-
- News
- Books
Featured Books
- smt007 Magazine
Latest Issues
Current IssueSupply Chain Strategies
A successful brand is built on strong customer relationships—anchored by a well-orchestrated supply chain at its core. This month, we look at how managing your supply chain directly influences customer perception.
What's Your Sweet Spot?
Are you in a niche that’s growing or shrinking? Is it time to reassess and refocus? We spotlight companies thriving by redefining or reinforcing their niche. What are their insights?
Moving Forward With Confidence
In this issue, we focus on sales and quoting, workforce training, new IPC leadership in the U.S. and Canada, the effects of tariffs, CFX standards, and much more—all designed to provide perspective as you move through the cloud bank of today's shifting economic market.
- Articles
- Columns
- Links
- Media kit
||| MENU - smt007 Magazine
Estimated reading time: 5 minutes
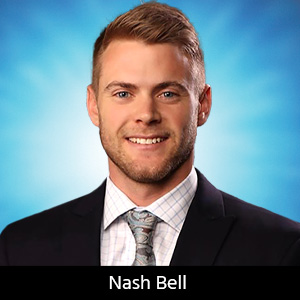
Knocking Down the Bone Pile: PCB Rework of 0201 Packages
As electronic passive components continue to shrink in size, methods for their rework need to be developed by electronic manufacturers to maintain and support PCB assembly processes. The 0201 package—only 20 by 10 thousands of an inch in size—is one of the components requiring a higher degree of rework skill compared to other larger packages. IPC-7711 and IPC-7721 on the “Rework, Modification, and Repair of Electronic Assemblies”[1] for these resistor and capacitor sizes outlines a variety of methods in sections 3.3.X. Here, I will compare and outline a few of these rework methods.
While the 0201 package size has been in the mainstream for several years, assembly soldering defects are common. Tombstone defects, common for this package type, are commonly caused by the pads heating up at different rates. A thermal mass imbalance may cause one of the pads to heat at a different rate compared to the other. For example, if one of the 0201 pads is connected to a thermal ground plane and the other pad is not, the unconnected pad will heat at a faster rate—all others being equal. This thermal imbalance will cause the tombstoning defect as the molten solder pushes up one side of the component.
It is well understood that lighter and smaller components are more susceptible to this tombstoning phenomenon. A similar result is realized if the pads are not the same size, as the larger pad will heat at a slower rate. The pad sizes influence the defect rate; smaller pad sizes result in higher defect rates[2]. The component placement offsets in the X and Y direction are one of the largest contributors to the post-reflow defect rates of these packages. This means that the assembler needs to control these parameters by placement consistency through proper placement programming, nozzle maintenance, and placement pressure. In addition, the very small pad geometries of the 0201 packages make solder paste printing consistency a challenge, which can also cause defects.
A Conductive Soldering Rework Technique
The most common technique used to remove and replace 0201 body style components is through the use of a conductive hand soldering system. This hand soldering rework technique calls for the removal of a passive component by employing a micro body tweezer or a micro hoof soldering tip. For part removal using a micro hoof tip, make sure to first tin the flat surface of the tip as this will aid in heat transfer. For placement, apply the proper liquid flux to the pads and hold the 0201 down with the tip of a tweezer and touch the hoof tip for 2–3 seconds to one side of the pad to allow the solder to reflow. Finish the attachment by doing the same operation on the other side.
An even faster hand soldering method uses a micro tweezer hand piece. These tweezers can reflow both ends of the 0201 simultaneously for component removal or replacement. The tips themselves are fragile structures and are easily damaged, which means care needs to be taken by the soldering technician. Because of the small geometries involved, the skill and patience of the soldering technician need to be at an advanced level. The site preparation process post component removal, regardless of the tip used, requires great care by the rework technician as the very small pad surface area means that the propensity to damage or lift pads is high. While hand soldering is the fastest method for the removal and replacement of the 0201, it requires a high degree of operator skill and dexterity.
Hot Air Rework
Another reflow method employed by soldering technicians for the rework of these small passive devices is by using a hot air source. Both controlled (closed-loop rework systems) and uncontrolled hot air sources (hot air guns or handpieces) can be used to reflow 0201s. These hot air sources must be designed with low airflow capability so as not to disturb the solder joint or blow the component off the pad. A controlled heat source has limited throughput compared to the hand soldering rework method as there are several process steps, which takes time. A split vision rework system, which assists the operator in aligning the part to the pads, reduces the degree of skill required to rework these small packages.
The downside of using a hot air reflow source is that components neighboring the component of interest can also be reflowed during the soldering or desoldering process. To prevent the hot air source from disturbing these neighboring components, they need to be thermally masked from the heat source. This further extends the rework process time. When using a hot air rework system, the removal of the component is accomplished by using a hot air nozzle specifically designed to push out low airflow. For replacement of the 0201 component, a high-resolution camera, combined with precision X-Y adjustments of the rework system, means device placement can be more precise and repeatable vis-à-vis the hand soldering approach.
Using an IR Reflow Source
While the hand soldering of 0201 packages requires highly-skilled soldering technicians and the hot air rework sources can easily disturb the solder or placement location of the lightweight 0201s, the use of an IR reflow source is a good alternative approach to reworking these packages. Infrared rework systems do not use any airflow as part of the reflow cycle, thereby preventing the problems associated with the hot air rework sources. The IR heat source can quickly heat these small component body style types before their removal.
Magnification, as part of the rework system—along with a micro vacuum nozzle—can then remove the component once a liquidus state has been reached. Through the use of an IR BGA rework system and the high skill and dexterity level required for rework of these 0201 packages, without the downside risk of the positive airflow from the hot air source, makes the IR reflow source ideal for these components.
References
1. IPC, “IPC-7351 Generic Requirements for Surface-Mount Design and Land Pattern Standard,” Bannockburn, Illionis, 2015.
2. Paul Neathway, et al. “A Study of 0201’s and Tombstoning in Lead-Free Systems,” Proceedings of SMTAI, 2014.
This column originally appeared in the September 2020 issue of SMT007 Magazine.
More Columns from Knocking Down the Bone Pile
Knocking Down the Bone Pile: Addressing End-of-life Component Solderability Issues, Part 4Knocking Down the Bone Pile: Tin Whisker Mitigation in Aerospace Applications, Part 3
Knocking Down the Bone Pile: Gold Mitigation for Class 2 Electronics
Knocking Down the Bone Pile: Basics of Component Lead Tinning
Knocking Down the Bone Pile: Package on Package Rework—Skill Required
Knocking Down the Bone Pile: 2023’s Top Challenges in BGA Rework
Knocking Down the Bone Pile: Eliminating Solder Balls in Hand Soldering
Knocking Down the Bone Pile: Opening a Trace on the Surface of a PCB