-
- News
- Books
Featured Books
- design007 Magazine
Latest Issues
Current IssueShowing Some Constraint
A strong design constraint strategy carefully balances a wide range of electrical and manufacturing trade-offs. This month, we explore the key requirements, common challenges, and best practices behind building an effective constraint strategy.
All About That Route
Most designers favor manual routing, but today's interactive autorouters may be changing designers' minds by allowing users more direct control. In this issue, our expert contributors discuss a variety of manual and autorouting strategies.
Creating the Ideal Data Package
Why is it so difficult to create the ideal data package? Many of these simple errors can be alleviated by paying attention to detail—and knowing what issues to look out for. So, this month, our experts weigh in on the best practices for creating the ideal design data package for your design.
- Articles
- Columns
- Links
- Media kit
||| MENU - design007 Magazine
The Cost of Inefficient Production of PCB Documentation
May 13, 2020 | Mark Gallant, DownStream TechnologiesEstimated reading time: 5 minutes
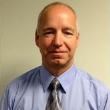
Editor’s note: The following article is an excerpt from Chapter 5 of the I-Connect007 eBook The Printed Circuit Designer’s Guide to… Documentation, written by Mark Gallant of DownStream Technologies.
Most EDA software providers have enhanced their tools by integrating new functionality and broadening their offerings through acquisition. Core EDA tools—including schematic capture, digital and analog simulation, PCB design, autorouters, and many others—have matured and have dramatically reduced time to market. However, implementing automated features for creating PCB documentation has been largely ignored by PCB CAD tool providers. As a result, PCB CAD tools are inherently inefficient for the final and critical phase of the PCB design process—creating documentation.
Creating comprehensive PCB documentation is a requirement in all electronics companies. If the end product is destined for a military or aerospace user, the documentation requirements increase considerably. Even in applications where accurate documentation is critical, much of it is created using CAD drafting features that have not improved since the CAD revolution of the 1980s. PCB CAD tools are superlative at reducing the PCB design cycle but fall short on some of the most basic documentation tasks.
For example, PCB design tools selling for tens of thousands of dollars per seat lack basic spellcheck features found in a $99 word processor. Most PCB CAD tools lack support for a paragraph requiring the creation of multiline text strings for fabrication or assembly notes. Countless hours are spent using rudimentary drafting tools to create layer stackups, PCB detail views, or drill charts one segment or line at a time.
These antiquated documentation methods impede the drafting workflow most often during a design re-spin. Drill quantities out of sync in a manually drawn drill chart? Select the text string and edit the value. Layer stackup changes? Manipulate the layer graphics and text to update the stackup. Does the PCB detail view need updating because a component moved on the PCB? Either recapture the entire view or start editing the graphics one vertex or one segment at a time. All of these manual updates are time-consuming and subject to human error.
Engineering organizations that use popular MCAD tools to complete the PCB documentation have additional encumbrances. MCAD tools are usually superior to ECAD tools with respect to creating documentation. However, the conversion of the design to MCAD file formats results in disassembling of the intelligent ECAD data. Part outlines are converted to shapes, traces to lines, copper shapes to polygons, etc. Creating tables, notes, and complex dimensions is certainly quicker in MCAD, but gleaning intelligent data for a parts list is mostly impossible. Should a design re-spin be required, the MCAD drawings must be recreated or manually updated with new design content. This drawback also introduces an MCAD design database to an already overcrowded PCB documentation file collection. Maintaining synchronicity between PCB and MCAD design databases wastes valuable designer time.
There is a hidden cost to performing a task inefficiently. If that task is repeated often enough in the engineering process, the inefficiency will have immeasurable costs for time-to-market delays on new or updated products. Every PCB design has its share of tasks related to documentation. Some documentation sets must include dozens of drawing sheets. Stringent documentation standards for military, aerospace, automotive, and other products require highly detailed, time-consuming documentation sets.
PCB documentation requirements are not limited to a single department’s needs. Documentation requirements are unique for each entity that comes in contact with a completed PCB design. Many downstream processes in product manufacturing have unique documentation requirements, including PCB rework instructions, assembly process steps, PCB panel fabrication drawing, assembly inspection, and more. As previously presented, there is more to a PCB documentation set than single-sheet assembly and fabrication drawings. Let’s consider the following scenario as a means to measure the cost of document creation inefficiently. "PCB documentation requirements are not limited to a single department’s needs."
A new product’s documentation cycle begins at the prototype stage. From this first stage, the number of documentation iterations can easily reach double digits. Consider that each iteration of a documentation set has both tangible and intangible costs—the greatest tangible cost likely being the salary of the individual creating the documents. Let’s assume a PCB designer’s annual salary is $100,000, and 20% of their time is devoted to inefficiently originating documentation. Creating documentation could cost an organization an average of $20,000 per PCB designer. Developing military-standard PCB documentation requirements can usurp more than 50% of a PCB designer’s time. For those types of electronic products, the cost of creating and maintaining documentation in an inefficient, traditional manner can easily escalate.
There are also intangible documentation costs that can be difficult to quantify. An inefficient documentation process that results in delays to new product introduction may have lost opportunity costs. Errors in a documentation set may result in multiple unplanned documentation revisions. Having a PCB designer focus on documentation rather than PCB design will delay the start of the next PCB design project. Sharing a networked software product license to create documentation and design PCBs may require users to postpone critical tasks until product licenses are made available. If other tools are in use—such as AutoCAD, Visio, or Microsoft Excel—to assist in creating documentation, the cost of training, owning, and maintaining those systems on an annual basis is also part of documentation expenditure.
When considering the cost of a PCB documentation method, it is important to measure both the creation and maintenance of a complete documentation set for the full life cycle of the product. Creating an initial documentation set will likely result in the bulk of the cost, but maintenance can be time-consuming as well. All of these documentation requirements ought to be part of any documentation efficiency calculation.
To read the rest of The Printed Circuit Designer’s Guide to… Documentation, click here. Visit the I-Connect007 eBook Library to download this book and other free, educational titles covering everything from high-speed PCB design to advanced manufacturing and assembly.
Suggested Items
Trump Copper Tariffs Spark Concern
07/10/2025 | I-Connect007 Editorial TeamPresident Donald Trump stated on July 8 that he plans to impose a 50% tariff on copper imports, sparking concern in a global industry whose output is critical to electric vehicles, military hardware, semiconductors, and a wide range of consumer goods. According to Yahoo Finance, copper futures climbed over 2% following tariff confirmation.
Happy’s Tech Talk #40: Factors in PTH Reliability—Hole Voids
07/09/2025 | Happy Holden -- Column: Happy’s Tech TalkWhen we consider via reliability, the major contributing factors are typically processing deviations. These can be subtle and not always visible. One particularly insightful column was by Mike Carano, “Causes of Plating Voids, Pre-electroless Copper,” where he outlined some of the possible causes of hole defects for both plated through-hole (PTH) and blind vias.
Trouble in Your Tank: Can You Drill the Perfect Hole?
07/07/2025 | Michael Carano -- Column: Trouble in Your TankIn the movie “Friday Night Lights,” the head football coach (played by Billy Bob Thornton) addresses his high school football team on a hot day in August in West Texas. He asks his players one question: “Can you be perfect?” That is an interesting question, in football and the printed circuit board fabrication world, where being perfect is somewhat elusive. When it comes to mechanical drilling and via formation, can you drill the perfect hole time after time?
The Evolution of Picosecond Laser Drilling
06/19/2025 | Marcy LaRont, PCB007 MagazineIs it hard to imagine a single laser pulse reduced not only from nanoseconds to picoseconds in its pulse duration, but even to femtoseconds? Well, buckle up because it seems we are there. In this interview, Dr. Stefan Rung, technical director of laser machines at Schmoll Maschinen GmbH, traces the technology trajectory of the laser drill from the CO2 laser to cutting-edge picosecond and hybrid laser drilling systems, highlighting the benefits and limitations of each method, and demonstrating how laser innovations are shaping the future of PCB fabrication.
Day 2: More Cutting-edge Insights at the EIPC Summer Conference
06/18/2025 | Pete Starkey, I-Connect007The European Institute for the PCB Community (EIPC) summer conference took place this year in Edinburgh, Scotland, June 3-4. This is the third of three articles on the conference. The other two cover Day 1’s sessions and the opening keynote speech. Below is a recap of the second day’s sessions.