-
- News
- Books
Featured Books
- design007 Magazine
Latest Issues
Current IssueProper Floor Planning
Floor planning decisions can make or break performance, manufacturability, and timelines. This month’s contributors weigh in with their best practices for proper floor planning and specific strategies to get it right.
Showing Some Constraint
A strong design constraint strategy carefully balances a wide range of electrical and manufacturing trade-offs. This month, we explore the key requirements, common challenges, and best practices behind building an effective constraint strategy.
All About That Route
Most designers favor manual routing, but today's interactive autorouters may be changing designers' minds by allowing users more direct control. In this issue, our expert contributors discuss a variety of manual and autorouting strategies.
- Articles
- Columns
- Links
- Media kit
||| MENU - design007 Magazine
Estimated reading time: 3 minutes
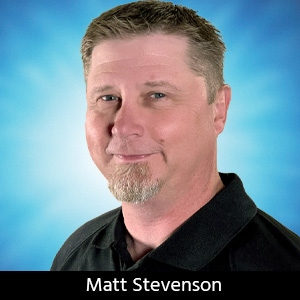
Connect the Dots: Design Tips for Layout
As a PCB manufacturer, we receive hundreds of PCB layouts represented in Gerber format every week. As you might expect, they’re not all created equal. Some of the layouts check every box and roll straight into manufacturing, while others need work before they can be sent to the production floor.
We affectionately refer to these layouts on occasion as Etch-A- Sketch designs, meaning that they did not adhere to best practices nor pay close attention to detail during the layout phase. And yes, sometimes these designs really do look like they were created on a toy from the ‘70s and not in a CAD tool. We recognize there are many good reasons for not-quite-ready-for-primetime designs to be submitted, such as:
- A designer lacking layout experience
- Looming deadlines and rushed design processes
- A lack of attention to the details
- A need for something to test in a hurry
Often, these issues create delays and issues with yield or reliability. They can be avoided before they cause problems with your budget and production schedule. Here are some best practices for doing so.
Use the Tools in Your CAD Program
You can represent a feature in your design by almost any means you’d like, but adhering to a few best practices leveraging the many useful functions in your CAD design tools can help eliminate confusion for your PCB manufacturer. For example, you can represent slots as overlapping drilled holes in your design. It isa common practice, but it creates two potential issues for the manufacturer:
- If left as is, it can create broken drill bits impacting yields and quality of the product.
- The other possibility is that the tooler corrects the issue during manufacturing, which is a very inefficient process.
Most software for PCB layout offers the capability to make a slot and have it contained on the drill layer of the Gerber files.
Another common design issue comes in the form of circles drawn on a layer to represent non-plated mounting holes. Your manufacturer may easily interpret this representation to mean you want copper circles on your PCB. Creating the mounting holes in your design tool and assigning them the plating type that you need is a much better approach. This will ensure you receive the non-plated mounting holes you want, not copper circles, and it doesn’t take any more time.
Pay Attention to Your Gerber Files
In many cases, the Gerber files you submit for manufacturing will be the gold standard by which the manufacturer creates your PCB. Most of the higher end PCB layout tools do a pretty good job of creating Gerber files that do justice to the layout, but there are certainly exceptions.
Utilizing a Gerber viewer to display your files before submission can help you to identify potential issues ahead of manufacturing (Figure 1). This practice can even limit your need to troubleshoot a completed design and use the blue wires to make it work. Common issues discoverable using the Gerber viewer include:
- Overlapping thermal connections on adjacent pins (isolating intended connections)
- Drilled holes in an unintended copper feature (like through a trace)
- Oversized or missing solder mask clearances (potential to create solder shorts or unsolderable situations)
Just Because You Can Doesn’t Mean You Should
Sometimes, you need to zoom in to see it. Many PCB layout tools are creatively accommodating and will let you do nearly anything digitally, but the consequences can be staggering during the transition to manufacturing. For example, we see many submitted designs that are virtually unbuildable due to the blind and/or buried vias in the design.
Blind and buried vias are one sure way to drive up the cost, extend lead time, and increase yield loss. We recommend that you do not build blind or buried vias into your design unless absolutely necessary. It goes without saying for this audience that comments like, “I was able to draw it, so you should be able to build it,” are only made in jest. PCB manufacturing must still adhere to the laws of physics, and that makes some things impossible to build at any cost.
Conclusion
At the end of the day, it comes down to taking your time, checking your work, and applying thoughtful design concepts to your PCB layout project. PCB layout is not rocket science (well, sometimes it actually is). Applying a few best practices, and using common sense steps in the design phase, can be a serious time saver.It is like the old adage about health: An ounce of prevention is worth a pound of cure.
There are many resources available to help you be successful, from YouTube videos to colleagues and your PCB manufacturer, to name a few. Good luck out there!
This column originally appeared in the January 2020 issue of Design007 Magazine.
More Columns from Connect the Dots
Connect the Dots: Sequential Lamination in HDI PCB ManufacturingConnect the Dots: The Future of PCB Design and Manufacturing
Connect the Dots: Proactive Controlled Impedance
Connect the Dots: Involving Manufacturers Earlier Prevents Downstream Issues
Connect the Dots: Stop Killing Your Yield—The Hidden Cost of Design Oversights
Connect the Dots: Designing for Reality—Routing, Final Fab, and QC
Connect the Dots: Designing for Reality—Surface Finish
Connect the Dots: Designing for Reality—Solder Mask and Legend