in some form, the failure mode will most likely remain a mystery upon the return of the hardware to the failure analysis (FA) lab.
The next issue you might see on a semiregular basis is called the “third shift issue” that occurs when you see a group of boards with performance issues processed within a single shift. In general, the third shift has less oversight from production managers than the first or second shift, so the chances of deviations from the normal process occurring and not being documented are higher. I am not saying the operators on the third shift are any less qualified to build production assemblies, but the lack of oversight sometimes leads to a lack of reporting issues and “creative resolutions”. Don’t get me wrong—creativity is important—but can be devastating to the reliability of your hardware. The documentation of any deviation from the normal assembly process is paramount to track any returns and root causes of failure.
Table 1: Ion chromatography data showing active flux residues.
One other issue more often seen on the third shift versus other shifts is ramping up the belt speed to meet an expected production number. This is sometimes done when the expected numbers of boards to be produced isn’t lowered when the number of operators is reduced. I wrote about this in a previous column (so I won’t go into the full details now), but when you increase the belt speed of any piece of assembly equipment, the quality will suffer from active flux residues, insufficient hole fills, and ineffective cleaning, among other issues. I want to reiterate that I am not saying all failures are related to those working the third shift, but these problems seem to be communicated to quality managers or documented for future reference less often.
When a failure comes back to an internal or external lab for inspection, it is much easier to diagnose the root cause if the full process is communicated and documented. With a fully documented procedure from the kitting process to final packaging, you can communicate in a language of reliability.
This column originally appeared in the October 2018 issue of SMT007 Magazine.
More Columns from Quest for Reliability
Quest for Reliability: Here We Go (Virtual) AgainQuest for Reliability: Put Your Operators in the Driver’s Seat
Quest for Reliability: What’s Lurking in the Shadows?
Quest for Reliability: Reliability Starts at the Bottom
Quest for Reliability: Correlating COVID-19 With Reliability?
Quest for Reliability: Big Trouble Comes in Tiny Packages
Quest for Reliability: New Solder, Same Old Testing
Quest for Reliability: Improving Reliability for Free