-
- News
- Books
Featured Books
- smt007 Magazine
Latest Issues
Current IssueMoving Forward With Confidence
In this issue, we focus on sales and quoting, workforce training, new IPC leadership in the U.S. and Canada, the effects of tariffs, CFX standards, and much more—all designed to provide perspective as you move through the cloud bank of today's shifting economic market.
Intelligent Test and Inspection
Are you ready to explore the cutting-edge advancements shaping the electronics manufacturing industry? The May 2025 issue of SMT007 Magazine is packed with insights, innovations, and expert perspectives that you won’t want to miss.
Do You Have X-ray Vision?
Has X-ray’s time finally come in electronics manufacturing? Join us in this issue of SMT007 Magazine, where we answer this question and others to bring more efficiency to your bottom line.
- Articles
- Columns
- Links
- Media kit
||| MENU - smt007 Magazine
Estimated reading time: 7 minutes
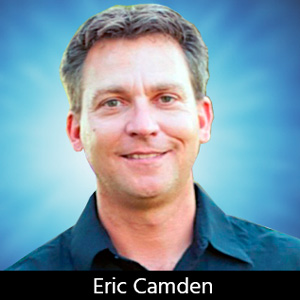
Quest for Reliability: The F Word
This month’s topic is failures and reliability, and I can’t think of two words as diametrically opposed as these two. The word “failure” is as nasty as it gets in our world. It goes against everything we thought we knew. All contract manufacturing facilities strive to build a reliable product, or at least they all should. The problem is too many companies hope they are building reliable products without doing the work required to ensure they are. This is not uncommon, nor is it specific to the electronics industry, but as consumers, we sure know when a company didn’t take the time to do reliability testing. Some companies simply don’t care about reliability because even though their product isn’t necessary for us to live, we simply can’t live without it (I’m looking at you, Comcast).
In our industry, reliability is a must for almost all companies, so testing is normally written into drawings and contracts, but is that enough? Or is it just checking a few historical boxes without any thought? We often see legacy products that have been updated as older parts have become obsolete, or as a result of design changes, but the testing requirements haven’t been updated since we found out who shot J.R.
Looking at today’s electronics with package miniaturization and more complex circuitry, you may need to go beyond what you’ve always done. While we are on that topic, “That is how we’ve always done it,” should be removed from your company’s vocabulary. Historical testing does not necessarily mean it’s still relevant or applicable to what you are building today. You need to assess the end-use environment and power demands to determine what testing should be carried out to ensure reliability. Obviously, safety-critical and life-dependent hardware must go through more rigorous testing than a PC, so there is no one-size-fits-all suite of testing.
Many times, the only verification testing I see being done on bare boards is dimensional measurements. This is a good test and should continue. At a minimum, the next test should be an analysis of the stackup using cross-section. Many PC fabrication shops will send a cross-section puck sample with each lot. However, most of the time, I see them tucked away in a drawer in a bag stapled to a CofC, but they have not been examined by the customer. Believe it or not, a file cabinet does not take any measurements. One of the main issues with simply filing away a CofC and a puck is building product under the assumption that what the PC fabrication shop sent aligns with the print requirement. Only when a failure is detected does anyone go back and examine what was sent. Plenty of CMs do the work and examine the puck, but I can also say it certainly isn’t all of them. You know who you are.
Another very important test for bare boards is cleanliness testing of some sort with historical data or objective evidence to back up your acceptance criteria. This process is now clearly defined in the IPC J-STD-001 Amendment 1. This is especially important if your product is built with no-clean flux as there is not an end-of-assembly wash process to make up for sins upstream. If you start with a dirty bare board, you may experience issues related to electrical leakage or electrochemical migration that have nothing to do with your assembly process, so it’s best to know up front if you’re fighting an uphill battle.
There are many other tests you can perform on bare panels, which can be found in the IPC 4000 and 6000 series documents with IPC-A-600 as a visual reference guide. Depending on the end-use environment, there may be a much larger suite of test you need to perform. This needs to be discussed with the PCB supplier and customer.
Once you are satisfied that you are getting what you asked for regarding the bare boards, it’s time to move on to your assembly. Material selections are often done using test coupons and some sort of elevated heat and humidity testing, which is a great idea. Surface insulation resistance (SIR) testing per IPC TM-650 2.3.6.7 has become a go-to test for determining how well your equipment can process the fluxes and what effect elevated heat and humidity will have, The idea is to either leave behind residues that are near benign or fully removed in the case of water-soluble flux types. There are also material compatibility tests for conformal coating, potting, adhesives, underfill, etc. It’s important to know what effect different materials will have on the product. Not all materials play well together, so if you plan to coat or use some other type of surface encapsulation, these tests can be very useful and eliminate a potential issue before it manifests in a failure.
After all of the materials have been selected, it is time to move on to building your PCBAs and even more testing to see what your reliability risk is based on all of the choices and testing done up to this point. Of course, there’s more testing; there’s always more testing if you care about reliability. Again, you can look to IPC for a myriad of testing and need to consider the end-use environment when determining exactly what test you need, but I will cover a few of what we consider to be the most important tests are. The IPC documents you need to review are J-STD-001 and the companion IPCA-610 for visual acceptance. These documents are a great reference tool if you have any questions about the assembly process. And no, I don’t work for IPC, but I do spend time in task group meetings making a small contribution to help make the decisions that ultimately go into the assembly documents.
One of the first tests I recommend is ion chromatography to determine the level of cleanliness after assembly. IC will tell you the exact type and amount of ionic contamination, which is crucial when determining the risk for failures related to electrical leakage or electrochemical migration. There are many ways to perform extractions for IC analysis, but one of the most important things to remember is that contamination is not evenly distributed across the entire surface of the assembly.
Historical testing using resistivity of solvent extract (ROSE) as well as standard IC extractions will show a result as if the contamination is indeed the same over each square inch. Each soldering process will introduce its own chemical signature into the final level of cleanliness, and only by looking at much smaller areas of the board will you know for sure what each process brings to the table. There are many ways to do localized extractions, and each has a unique set of benefits and drawbacks, so each method should be examined to determine which is right for your specific application. When you know just how much residue each process is adding, you can then directly address that part of the process to optimize and reduce the amount of active contamination. Excessive active residues will easily absorb atmospheric moisture and facilitate electrical leakage.
The next test I always recommend is thermal, humidity, and bias (or THB) testing. This process involves placing fully assembled product into an environmental chamber at elevated heat and humidity with a fixture that supplies nominal power to the samples and some expected output is measured over the course of 500 or 1,000 hours to get the best possible idea of what to expect in a normal field service environment. This is as close to the rubber meeting the road as you can get because this is 100% representative of your full process. All of the testing you’ve done to this point should give you an idea of what to expect from this type of testing. If you’ve made good decisions up to THB, you should see very good results.
These are the basic blocks of testing that I recommend at a minimum to cover, assess, and increase reliability. Of course, this doesn’t cover every test you might need to consider. If your product is an under-hood application, you may need to add a vibration test. If it’s going into a harsh environment, you may consider a mixed flow gas test. The list of applicable tests might grow, or you might be good with some of the basics I have mentioned here, but testing everything on the way to your final product is always a better strategy for reliability than having to react to the F word.
Eric Camden is a lead investigator at Foresite Inc.
This article was initially published in the July 2019 issue of SMT007 Magazine.
More Columns from Quest for Reliability
Quest for Reliability: Here We Go (Virtual) AgainQuest for Reliability: Put Your Operators in the Driver’s Seat
Quest for Reliability: What’s Lurking in the Shadows?
Quest for Reliability: Reliability Starts at the Bottom
Quest for Reliability: Correlating COVID-19 With Reliability?
Quest for Reliability: Big Trouble Comes in Tiny Packages
Quest for Reliability: New Solder, Same Old Testing
Quest for Reliability: Improving Reliability for Free