-
- News
- Books
Featured Books
- pcb007 Magazine
Latest Issues
Current IssueInventing the Future with SEL
Two years after launching its state-of-the-art PCB facility, SEL shares lessons in vision, execution, and innovation, plus insights from industry icons and technology leaders shaping the future of PCB fabrication.
Sales: From Pitch to PO
From the first cold call to finally receiving that first purchase order, the July PCB007 Magazine breaks down some critical parts of the sales stack. To up your sales game, read on!
The Hole Truth: Via Integrity in an HDI World
From the drilled hole to registration across multiple sequential lamination cycles, to the quality of your copper plating, via reliability in an HDI world is becoming an ever-greater challenge. This month we look at “The Hole Truth,” from creating the “perfect” via to how you can assure via quality and reliability, the first time, every time.
- Articles
- Columns
- Links
- Media kit
||| MENU - pcb007 Magazine
Estimated reading time: 3 minutes
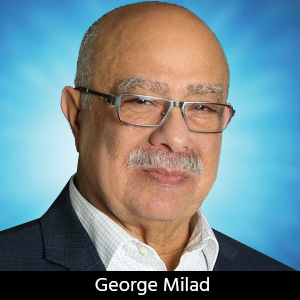
The Plating Forum: Can ‘Nickel Corrosion’ Occur in ENEPIG?
Nickel palladium gold (ENEPIG) surface finish is being referred to as the “universal finish.” The finish is an excellent soldering surface, forming a Ni/Sn intermetallic (IMC). It is a wire-bondable surface for both gold and aluminum wire. It also serves as a good contacting surface. ENEPIG was also the answer to the nickel corrosion “black pad” occasionally encountered with electroless nickel/immersion gold (ENIG) deposits.
As the finish gained more market share due to its flexibility—particularly as a gold wire bonding surface—occasional bond failure was observed in cases where the dwell time in the immersion gold was extended in an attempt to meet design requirements of > 3.0 µins (0.075 µm) of gold. The failure was manifested as wire bond lifts. Failure analysis of the failed bonds showed a separation at the Ni/Pd interface. The nickel surface was black and was clearly corroded “black pad.” Nickel corrosion in ENIG occurs in the immersion gold deposition step and is usually the result of a compromised nickel surface (uneven), in combination with an aggressive immersion gold bath (low gold concentration, low pH) and an extended dwell time in the gold bath. The extended dwell time is used in instances where the design requirements demand a thicker immersion gold. How can the nickel capped with an electroless palladium layer corrode when it is theoretically not available to the immersion gold step?
Immersion gold deposition is a displacement reaction where one atom of nickel metal is oxidized to the nickel ion giving up two electrons. The two electrons are picked up by two positively charged gold ions in solution and, in turn, are reduced to the metal and deposited on the surface of the nickel substrate.
The driving force of the oxidation-reduction displacement reactions can be derived from the electromotive series. The electromotive series is a listing of chemical species (atoms, molecules, and ions) in the order of their tendency to gain or lose electrons (be reduced or oxidized, respectively), expressed in volts and measured with reference to the hydrogen electrode—which is taken as a standard and arbitrarily assigned the voltage of 0.000 v.
The driving force for the Ni/Au exchange is 3.4 times greater than that of the Pd/Au exchange. If the immersion gold ion has access to the underlying nickel, this would be the path of least resistance for the reduction of the gold. The gold will be reduced at the expense of the nickel, allowing nickel to be oxidized or corroded and gold to be deposited on the top palladium layer. Investigation and failure mechanism analysis showed that the immersion gold, under certain conditions (compromised nickel deposit coupled with extended dwell time in an aggressive immersion gold bath), could get access to the underlying nickel.
The IPC Amended ENEPIG Specification 4556-A specifies the immersion gold thickness at 1.2–2.8 µins (0.03–0.07 µm). Although data shows that this thickness of gold is adequate for gold wire bonding, thicker gold (> 3.0 µins, 0.075 µm) is often spelled out in the board design for the purpose of opening the wire bonding window.
There are three approaches to mitigate nickel corrosion in ENEPIG deposits. The first approach is to control the electroless nickel deposition process in order to produce an even deposit with minimum crevices, to increase the phosphorous content of the deposit by one or two percentage points, and not to attempt to deposit thicker gold in an immersion gold bath.
The second approach is to deposit a thicker (6–8 µins, 0.15–0.20 µm) electroless palladium layer that could cover any imperfections in the nickel deposit and act as a barrier between the immersion gold and the underlying nickel. This is a relatively costly proposition as the price of an ounce of palladium now exceeds the price of an ounce of gold.
The third approach is to replace the immersion gold (IG) with reduction-assisted immersion gold (RAIG). RAIG is a mixed reaction bath. Both immersion and autocatalytic reactions start simultaneously. As the substrate becomes less accessible, the immersion reaction will diminish, and the autocatalytic reaction will dominate. RAIG is non-aggressive and will not produce substrate corrosion and is capable of depositing 4–6 µins, (0.10–0.15 µm) of gold in a single step.
The choice of which mitigation approach is best is left to the manufacturer and their supplier to determine availability and that the process choice fits in the production floor and is within the manufacturer’s budgetary constraints. It is worth mentioning here that the RAIG solution is gaining popularity and is becoming the choice for ENEPIG, particularly if thicker gold is specified in the design of the board.
This column originally appeared in the May issue of PCB007 Magazine.
More Columns from The Plating Forum
The Plating Forum: Reduction Assisted Immersion Gold for ENEPIG Surface FinishThe Plating Forum: Surface Finish Evolution from Conventional to Advanced
The Plating Forum: Plating in Electronic Applications
The Plating Forum: How the Pandemic Impacted PCB Manufacturing
The Plating Forum: The Significance of IPC ENIG Specification 4552 Revision B
The Plating Forum: The IPC Surface Finish Specifications
The Plating Forum: An Overview of Surface Finishes
The Plating Forum: DIG—The Next Generation