-
- News
- Books
Featured Books
- design007 Magazine
Latest Issues
Current IssueProper Floor Planning
Floor planning decisions can make or break performance, manufacturability, and timelines. This month’s contributors weigh in with their best practices for proper floor planning and specific strategies to get it right.
Showing Some Constraint
A strong design constraint strategy carefully balances a wide range of electrical and manufacturing trade-offs. This month, we explore the key requirements, common challenges, and best practices behind building an effective constraint strategy.
All About That Route
Most designers favor manual routing, but today's interactive autorouters may be changing designers' minds by allowing users more direct control. In this issue, our expert contributors discuss a variety of manual and autorouting strategies.
- Articles
- Columns
- Links
- Media kit
||| MENU - design007 Magazine
Estimated reading time: 6 minutes
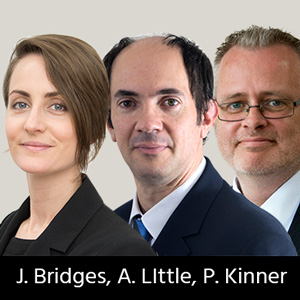
Sensible Design: Encapsulation Resins—What Could Go Wrong?
In last month’s column, we looked at the pitfalls of potential contaminants and best mixing practices for two-part encapsulation resins. This month, I’ll address some of the pain points with mixing resin packs and air bubbles, including what can go wrong and why. I will also examine some of the key differences between conformal coatings, encapsulation resins, and potting compounds to help designers make decisions that are more informed, ultimately increasing the reliability and lifetime of your electronic circuitry.
Extending lifetime and improving the performance of devices is essential to a brand’s reputation; no one appreciates a product recall, or worse, a product failure. Encapsulation resins are an excellent way of protecting electronic circuitry; however, there are some excellent conformal coating alternatives on the market too. I will elaborate further to help dispel any confusion.
For instance, we have created the 2K coatings range, which behaves like a resin with the application ease of a coating. This has been a great success in applications, such as automotive, where protection in harsh environments is critical. I will explore coatings vs. resins, as well as resins vs. potting compounds, using my usual five-point Q&A format. Let’s take a closer look at five critical factors affecting encapsulation resins.
1. What are the consequences of having air bubbles trapped in encapsulation resins, and does this impair performance?
Air bubbles can have a number of effects on the performance of the cured resin. Depending on the number and distribution of the bubbles, the thickness of the polymer layer applied
will be decreased. The level of protection will also be reduced, particularly against chemical attack.
If there are air bubbles next to components, wiring, or tracks, then particularly when high voltages are applied, corona can build up inside these voids and ultimately destroy the components or wiring. Voids also act as a weak point for thermal and physical shock, which can lead to the resin cracking in service.
Bubbles in optically clear resins not only look unattractive but will also distort the light passing through the resin either by the changes in the refractive index or by diffusion of the light. Bubbles on the surface of the resin may break over time, with dirt and detritus collecting in the resulting crater.
2. What are some key differences between resins and coatings?
The most noticeable differences are the methods of application, such as aerosol, conformal coating spray equipment, manual spray gun, and brushing for coatings. This is compared to mixing and dispensing equipment and resin packs for resins, thickness of application (500 microns for resins), and approval ratings (coatings are generally approved to UL746, whereas for resins, it heavily depends on the application).
Because of the coating thickness, coatings occupy less space and have a low increase in overall weight compared to resins. There are both coatings and resins based on epoxy, polyurethane, and silicone chemistries, but there are also acrylate, acrylic, and parylene coatings that do not have a direct resin equivalent. Ninety-nine percent of resins are 100% solid systems, meaning they have low, or no, VOCs released during curing, while many coatings are solvented.
However, it is important to mention that there are two-component (2K) and UV-curable acrylate systems with 100% solids available. These 2K coatings, in particular, can be applied up to 500 microns thick without cracking during thermal shock testing and enable a greater degree of component lead coverage to be achieved, resulting in improved performance during thermal shock, powered salt-spray testing, MFG testing, and condensation testing (i.e., traditionally gruelling test regimes that are commonly used during automotive qualification campaigns). The 2K series is also VOC-free, solvent-free, and fast curing.
3. Why would I choose a resin instead of a coating?
The choice between a resin or a coating is usually down to application specifics. If the unit involved is to be subject to long-term immersion in various chemicals, continuous thermal, and/or physical shock cycling, then a resin is generally preferred. Additionally, if there are a large number of big components on a PCB, it is generally better to use a resin to encapsulate these than to coat them. Further consideration should be given if the unit is to be used in a situation where it is not easily accessible or if a long continuous service life is required, in which case a resin would be recommended to provide the extra protection and durability needed.
4. Are encapsulation resins and potting compounds basically identical, or are there differences?
There are no real differences between the two in terms of the resins used, but there is a difference in what the resin is required to do. An encapsulation resin will totally cover the PCB and the components and can act as the protective support structure, while a potting compound is used to fill a housing or enclosure containing the PCB and components.
An encapsulation resin will adhere to the PCB and the components, and its outer faces will act as the primary barrier to protect the unit. However, a potting compound has to adhere not just to the PCB and components, but also the housing. In this case, the differences in CTE (coefficient of thermal expansion) between all the materials used can become a critical factor, as the resin will be subjected to different rates of expansion and contraction due to the materials concerned, as well as its own CTE. This can put a resin under extreme stress and, over time, lead to failure.
5. What is the most effective method for mixing a resin pack, what can potentially go wrong (and why)?
First, remove the resin pack from the outer packaging. In the case of polyurethane and silicone resins, do not remove from the foil outer pack until ready to use. Lay the pack out onto a flat surface and remove the centre clip. Use the clip to push the resin from one half of the pack to the other, then pick the pack up in both hands and mix in a circular motion for a couple of minutes.
Place the pack back on the flat surface and use the clip to push the resin from the corners into the centre. Pick the pack up in both hands and continue mixing for a further minute. Repeat pushing the resin from the corners into the centre of the pack, and then continue to mix for another minute to ensure that the material is fully mixed and is a uniform colour.
Use the clip to push the mixed resin to the side of the pack with the angled seam. Roll the pack film up so that the pack fits into the hand. Cut the corner of the pack off and then tilt the pack to dispense the resin, applying slight pressure as required to maintain the flow. If the material from the corners of the pack is not pushed into the centre of the pack, then unmixed material can be dispensed.
If the resin is not mixed sufficiently, it may not cure, or have a patchy cure. In the case of filled resin systems, some sedimentation might have taken place over time, so it may take a little more mixing to ensure that the fillers are correctly distributed throughout the resin. With the optically clear resins, when first mixed, the resin will appear hazy. This is perfectly normal, and the haziness will disappear as the material cures.
Conclusion
I hope the points covered this month have been helpful. Look for my next column, where I’ll cover more issues on encapsulation resins to get the best protection for your circuitry requirements with the least amount of aggravation. In the meantime, please contact me if you have any questions.
This column originally appeared in the February 2020 issue of Design007 Magazine.
More Columns from Sensible Design
Sensible Design: Automotive Conformal Coating ApplicationsSensible Design: Green Coats Are In
Sensible Design: Encapsulation Resins—PU vs. Epoxy
Sensible Design: Avoiding Conformal Coating Pitfalls
Sensible Design: Comparing Traditional and Bio-based Resins
Sensible Design: All Resins Are Not Created Equal
Sensible Design: Can Solvent-free UV-cure Coatings Increase Stability and Throughput?
Sensible Design: Optimize Your Thermal Management