-
- News
- Books
Featured Books
- smt007 Magazine
Latest Issues
Current IssueMoving Forward With Confidence
In this issue, we focus on sales and quoting, workforce training, new IPC leadership in the U.S. and Canada, the effects of tariffs, CFX standards, and much more—all designed to provide perspective as you move through the cloud bank of today's shifting economic market.
Intelligent Test and Inspection
Are you ready to explore the cutting-edge advancements shaping the electronics manufacturing industry? The May 2025 issue of SMT007 Magazine is packed with insights, innovations, and expert perspectives that you won’t want to miss.
Do You Have X-ray Vision?
Has X-ray’s time finally come in electronics manufacturing? Join us in this issue of SMT007 Magazine, where we answer this question and others to bring more efficiency to your bottom line.
- Articles
- Columns
- Links
- Media kit
||| MENU - smt007 Magazine
Estimated reading time: 8 minutes
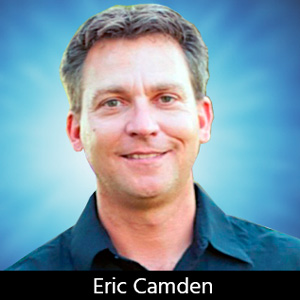
The Effect of Thermal Profiles on Cleanliness and Electrical Performance
This month, my column will cover “The Effect of Thermal Profiles on Cleanliness and Electrical Performance.” This paper was originally published in the SMTA International proceedings of 2014 (and is reprinted here with permission), but the topic is timely and worth continuing the conversation here.
Introduction
The process of thermal profiling for reflow soldering is one of the most important considerations when setting assembly parameters. Knowing how to effectively profile includes choosing the proper equipment, understanding the results and being able to adjust as necessary. Consideration for some larger multilayer assemblies and assemblies with large thermal mass components should be made to ensure that all areas of the assembly reach the minimum recommended temperature for proper solder joint formation as well as rendering no-clean flux residues benign. A review of the assembly drawing is necessary to determine if there are heavy copper layers in select areas. The heavier layers of copper will absorb heat away from the surface of the assembly. This can lead to cold and brittle solder joint defects.
Characteristics of Profile
Figure 1: Example lead-free reflow profile phases.
There are four different phases or zones to analyze under the reflow curve (Figure 1). The first is the preheating slope (temperature ramp rate), then preheat dwell (soak time), followed by time above liquidus that will include the peak temperature, and lastly, the cooling zone.
For the paste flux used in this trial, the preheat slope should be controlled to
The preheat dwell phase is where the flux activators remove oxides and prepare the metal surfaces for joining with the solder paste. This phase brings the entire assembly with components to a common temperature below the melting point of the solder. This temperature is typically maintained for 60–90 seconds for most paste types.
Figure 2: Umpire two test board.
The reflow phase is when the intermetallic formation is made. The temperature is commonly anywhere between 20–40°C above the melting point of the solder. Time above liquidus can vary between 30–90 seconds depending on thermal mass and other material choices.
The cooling zone helps determine the integrity of the solder joint grain structure. A quicker cool down ramp, in comparison to the preheat phase ramp, is normally desired but take care not to exceed the CTE of components and board surface. A common recommendation for cooling ramp rate is no more than 4°C per second.
More detailed information can be found in the IPC-7530: Guideline for Temperature Profiling for Mass Soldering (Reflow and Wave) Processes.
Profiling Equipment
There are several choices of reflow profiling equipment available depending on the need. There are profilers for either the product or the reflow oven. For this study, I will focus on only the product profiling equipment that travels with the product, thus eliminating the need for long wires that run the length of the oven. The product profiler should be capable of measuring multiple locations on the assembly. Most commercially available traveling type profilers have up to six separate thermocouples. Some have real-time measurements sent to a receiver on a computer display, and others use internal memory to store the data points for downloading after the product exits the reflow oven. Either type can yield the desired analysis.
Design of Experiment
Multiple thermal profiles were used for this experiment to determine what effect temperature has on cleanliness and electrical resistance measurements. Cleanliness was measured using ion chromatography (IC) and surface insulation resistance (SIR) testing is performed in an environment of 40°C and 90% relative humidity with 5V bias with measurements made every 10 minutes. All test boards are the Umpire two qualification test board (Figure 2).
Figure 3: Group 1 thermal profile.
The first thermal profile was 20° below the recommended limit. The second profile group was done at 10° below the recommended limit. Meanwhile, the third profile group was done at the manufacturer’s recommended profile for the solder paste. This is what is considered the minimum allowable temperature for proper solder joint formation and full flux activation. The fourth profile was done at 10° above the recommended limit.
Table 1: IC data for Group 1.
Ten boards were processed for each profile group, and of the 10, five were tested with IC; the remaining five from each group were subjected to SIR testing. Each board was measured at four different locations including an LCC, TQFP, BGA, and a non-populated row of headers for reference.
Figure 4: SIR results for Group 1.
Analysis Techniques
As previously mentioned, the experiments involved two kinds of analysis techniques: IC and SIR testing.
All IC testing was performed using a Dionex ICS 3000 chromatography system with Chromeleon software. The extractions were performed using an automated localized extraction technique. The parts were all mechanically removed, and the samples were taken from the board level. Localized extractions are of utmost importance as they do not normalize out pockets of contamination across the full surface area of the assembly like other extraction and test methods do. A raw sample of the chosen solder paste was tested with IC to determine the main constituents of the paste activator. All samples were compared to the raw paste IC data when determining the level of ionic cleanliness.
The SIR testing was performed in a standard environmental chamber capable of maintaining a temperature within ±1°C and relative humidity within 3%. A calibrated automatic switching measurement system was used for the electrical measurements taken once every 10 minutes.
Thermal Profile Group 1
The first thermal profile group was processed at a worst-case temperature of 20° below what is recommended by the solder paste manufacturer. This is a profile that barely achieves liquidus state of the paste and could be a function of multiple failing heating sources, an improper recipe being used (possible a standard leaded profile), or other unknowns (Figure 3).
Group 1 IC Results
The raw paste IC sample shows that acetate, chloride, lithium, sodium, ammonium, and potassium are the ions of highest concentration, and also of highest concern after each reflow profile variation. This worst-case profile shows highly elevated levels of acetate, chloride, lithium, and sodium. The ammonium and potassium levels depreciate greatly with this profile (Table 1).
Group 1 SIR Results
Group 1 SIR results show that all samples fail the IPC limits of 1.0e8 ohms of resistance (Figure 4).
Thermal Profile Group 2
Group 2 is a much more realistic profile than Group 1 that shows the effect of the flux residues left behind on the analysis when the temperatures are only 10° below the recommended limits. However, 10° variability is not out of the question for larger thermal mass boards and components and emphasizes the importance of profiling the assembly as well as the equipment. The equipment must also be tested to ensure that all heating elements are functioning properly. See Figure 5 for the thermal profile, Table 2 for IC data, and Figure 6 for SIR data.
Figure 5: Group 2 thermal profile.
Table 2: IC data for Group 2.
Figure 6: SIR results for Group 2.
Group 2 IC Results
The IC results for Group 2 shows lower levels of most ionics, but most are still above the recommended limits. In particular, the acetate, lithium, and sodium ions are still at a level that will increase the risk of failure in a normal field service environment.
Group 2 SIR Results
All locations with components failed both the SIR criteria as well as the recommended IC limits. The header (non-populated) area did pass both SIR and IC testing due to the lack of thermal mass.
Thermal Profile Group 3
The manufacturer recommends a maximum ramp of
Figure 7: Group 3 thermal profile.
Table 3: IC results for Group 3.
Figure 8: SIR results for Group 3.
Group 3 IC Results
The manufacturer recommended profile renders all of the flux activators benign in the areas tested with and without components. Looking at the profile for Group 3, all of the areas reached at least 246°C which is within the recommended range of 25–45° above the melting point of the solder.
Group 3 SIR Results
All locations with and without components passed the acceptance criteria. The data in Figure 8 shows that at no time did the resistance measurement dip below the 1.0e8 ohms of resistance. This indicates that in a normal field service environment without excessive available atmospheric moisture, the product should not fail when voltage is applied.
Thermal Profile Group 4
The final group was processed at a peak temperature of 260°C to determine what, if any, effect additional thermal energy has in relation to cleanliness and SIR performance. The preheat and cooling ramp are still within the recommended limits (Figure 9).
Figure 9: Group 4 thermal profile.
Group 4 IC Results
The additional thermal energy did not significantly reduce the level of ionics beyond the peak temperature of 250°C. Adding thermal energy can actually be detrimental and induce damage conducing certain types of components. The data in Table 4 shows similar levels to that of Group 3.
Table 4: IC results for Group 4.
Group 4 SIR Results
All locations with and without components passed the acceptance criteria, much as with Group 3. The data in Figure 10 shows that at no time did the resistance measurement dip below the 1.0e8 ohms of resistance. This indicates that in a normal field service environment without excessive available atmospheric moisture, the product should not fail when voltage is applied.
Figure 10: SIR results for Group 4.
Conclusions
The final reliability of an assembly relies heavily on the thermal profile used for soldering. When the peak temperature is too low, excess amounts of active flux residues are left behind. Further, when ample moisture is available from a normal operating atmosphere or from condensing moisture anomalies, there is a greatly increased risk of failure due to electrical leakage and/or electrochemical migration.
Active no-clean flux residues are conductive in general, and when moisture is absorbed into the residue across non-common conductors, voltage easily flows between the two. When processing assemblies with a water-soluble flux, or when cleaning no-clean flux, there is a failsafe for removing the conductive residues. Processing with no-clean flux types does not allow for any excess of contamination from any of the selected materials such as PCBs and components. One of the few things that can be controlled in an effort to reduce overall cleanliness and quality is the reflow process.
Future Work
With the myriad of different no-clean flux formulas, a larger study that includes more types is in order to determine the effect of thermal energy on different types of chemistry used as flux activators.
More Columns from Quest for Reliability
Quest for Reliability: Here We Go (Virtual) AgainQuest for Reliability: Put Your Operators in the Driver’s Seat
Quest for Reliability: What’s Lurking in the Shadows?
Quest for Reliability: Reliability Starts at the Bottom
Quest for Reliability: Correlating COVID-19 With Reliability?
Quest for Reliability: Big Trouble Comes in Tiny Packages
Quest for Reliability: New Solder, Same Old Testing
Quest for Reliability: Improving Reliability for Free