-
- News
- Books
Featured Books
- design007 Magazine
Latest Issues
Current IssueProper Floor Planning
Floor planning decisions can make or break performance, manufacturability, and timelines. This month’s contributors weigh in with their best practices for proper floor planning and specific strategies to get it right.
Showing Some Constraint
A strong design constraint strategy carefully balances a wide range of electrical and manufacturing trade-offs. This month, we explore the key requirements, common challenges, and best practices behind building an effective constraint strategy.
All About That Route
Most designers favor manual routing, but today's interactive autorouters may be changing designers' minds by allowing users more direct control. In this issue, our expert contributors discuss a variety of manual and autorouting strategies.
- Articles
- Columns
- Links
- Media kit
||| MENU - design007 Magazine
Estimated reading time: 2 minutes
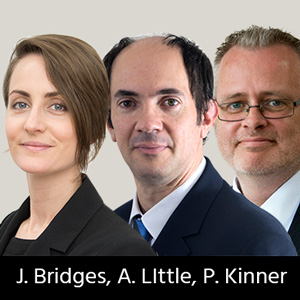
Top Five Tips to Protect PCBs from Harsh Environments
Last month, I began my new series of columns on encapsulation resins by selecting five frequently asked customer questions regarding resin chemistries and properties, and typical resin applications and their limitations. In this column, I’m taking this introduction a step further by listing what I believe are the top five tips for circuit designers and manufacturers who seek to ensure that the in-service reliability and longevity of their electronic assemblies and products are fully addressed.
Five Top Tips
1. First, think very carefully about the sort of environment your PCB is likely to encounter. It is easy to over-engineer a product so that it will survive the very worst of conditions, but worst conditions may only be fleeting or transient. Therefore, a resin solution with a lower temperature performance specification will often cope. Take temperature extremes as an example; your application may experience occasional temperature spikes of up to 180°C, which you might feel deserves treatment with a special resin. However, such excursions may only be short-lived. Under normal operating conditions, the PCB might only be subjected to a maximum temperature of 120°C, opening up a wider choice of resin types and methods of application.
Similarly, the required chemical resistance of your chosen resin will depend on the duration and/or extent of the chemical contamination. For example, there is a considerable difference in terms of the extent of chemical damage between a thin layer of a contaminating chemical on the resin surface that is wiped off within five minutes, and 500 ml of a chemical present on the resin surface for one hour or more. Complete immersion takes the requirements to an even higher level. Furthermore, the range of chemicals that a PCB might eventually be exposed to is often quite limited, and almost certainly not the broad range that is frequently listed at the design stage just to be on the safe side.
2. Environmental factors that normally affect a PCB include temperature, chemical attack, physical shock (vibration), and thermal shock. The trick is to decide which of these is likely to have the greatest impact upon your PCB and then concentrate on making an appropriate resin choice. Each of the three main resin types (epoxy, polyurethane, and silicone) have strong points as well as weaknesses.
Silicone resins have the broadest continuous operating temperature range of any of the resin chemistries, so they are a natural choice for both high- and low-temperature applications as well as those subject to thermal shock. They also maintain their flexibility over this temperature range with very little sign of degradation over time. On the downside, silicones have poor adhesion on certain substrates, and their chemical resistance is not as good as that provided by an epoxy resin.
As well as offering excellent chemical resistance, epoxies provide good temperature performance. However, due to their rigid nature, epoxies are not as good at protecting against physical shock. Polyurethanes, on the other hand, have excellent moisture and physical shock resistance but deliver poor high-temperature performance. As a result, polyurethanes are best restricted to applications operating in the -40 to +120°C region. However, they do provide similar levels of flexibility and better adhesion to many substrates compared with silicones at a lower cost.
To read this entire column, which appeared in the December 2018 issue of Design007 Magazine, click here.
For detailed information on this subject, download The Printed Circuit Assembler's Guide to... Conformal Coatings for Harsh Environments.
More Columns from Sensible Design
Sensible Design: Automotive Conformal Coating ApplicationsSensible Design: Green Coats Are In
Sensible Design: Encapsulation Resins—PU vs. Epoxy
Sensible Design: Avoiding Conformal Coating Pitfalls
Sensible Design: Comparing Traditional and Bio-based Resins
Sensible Design: All Resins Are Not Created Equal
Sensible Design: Can Solvent-free UV-cure Coatings Increase Stability and Throughput?
Sensible Design: Optimize Your Thermal Management