-
- News
- Books
Featured Books
- smt007 Magazine
Latest Issues
Current IssueSpotlight on India
We invite you on a virtual tour of India’s thriving ecosystem, guided by the Global Electronics Association’s India office staff, who share their insights into the region’s growth and opportunities.
Supply Chain Strategies
A successful brand is built on strong customer relationships—anchored by a well-orchestrated supply chain at its core. This month, we look at how managing your supply chain directly influences customer perception.
What's Your Sweet Spot?
Are you in a niche that’s growing or shrinking? Is it time to reassess and refocus? We spotlight companies thriving by redefining or reinforcing their niche. What are their insights?
- Articles
- Columns
- Links
- Media kit
||| MENU - smt007 Magazine
Estimated reading time: 5 minutes
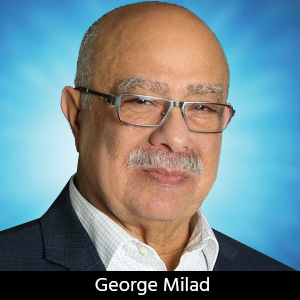
The Plating Forum: The Critical Role of Pretreatment for Plating
Electrodeposition can be traced back to the 1800s. Plating decorative gold on a silver surface using a voltaic cell was exciting at that time. Along with electrodeposition, surface prep or pretreatment was an integral part of the process.
Pretreatment is usually customized to the incoming substrate and the plated metal. It is designed to clean organic and inorganic contaminants from the surface. In addition, pretreatment may alter the surface morphology of the substrate for adhesion enhancement. It is a critical step and must be completed before plating to achieve the desired adhesion and to enhance the quality of the deposited metal.
Pretreatment utilizes cleaners and etching steps. In some applications, pretreatment is used to modify the substrate to allow plating to initiate. Chemistries used in pretreatment are not compatible with the plating process and must be thoroughly rinsed before plating. Rinsing for electronic manufacturing is usually done in a two- or three-step cascading flowing rinse.
The following is a description of the desired pretreatment for the following applications:
- General metal finishing
- Plating for electronics manufacturing:
- Electroless copper plating
- Acid copper plating
- Surface finish
1. General Metal Finishing
Metal surfaces must be pretreated before plating. The objective is to remove contaminants from the surface. Contaminants may be organic (oils, grease, fingerprints) or inorganic (scale, stains, and oxides).
The process is referred to as “pickling” and usually involves the use of strong acids like sulfuric or hydrochloric. The pickling liquor may contain other acids as well as specific additives like wetting agents and corrosion inhibitors. The pickling chemistry must be compatible with the specific basis metal and effective at removing the associated impurities and or contaminants.
The choice of pickling liquor chemistry (type, concentration, and bath life) and the conditions under which it is used—like temperature, dwell time, and part agitation—must be well-defined and adhered to for efficient surface preparation. The pickling solution must be thoroughly rinsed before the introduction into the plating electrolyte.
2. Plating for Electronics Manufacturing
Electroless Copper
The electroless copper process is used in electronic manufacturing to metalize the dielectric in the drilled holes. The deposition is autocatalytic or electroless and does not require rectification.
Pretreatment is very critical in this process as it serves multiple functions. It starts with a cleaner/conditioner that cleans the surface and modifies the fiberglass in the FR-4 dielectric by altering its negative charge to neutrality so that it will adsorb the catalyst that initiates the copper deposition.
The cleaner is followed by a micro-etch that refreshes the copper on the surface, as well as in the inner layer interconnects in the hole. It ensures good adhesion on the copper surface and the interconnect integrity with no separation between the plated copper and the inner layer. This step is followed by the catalyst and its rinse.
If the pretreatment is compromised, voiding in the deposit may occur as well as a separation in the interconnect at the inner layers. The electroless copper process is preceded by “desmear.” Desmear is considered a process in its own right and not a pretreatment.
Acid Copper Electroplate
The copper electroplate process is the backbone of printed circuit manufacturing. It forms the circuitry that carries the current throughout the board. Parts coming to the electroplating line have already been through the electroless copper process. Pretreatment here involves a cleaning step, micro-etch, and acid predip.
The “cleaner” serves a series of functions: the detergent component removes soils and organic residues (fingerprints), the acidic component removes oxidation, and the surfactant present wets the surface. A properly wetted surface will help dislodge any entrapped air in the narrower vias. Entrapped air leads to voiding and discontinuity. Vibrating the parts in the cleaner bath is recommended for high aspect ratio holes and blind vias. Vendor recommendations of makeup, bath life, operating temperature, and dwell time, should be followed. Good rinsing should follow the “cleaner.”
The micro-etch step is mild and removes 5–10 micro-inches of copper, exposing a fresh surface for plating. Excessive etching is not recommended, as it may dissolve the electroless metallization resulting in voiding.
The last step in pretreatment is an acid predip. This serves two functions. First, it ensures no oxidation on the copper surface; second, it acidifies the surface to match the acidity of the copper electrolyte.
Surface Finish
For the purpose of this column, I chose to break down surface finish to:
1. Single-layer finishes: Hot air solder leveling (HASL), organic solderability preservative (OSP), immersion silver, and immersion tin
2. Multilayer finishes: ENIG, ENEPIG, and EPIG/EPAG
Single-Layer Finishes
The pretreatment for this class of finishes is based on creating a clean surface that is contaminant/oxide free. In addition, for immersion silver and immersion tin, the surface morphology of the copper surface is also addressed. For HASL to produce a contiguous intermetallic (IMC) with no dewetting, the copper surface must be clean and pristine. For pretreatment, the parts go through a cleaner and a micro-etch in a horizontal conveyorized manner; this is followed by a flux dip before introduction into the molten solder. Inadequate pretreatment results in dewetting of the solder on the copper surface. For OSP, the same principle of cleaning the copper surface applies. OSP is usually run in continuous horizontal equipment. OSP is specific to the copper surface and forms a complex with the clean copper. Immersion silver, as the name of the process implies, is an immersion or displacement reaction. It is driven by electromotive force. Pretreatment involves a cleaner and a micro-etch. The micro-etch is hydrogen-peroxide-based to produce a smoother copper morphology. A smoother topography eliminates the probability of bubble voids at the IMC after soldering. Immersion tin pretreatment is based on cleaning and micro-etching. It is important that the immersion reaction initiates uniformly for better continuity of the tin deposit.
Multilayer Finishes
The pretreatment for ENIG, ENEPIG, and EPIG/EPAG has been addressed in detail in a previous column titled “ENIG and the Plating Process.” What applied to ENIG is the same for ENEPIG and EPIG/EPAG.
Conclusion
Pretreatment plays a key role in the success of the process that it is designed for. Special attention to the front end of the line (pretreatment) is needed. Adhere to the supplier’s instructions per the datasheet. A compromised or incomplete pretreatment could have devastating results that may lead to scrapping products.
George Milad is the national accounts manager for technology at Uyemura.
More Columns from The Plating Forum
The Plating Forum: Reduction Assisted Immersion Gold for ENEPIG Surface FinishThe Plating Forum: Surface Finish Evolution from Conventional to Advanced
The Plating Forum: Plating in Electronic Applications
The Plating Forum: How the Pandemic Impacted PCB Manufacturing
The Plating Forum: The Significance of IPC ENIG Specification 4552 Revision B
The Plating Forum: The IPC Surface Finish Specifications
The Plating Forum: An Overview of Surface Finishes
The Plating Forum: DIG—The Next Generation