-
- News
- Books
Featured Books
- design007 Magazine
Latest Issues
Current IssueProper Floor Planning
Floor planning decisions can make or break performance, manufacturability, and timelines. This month’s contributors weigh in with their best practices for proper floor planning and specific strategies to get it right.
Showing Some Constraint
A strong design constraint strategy carefully balances a wide range of electrical and manufacturing trade-offs. This month, we explore the key requirements, common challenges, and best practices behind building an effective constraint strategy.
All About That Route
Most designers favor manual routing, but today's interactive autorouters may be changing designers' minds by allowing users more direct control. In this issue, our expert contributors discuss a variety of manual and autorouting strategies.
- Articles
- Columns
- Links
- Media kit
||| MENU - design007 Magazine
Estimated reading time: 1 minute
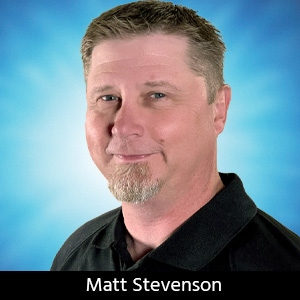
Connect the Dots: A Penny for Your Thoughts on Copper
I know what you’re thinking: “He can’t possibly write an entire article dedicated to the use of copper in PCBs.” I say, “Hold my beer.”
Copper is the primary metal for standard PCBs, which you can find in pretty much every type of electronic device on the planet. And while standard PCB capabilities depend on what materials are used and how they are constructed, copper is the go-to choice.
Copper works very well for the conduction of electrical current in any environment. In fact, it has the highest electrical conductivity rating of all non-precious metals, making it highly effective for performance and cost. For a vast majority of PCB designs, copper is the conductor of choice. Copper conducts the signal and power for just about every electronic item in your life.
Way to go, copper! You are doing a great job. Keep it up.
There are, however, challenges associated with its use. Though incredibly conductive, copper is a relatively soft metal and susceptible to corrosion. Insufficient copper-to-edge clearances can result, potentially causing exposed copper, shorts, or corrosion. Resist can flake off of very narrow traces. During etching, long slivers can wander around in the bath. These loose cannons of conductivity can affix themselves to a board, keeping unwanted copper from being etched away, creating unwanted circuits and failed boards.
So, how do you get copper to function in a nice, orderly manner the way your design calls for it? First, keep an eye out for potential problems during the design phase. To properly control resistance and temperature rise, use a PCB trace width calculator to determine how thick and wide traces need to be. If your board is large enough, wider traces increase reliability. Skinny traces can get hot and release all of your magic smoke. Once it gets out, it’s really hard to put back in.
To read this entire column, which appeared in the November 2019 issue of Design007 Magazine, click here.
More Columns from Connect the Dots
Connect the Dots: How to Avoid Five Common Causes of Board FailureConnect the Dots: Sequential Lamination in HDI PCB Manufacturing
Connect the Dots: The Future of PCB Design and Manufacturing
Connect the Dots: Proactive Controlled Impedance
Connect the Dots: Involving Manufacturers Earlier Prevents Downstream Issues
Connect the Dots: Stop Killing Your Yield—The Hidden Cost of Design Oversights
Connect the Dots: Designing for Reality—Routing, Final Fab, and QC
Connect the Dots: Designing for Reality—Surface Finish