-
- News
- Books
Featured Books
- smt007 Magazine
Latest Issues
Current IssueSupply Chain Strategies
A successful brand is built on strong customer relationships—anchored by a well-orchestrated supply chain at its core. This month, we look at how managing your supply chain directly influences customer perception.
What's Your Sweet Spot?
Are you in a niche that’s growing or shrinking? Is it time to reassess and refocus? We spotlight companies thriving by redefining or reinforcing their niche. What are their insights?
Moving Forward With Confidence
In this issue, we focus on sales and quoting, workforce training, new IPC leadership in the U.S. and Canada, the effects of tariffs, CFX standards, and much more—all designed to provide perspective as you move through the cloud bank of today's shifting economic market.
- Articles
- Columns
- Links
- Media kit
||| MENU - smt007 Magazine
Estimated reading time: 4 minutes
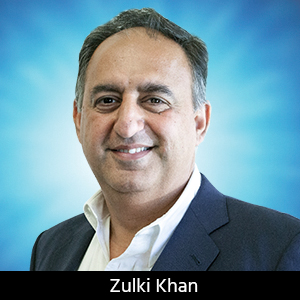
Zulki’s PCB Nuggets: Successful PCB Microelectronics Assembly
So far, I’ve discussed a variety of PCB microelectronics subjects. However, I haven’t covered one of the most crucial areas: PCB fabrication that creates the circuit board undergoing microelectronics assembly. OEMs need to carefully consider fabrication for their products that are assembled via the PCB microelectronics route.
The burning question is, “Why is fabrication vitally important when it comes to successful microelectronics assembly?” Keep in mind that PCBs going through microelectronics assembly are considerably more special due to the intricacies involved. That includes the utmost precision required for placing a bare die on the circuit board and the critical cleanliness of the board before and after a bare die is attached.
In effect, fabrication is vital because it serves as the base on which the total and successful microelectronic assembly process depends. For starters, a fabrication shop producing PCBs for microelectronics assembly should, at the minimum, have ISO 9001 certification, so it has the infrastructure in place to produce quality PCBs. And it’s all the better if the fabricator has additional qualifications like ISO 13485, AS9100, and/or some mil/aero certifications.
Aside from these certifications, fabricating PCBs for microelectronics assembly demands excellence in three major areas: board and substrate co-planarity, process flow and control, and verification. In simple terms, co-planarity refers to the PCB or substrate surface being 100% uniform or non-planar. This is where surface finishes come into the picture to determine which ones are completely uniform or not for microelectronics assembly. Candidates include leaded or lead-free hot air solder leveling (HASL), Entek, also known as organic solderability preservative (OSP), immersion silver, electroless nickel immersion (ENIG), and electroless nickel/electroless palladium/immersion gold (ENEPIG).
Leaded or lead-free HASL is out the door right away because it is the most uneven surface finish. Entek, or OSP, poses two major issues: corrosion, and it’s not suitable for proper microelectronics assembly because it does not have peel strength to properly hold wire bond pads in place. Likewise, immersion silver is prone to corrosion.
ENIG and ENEPIG are the two surface finishes that are acceptable; of the two, ENEPIG is the absolute best surface for microelectronics assembly. OEMs can live with ENIG. Ideally speaking, however, ENEPIG is the better of the two because it’s very co-planar with gold-to-gold contact. Also, there’s excellent conductivity between gold wire to the gold surface finish. Plus, there’s heat transfer rate, and adhesion is robust and occurs quickly.
Next is process flow and control efficiency and how they impact the success of microelectronics assembly. The PCB layout or IC design engineer creates the necessary specifications for pad definitions with appropriate tolerances listed; he or she then provides them in the form of fabrication notes. These notes define the best ways to fabricate a board.
Take fabrication tolerances, for example. Figure 1 shows the inconsistencies of two to three pads that should be equal in dimensions but are not. As shown, Pad #3 is only 0.060 mm while Pad #2 is 0.069 mm, a difference of over 12% in pad dimensions.
In this case, the PCB layout engineer didn’t spec out the exact tolerances, which is routinely done in regular PCB manufacturing. Regular SMT manufacturing requires a ±1 mil, which is typically very tight tolerance-wise. The absolute maximum is the standard ±3 mils.
In microelectronics, tolerances are measured in microns rather than in mils, which is standard for SMT manufacturing. In microelectronics assembly, 1–2 mils could be too large of a tolerance to optimally perform these bonds. It also means avoiding the solder mask from encroaching on the bond pad, which is absolutely prohibitive. Laser direct imaging (LDI) is a methodology that is used for assuring that the solder mask is properly aligned with the bond pad. This allows die attach and wire bonding to be correctly performed.
Also, fiducial marks are of utmost importance for both SMT and microelectronics assembly. They are crucial for defining data point locations for component placement as part of the PCB SMT assembly. For microelectronics, a bare die should have fiducial marks because they allow the programmer or process engineer to perform the die-attach programming. This programming is based on a bond-pad diagram the OEM customer provides.
Precision in the pick-and-place operation is another point to make in defining process control. Consider specific areas from which to pick and place a die. For example, there can be a lens, sensor, or perhaps a camera function on a bare die. Hence, there is no discretion as to picking up that particular die. If it gets picked up from the lens or sensor area, the pick-and-place operation can damage the complete die even if highly precise tools are used. In those cases, those particularly sensitive areas on a die must be clearly defined in assembly descriptions and notes to avoid die damages.
Moreover, in the process flow and control area, an EMS provider must have in place an incoming fabrication quality control check. That is important because the QC check immediately determines the good from the bad PCBs. There can be a range of deficiencies and problems, including marginal boards in terms of pad size, solder mask issues, co-planarity, and/or contaminations, among others.
Lastly, after completing the microelectronics assembly, including die attach and wire bonding, there is a verification process. This is the critical step to ensure that assembly was properly performed. Highly advanced and sophisticated tools, like a Keyence digital microscope, are ideal for their very precise measuring capabilities, inspection, and verification for die-attach and wire-bond applications. These verification features are necessary to detect virtually any defect in the whole manufacturing process that is not visible using regular inspection tools.
Therefore, EMS providers engaged in PCB microelectronics must have on their assembly lines verification tools like this. High-caliber verification tools and disciplined inspection methodologies enhance the overall capabilities for performing successful microelectronics assembly.
Zulki Khan is the president and founder of NexLogic Technologies Inc.
More Columns from Zulki's PCB Nuggets
Zulki's PCB Nuggets: Cleanliness is Next to ReliabilityZulki’s PCB Nuggets: Thermal Compression Bonding for Extra Fine Pitch Flip Chips
Zulki’s PCB Nuggets: WBAN Steps Into PCB Microelectronics Assembly
Zulki’s PCB Nuggets: Photonics Comes to PCB Microelectronics Assembly
Zulki’s PCB Nuggets: Sub-Micron Die Bonding—Don’t Be Misled by Five Micron Placement Standard
Zulki’s PCB Nuggets: Meet the New Player in PCB Microelectronics Assembly—Interposers
Zulki’s PCB Nuggets: How Effective Is Your PCB Microelectronics Assembly?
Zulki’s PCB Nuggets: Five Key Benefits for Onshoring PCB Microelectronics Assembly