-
- News
- Books
Featured Books
- smt007 Magazine
Latest Issues
Current IssueSupply Chain Strategies
A successful brand is built on strong customer relationships—anchored by a well-orchestrated supply chain at its core. This month, we look at how managing your supply chain directly influences customer perception.
What's Your Sweet Spot?
Are you in a niche that’s growing or shrinking? Is it time to reassess and refocus? We spotlight companies thriving by redefining or reinforcing their niche. What are their insights?
Moving Forward With Confidence
In this issue, we focus on sales and quoting, workforce training, new IPC leadership in the U.S. and Canada, the effects of tariffs, CFX standards, and much more—all designed to provide perspective as you move through the cloud bank of today's shifting economic market.
- Articles
- Columns
- Links
- Media kit
||| MENU - smt007 Magazine
Estimated reading time: 4 minutes
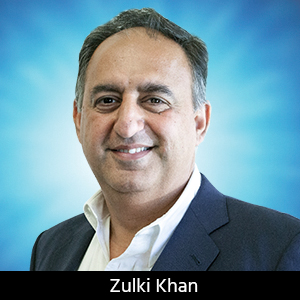
Zulki’s PCB Nuggets: FCBGA Packaging Enters PCB Microelectronics Assembly
As I’ve said in earlier columns, the demand for smaller circuitry and packaging, as well as ever-shrinking PCB real estate, have continually pushed PCB assembly and manufacturing protocols. Newer, smaller, portable, and ingestible medical devices are opening new frontiers and are leading OEMs from other industries down that same road.
Part of these technological advances deal with a new twist or turn associated with PCB microelectronics assembly. It involves a combination of flip-chip and BGA (FCBGA) packaging, as shown in Figure 1. This is nothing new since this type of packaging has been around for the past 15 years. But now, it’s entering into a more prominent phase since FCBGA is of utmost importance in the microelectronics assembly and manufacturing of newer, smaller medical devices, as well as small mil-aero, commercial, and industrial devices.
Figure 1: A BGA and a flip-chip interposer. (Source: Thorsten Meyer, Wikipedia, with minor modifications in red)
But before going there, let’s take a step back to take another look at conventional BGA packaging to fully understand the importance of FCBGAs.
With conventional BGAs, I’m talking about traces and spaces in mils (one-tenth of an inch) rather than in microns. For example, 25 microns equals one mil. This means that if you are running a trace from two pads of a BGA on an FR-4 or any other organic substrate like Rogers, you need to have a BGA pad pitch of at least 30 mils on a 10-mil ball size to run a trace of three or more mils in between adjacent pads. That’s not possible from a real estate and size perspective when it comes to microelectronics simply due to the fact everything is so tiny.
This is where FCBGA comes in. This flip-chip assembly shrinks the conventional BGA down to one-third to one-fourth the original size and, at the same time, all the necessary connections can fit into that one-third or one-fourth of the physical size of the BGA. By doing so, more valuable space is created on an already small flex or rigid-flex circuit board. In other words, the same circuitry can be designed on a lot smaller real estate, when you go from BGA interposer to a flip-chip.
That’s only part of the story that an FCBGA brings to the PCB microelectronics assembly area. The other is more extensive and lands squarely on both the EMS supplier or contract manufacturer and the OEM. Both parties must have an understanding of new advances in the redistribution of layers (RDL). In the case of a flip-chip, in particular, RDL conveys signals from a die out to pins that solder it to the circuit board and through the BGA, effectively reducing the amount of real estate involved.
At the top of the RDL list, at the outset of a PCB microelectronics assembly project, EMS providers collaborate with their OEMs on the correct flip-chip material. Will organic or inorganic material be used for making the substrate to install BGA and flip-chip? And will chip connection C4 or C2 material be used for the flip-chip bumps? Regardless of which one is chosen, careful considerations must be applied because each has different characteristics and has a definite application.
In many instances, C4 bumps are used in area array flip-chip packages. However, it’s not suitable for ultrafine-fine flip-chip devices. The key reason is C4 solder bumps melt and collapse on the wide opening copper pads. On the other hand, C2 bumps are connected to copper substrate pads, which are a surface treated with organic solder preservative (OSP), with reflow and no-clean processes, ideally speaking.
Also, discussion and recommendation take into account wafer size, whether it’s six-, eight-, or 12-inch. Bumps have to be put on each chip, but typically on the wafer-level—not on the individual die-level—and the industry term for this process is under bump metallization (UBM). Six-inch wafers are less costly to process compared to eight- or 12-inch wafers.
Beyond these key points to be considered, there are a number of others:
- Making the bumps either with C2, which is copper pillar, or C4, which are solder bumps
- Solder paste to be used, such as SAC 305 or tin-silver, or another type, like tin-lead
- Recommended BGA pad size on the die and the RDL substrate
- Will the OEM provide bumps at the wafer-level or on the die-level?
- What type of flatness is acceptable to the OEM customer when it comes to the RDL substrate as it pertains to attaching the die on a substrate like PCB?
- What are the advantages and disadvantages of using an organic RDL substrate like FR-4 or Rogers versus inorganic material like gallium arsenide or alumina?
As indicated here, the introduction of FCBGA presents new questions and challenges for PCB microelectronics assembly. They are best resolved when OEMs get an early start with their EMS providers to discuss how to effectively approach the microelectronics assembly of new and smaller devices, whether they be medical, military, industrial, or commercial. The important thing to keep in mind is that you are creating a flip-chip from a BGA and still making the same connections. The result is utilizing only 30–40% of the circuit board space to perform all the connections.
Zulki Khan is the president and founder of NexLogic Technologies Inc.
More Columns from Zulki's PCB Nuggets
Zulki's PCB Nuggets: Cleanliness is Next to ReliabilityZulki’s PCB Nuggets: Thermal Compression Bonding for Extra Fine Pitch Flip Chips
Zulki’s PCB Nuggets: WBAN Steps Into PCB Microelectronics Assembly
Zulki’s PCB Nuggets: Photonics Comes to PCB Microelectronics Assembly
Zulki’s PCB Nuggets: Sub-Micron Die Bonding—Don’t Be Misled by Five Micron Placement Standard
Zulki’s PCB Nuggets: Meet the New Player in PCB Microelectronics Assembly—Interposers
Zulki’s PCB Nuggets: How Effective Is Your PCB Microelectronics Assembly?
Zulki’s PCB Nuggets: Five Key Benefits for Onshoring PCB Microelectronics Assembly