-
- News
- Books
Featured Books
- design007 Magazine
Latest Issues
Current IssueProper Floor Planning
Floor planning decisions can make or break performance, manufacturability, and timelines. This month’s contributors weigh in with their best practices for proper floor planning and specific strategies to get it right.
Showing Some Constraint
A strong design constraint strategy carefully balances a wide range of electrical and manufacturing trade-offs. This month, we explore the key requirements, common challenges, and best practices behind building an effective constraint strategy.
All About That Route
Most designers favor manual routing, but today's interactive autorouters may be changing designers' minds by allowing users more direct control. In this issue, our expert contributors discuss a variety of manual and autorouting strategies.
- Articles
- Columns
- Links
- Media kit
||| MENU - design007 Magazine
Estimated reading time: 2 minutes
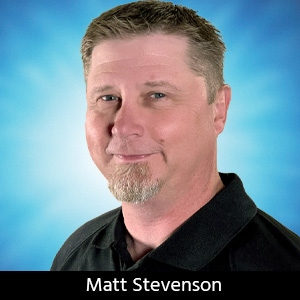
Connect the Dots: Six Tips to Ensure Parts Fit on Your Board
“Will my parts fit on the board?” That seems like an easy enough question to answer as you transition from the design stage to manufacturing, but issues with parts fitting are one of the most frequent causes of delays and cost overruns. We see it every day. Designs are submitted that can’t or shouldn’t be manufactured because the parts will not fit properly. This creates issues with performance and durability—effectively reducing the overall quality of the board.
The six following tips will help you avoid common parts-related manufacturability pitfalls.
1. Avoid Pinhole Pitfalls
It’s essential t to check component physical dimensions, consider dimension tolerances, and account for variations that could impact fit. Pins could be the wrong size or have the wrong spacing, and components could be much larger than their footprint or land pattern might indicate. Further, alternative or replacement components could be on the wrong end of the tolerance range. After all, it just takes a few mils before things don't fit and assembly starts going wrong. Finding a good alternative part can be a challenge, which is why datasheets can be your best friends. In addition to watching part sizes, pay close attention to the minimum, nominal, and maximum material conditions for the original part.
2. What to Do When the Land Pattern and Pin Size Differ
One of the most frustrating mismatches with alternative through-hole parts occurs when the land pattern matches, but the pin size is off. If hole sizes are too tight, pins may not fit through the holes, or if they do go into the holes, they may not solder well. Solder will need to flow through the gap between the pin and the hole barrel. If there is not enough space to allow enough solder mass to flow through the hole, the circuit board will absorb heat from the molten solder and cause the solder to solidify partway up the hole. This is called a cold solder joint and can result in a premature failure of your circuit.
To avoid this issue, make sure that when you design your land pattern, you know the pin size and tolerance range for your components. With that information, you can plan the proper hole size. Component holes should be sized correctly to allow 12–16 mils in diameter larger than the component pin at maximum material condition (MMC). MMC is the condition where the hole is drilled at the low end of the tolerance range and the pin measures at the high end of the tolerance range. Pin locations should be placed at nominal locations or the basic dimensions shown on the datasheet.
To read the rest of the column, which appeared in the November 2018 issue of Design007 Magazine, click here or download the PDF here.
More Columns from Connect the Dots
Connect the Dots: How to Avoid Five Common Causes of Board FailureConnect the Dots: Sequential Lamination in HDI PCB Manufacturing
Connect the Dots: The Future of PCB Design and Manufacturing
Connect the Dots: Proactive Controlled Impedance
Connect the Dots: Involving Manufacturers Earlier Prevents Downstream Issues
Connect the Dots: Stop Killing Your Yield—The Hidden Cost of Design Oversights
Connect the Dots: Designing for Reality—Routing, Final Fab, and QC
Connect the Dots: Designing for Reality—Surface Finish