-
- News
- Books
Featured Books
- smt007 Magazine
Latest Issues
Current IssueSupply Chain Strategies
A successful brand is built on strong customer relationships—anchored by a well-orchestrated supply chain at its core. This month, we look at how managing your supply chain directly influences customer perception.
What's Your Sweet Spot?
Are you in a niche that’s growing or shrinking? Is it time to reassess and refocus? We spotlight companies thriving by redefining or reinforcing their niche. What are their insights?
Moving Forward With Confidence
In this issue, we focus on sales and quoting, workforce training, new IPC leadership in the U.S. and Canada, the effects of tariffs, CFX standards, and much more—all designed to provide perspective as you move through the cloud bank of today's shifting economic market.
- Articles
- Columns
- Links
- Media kit
||| MENU - smt007 Magazine
Estimated reading time: 4 minutes
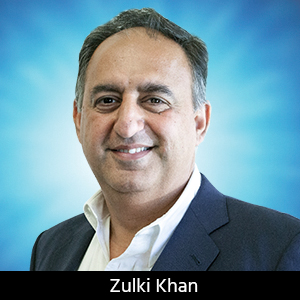
Zulki’s PCB Nuggets: Medical Miniaturization and PCB Microelectronics Assembly
Medical electronics continue to be a gamechanger, with miniaturization being foremost today in the minds of medical OEMs. In a previous column, I discussed ingestible and implantable medical devices based on remarkably small and unique PCBs, and the technology trends supporting those products continue to dramatically escalate. Today, there is a growing demand for even greater device and component miniaturization that plays a major role in the PCB microelectronics assembly of these medical devices.
Medical miniaturization is rapidly evolving because doctors, hospitals, and other medical care facilities are requiring more functionality, increased portability, and more robustness to upgrade surgical procedures and mobile monitoring equipment. Plus, the highly complex devices successfully interacting with the human body are driving the need for this greater medical miniaturization.
Biosensing and biosensors are at the forefront of this device miniaturization due to their critical nature in today’s medical technology, and they are pushing the limits of electronics manufacturing. In most cases, biosensors are implantable devices that look for diagnostic conditions, such as monitoring a patient’s health conditions in remote areas most of the time.
These biosensing devices require very thin PCBs that are capable of getting into tight spaces in the human body. We are looking at new materials for device manufacturing to be able to accommodate and be compatible with the human body and without causing adverse effects when these miniaturized devices are inserted.
Traditionally, the thinner flex circuit boards are 15 mils or so. Now, with the advent of new technology, we are looking at 5–10 mils of flex board thickness, which are more nimble and flexible to go into smaller places within the human body without much difficulty. Examples of these miniaturized devices include implantable defibrillators, cardiac pacemakers, programmable infusion pumps, continuous glucose monitoring (CGM) devices, and wellness and emergency response safety monitoring systems.
As far as those very thin PCBs, a microelectronics assembly line must be able to deal with this emerging device miniaturization. A PCB microelectronics assembly line must have key operations, such as:
- Highly precise and accurate flux and solder paste dispensing systems for the traditional SMT manufacturing as well as for extremely precise epoxy dispensing for die attach and encapsulations when using microelectronic manufacturing
- Extremely accurate component placement systems having within tolerances of ±1-mil accuracy for SMT manufacturing, and tolerances of ±10-micron accuracy when dealing with microelectronics assembly
- Excellent inspection systems using in-process verification methodologies so that a product has self-verification and correction mechanism built into it for full manufacturing cycle for optimal product creation
- Final testing tools so that the testing of the final product can be automated, thereby reducing the time to ship the product to the end-users and customers
Aside from having the right PCB microelectronics assembly capabilities, the medical equipment OEM and EMS provider partner must take into account that datasheets for newer miniature devices and components may not yet be available on a large commercial scale. Therefore, it is to their advantage to collaborate early on with device manufacturers to find out about device characteristics, such as electrical, mechanical, thermal, and electromagnetics.
Those include electrical signals, thermal capabilities, and mechanical sturdiness, among other key device characteristics; that’s vitally important since we’re dealing with new materials. Along this line, other top characteristics that must be evaluated include component size, grain structure and size, and the custom processing that may be required for specialized custom components in terms of miniaturization.
Component selection also takes on another level of importance. For instance, take a microcontroller or a similar device that has multiple embedded functionalities into a single chip. Here, power management and thermal capabilities must be investigated so that the component and overall circuitry perform at optimal levels, keeping in mind the speeds at with these signals are operating under normal circumstances.
Simultaneously, considerations must be given to the evolution of these devices and the fact they are increasingly integrated into a human form factor. This means they must continue to be less bulky, lighter in terms of weight, considerably mobile, sturdy, robust, and more dexterous to sustain a long lifetime in the human body.
Further, relatively new terminology is entering into the medical electronics lexicon and is highly pertinent to PCB microelectronics assembly, such as, “The proximity of a device to the human skin or human element.” That is one more thing required for device miniaturization. For example, with artificial pancreases, ocular implants, or prostatic human arms and legs, close scrutiny must be applied to implantable chips and how they react to human fluids and body chemicals for those chips to perform in an optimal way without degrading the integrity of human fluids.
Given today’s trends toward increasing medical device miniaturization, it is highly beneficial for medical equipment OEMs to partner with PCB design and assembly vendors that not only design but also develop the necessary processes at the early stages of new products. Those include component matching and selection for a particular product application, associated power consumption, and other important factors associated with medical miniaturization. Based on these disciplined steps, testing and mass production are performed with minimal efforts.
Zulki Khan is the president and founder of NexLogic Technologies Inc.
More Columns from Zulki's PCB Nuggets
Zulki's PCB Nuggets: Cleanliness is Next to ReliabilityZulki’s PCB Nuggets: Thermal Compression Bonding for Extra Fine Pitch Flip Chips
Zulki’s PCB Nuggets: WBAN Steps Into PCB Microelectronics Assembly
Zulki’s PCB Nuggets: Photonics Comes to PCB Microelectronics Assembly
Zulki’s PCB Nuggets: Sub-Micron Die Bonding—Don’t Be Misled by Five Micron Placement Standard
Zulki’s PCB Nuggets: Meet the New Player in PCB Microelectronics Assembly—Interposers
Zulki’s PCB Nuggets: How Effective Is Your PCB Microelectronics Assembly?
Zulki’s PCB Nuggets: Five Key Benefits for Onshoring PCB Microelectronics Assembly