-
- News
- Books
Featured Books
- design007 Magazine
Latest Issues
Current IssueProper Floor Planning
Floor planning decisions can make or break performance, manufacturability, and timelines. This month’s contributors weigh in with their best practices for proper floor planning and specific strategies to get it right.
Showing Some Constraint
A strong design constraint strategy carefully balances a wide range of electrical and manufacturing trade-offs. This month, we explore the key requirements, common challenges, and best practices behind building an effective constraint strategy.
All About That Route
Most designers favor manual routing, but today's interactive autorouters may be changing designers' minds by allowing users more direct control. In this issue, our expert contributors discuss a variety of manual and autorouting strategies.
- Articles
- Columns
- Links
- Media kit
||| MENU - design007 Magazine
Estimated reading time: 4 minutes
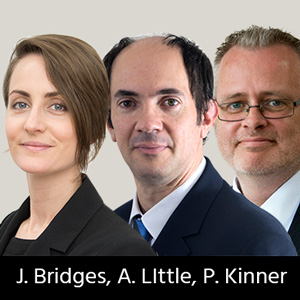
Sensible Designs: Resins—Five Tips for Potting and Performance
In recent columns, I have outlined various resin properties and how they relate to particular types of circuit protection, seen ?how to apply these resins in a production environment by deciding on which mixing and application techniques are appropriate to ?specific production needs, and explored various resin subtleties, such as how best to achieve a satisfactory cure. Nevertheless, readers continue to ask, “Does thicker coverage achieve better performance? What is the best advice for manual potting? We chose an inappropriate resin, so how will this affect our application?” In this column, I will explore these and other issues based upon frequently asked questions from Electrolube’s customers.
In no particular order, here are five questions that raise a number of technical issues allied to resin applications, together with my responses. Hopefully, it will provide useful background information to help you with your own resin-related activities.
1. What are some examples of a critical application, and how do these differ from non-critical?
Normally, the phrase “critical application” is used when referring to safety-critical systems. These are applications that will not only seriously impact on the user and their organization but also potentially result in serious environmental damage, injury, or loss of life if they malfunction. Examples of critical applications include aircraft; automotive and railway operating and control systems; emergency lighting; burglar and fire alarm systems; medical equipment required by doctors, nurses, and surgeons; as well as power grid systems and first responder communication systems. Non-critical applications are normally where if a failure occurs, lives are not immediately at risk. If we look at potential malfunctions within automotive applications, the brakes would be considered critical, and climate control would be considered non-critical.
2. I have heard mention of some resins containing glass beads (or similar). Why would these be required and offer some potential applications?
Glass beads are added to resins for a number of different reasons. They can be used as a filler to produce a low density, chemical resistant resin, which is good for weight critical applications. They also control the minimum resin thickness that can be applied. Aesthetically, glass and/or plastic beads can be used to provide a matt surface to resins or, in the case of optically clear resins, a diffused effect when light is passed through. An example is the UR5635 two-part, flexible polyurethane potting compound, which has been formulated to provide a light-diffusing effect for LEDs. It offers a unique light diffusion effect thanks to its cloudy appearance and has been used to great success as an?LED?potting compound for both decorative and protective applications.
3. What are some key pointers to remember when manually potting?
Think about the amount of resin that you are going to need and across how many units. If there are a large number of units, and a large amount of resin required, it is often better to use a number of small-sized resin packs, as you will have better control over the potting process. If a large resin pack is used, then due to the volume of material, once mixed, the resin will start to cure over a shorter time-scale compared to a small volume pack. Consider where to place the resin so that it can flow around and under the components. With thixotropic resins, it is more critical, as the resin is purposely designed to have a low flow when applied.
4. Does thicker coverage equal better performance?
The simple answer to this is yes. In general, they do perform better; however, there will be a point at which increasing the resin thickness will not offer any significant gain in performance. This heavily depends on the specifics of the application and the resin used. Generally, a thicker resin layer is better if high levels of chemical resistance are required, particularly in the case of long-term immersion or for high voltage systems to increase long-term performance. Considering the variation in height of components on a PCB, the thinnest coating thickness needs to be taken as being representative across the entire unit rather than the average. In the case of physical shock, a thicker layer of resin can help to protect the components and dissipate forces better than a thin layer. The major downside with increasing the resin thickness is the increase in weight and volume occupied by the encapsulated board.
5. What are the potential issues to be faced by selecting an inappropriate resin for a particular application?
Okay, there’s no dancing around the issue here; the simple answer is a premature failure. Choosing the correct resin is not as easy as it may seem, as there are so many variables to consider, such as typical operating conditions, expected extremes, the size and geometry of the units, the need for repair, the expected service life, etc. If the resin is too brittle, it can crack during operation and expose the electronics to potentially harmful chemicals. If the unit is expected to undergo cyclic thermal shock during its service life, then a flexible resin would be advised, but it depends on the maximum and minimum temperature expected. There is a lot of difference between –60 to +60°C and +40 to +160°C; both are a 120°C temperature difference, but for one, a polyurethane resin would be recommended, while for the other, epoxy would be better.
Conclusion
If ever in doubt, refer to the technical data sheets (TDS); these can be a great help when you embark on a new design or production schedule with new components and resins. However, if you do anticipate any glitches with matching resin types to your production procedures and find it hard to resolve this from the TDS, please contact your supplier’s technical support team for further advice. Next time, I will take an in-depth look at some of the most frequently asked questions fielded by our Technical Support Team and explore options to fully address these enquiries.
This column originally appeared in the March issue of Design007 Magazine, click to view.
More Columns from Sensible Design
Sensible Design: Automotive Conformal Coating ApplicationsSensible Design: Green Coats Are In
Sensible Design: Encapsulation Resins—PU vs. Epoxy
Sensible Design: Avoiding Conformal Coating Pitfalls
Sensible Design: Comparing Traditional and Bio-based Resins
Sensible Design: All Resins Are Not Created Equal
Sensible Design: Can Solvent-free UV-cure Coatings Increase Stability and Throughput?
Sensible Design: Optimize Your Thermal Management