-
- News
- Books
Featured Books
- smt007 Magazine
Latest Issues
Current IssueMoving Forward With Confidence
In this issue, we focus on sales and quoting, workforce training, new IPC leadership in the U.S. and Canada, the effects of tariffs, CFX standards, and much more—all designed to provide perspective as you move through the cloud bank of today's shifting economic market.
Intelligent Test and Inspection
Are you ready to explore the cutting-edge advancements shaping the electronics manufacturing industry? The May 2025 issue of SMT007 Magazine is packed with insights, innovations, and expert perspectives that you won’t want to miss.
Do You Have X-ray Vision?
Has X-ray’s time finally come in electronics manufacturing? Join us in this issue of SMT007 Magazine, where we answer this question and others to bring more efficiency to your bottom line.
- Articles
- Columns
- Links
- Media kit
||| MENU - smt007 Magazine
Estimated reading time: 2 minutes
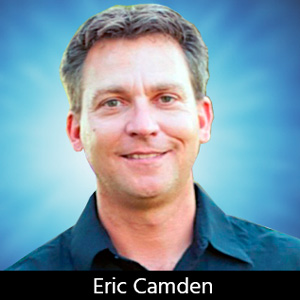
Quest for Reliability: Reliability by the Book
Standards have been around in the industry as long as the industry itself. But if they are followed, does that mean that you’ll have improved reliability? The answer is a famous one in certain circles; it depends on a few things, such as the product’s intended use and warranty. If you are building something that must work only as it leaves the facility and is considered a Class I product, then reliability isn’t something you need to worry about. But having been in electronics for just shy of 20 years, I can say that the next time we work on a Class I failure analysis project, it will pretty much be the first. Class I electronics serve a different purpose in life, and if they fail, it’s normally not a big deal; instead, it’s mainly a minor inconvenience. In this month’s column, I’ll speak to specifications for Class I, II, and III products per IPC definitions as well as the IPC standards process.
Class I, II, and III
The low-cost materials and disposable nature of Class I products basically preclude them from ever being labeled as high-reliability. Within IPC guidelines for Class I, the assembly guidelines are very different than Class II or Class III. This isn’t necessarily a knock on Class I products by any means. IPC’s definition for Class I is “includes products suitable for applications where the major requirement is the function of the completed assembly.” There’s not a single word about reliability or critical nature of their intended use.
Class II is defined as dedicated service electronic products, which “includes products where continued performance and extended life is required, and for which uninterrupted service is desired but not critical. Typically, the end-use environment would not cause failures.” Class II products would be found in a lot of automotive electronics, not related to safety, as well as harsh environment electronics that may not necessarily be life-critical but are expected to operate for 20+ years.
Class III is defined as “products where continued high performance or performance-on-demand is critical, equipment downtime cannot be tolerated, the end-use environment may be uncommonly harsh, and the equipment must function when required, such as life support or other critical systems.” These electronics are most commonly found in industries like healthcare and aerospace. When your life, or the life of others, is on the line, Class I simply won’t do.
The standards for assembling Class II and III are well known with IPC J-STD-001 being the cornerstone of the J-STD series of standards. J-STD-001 is titled “Requirements for Soldered Electrical and Electronic Assemblies,” which covers a lot of ground. The Technical Activities Executive Committee (TAEC) says, among other things, that standards should focus on the end-use environment, not tell you how to make something. That last part is very important to remember because standards aren’t the full recipe necessary to build electronics; they should be considered a guideline to reference when there is uncertainty on how to do some part of the process. The order of precedent on any drawing should be as agreed between the user and the supplier and standards like J-STD. This helps to drive home the point that IPC standards are not necessarily the final word on how to build a PCBA, but should be used as a companion to the demands of the customers.
To read this entire column, which appeared in the September 2019 SMT007 Magazine, click here.
More Columns from Quest for Reliability
Quest for Reliability: Here We Go (Virtual) AgainQuest for Reliability: Put Your Operators in the Driver’s Seat
Quest for Reliability: What’s Lurking in the Shadows?
Quest for Reliability: Reliability Starts at the Bottom
Quest for Reliability: Correlating COVID-19 With Reliability?
Quest for Reliability: Big Trouble Comes in Tiny Packages
Quest for Reliability: New Solder, Same Old Testing
Quest for Reliability: Improving Reliability for Free