-
- News
- Books
Featured Books
- smt007 Magazine
Latest Issues
Current IssueSupply Chain Strategies
A successful brand is built on strong customer relationships—anchored by a well-orchestrated supply chain at its core. This month, we look at how managing your supply chain directly influences customer perception.
What's Your Sweet Spot?
Are you in a niche that’s growing or shrinking? Is it time to reassess and refocus? We spotlight companies thriving by redefining or reinforcing their niche. What are their insights?
Moving Forward With Confidence
In this issue, we focus on sales and quoting, workforce training, new IPC leadership in the U.S. and Canada, the effects of tariffs, CFX standards, and much more—all designed to provide perspective as you move through the cloud bank of today's shifting economic market.
- Articles
- Columns
- Links
- Media kit
||| MENU - smt007 Magazine
Estimated reading time: 6 minutes
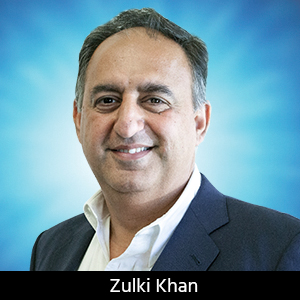
Zulki’s PCB Nuggets: Wire Bonding and CoB for PCB Microelectronics Assembly
Real estate continues to be a precious commodity for substrates, package sizes, dies, and PCBs. One thing stays constant, any way you look at it, and that constant is we continue to shrink the real estate as much as possible.
Not long ago, package on package (PoP) was a top technology on the SMT manufacturing floor. With PoP, you stack one component on top of another and then on top of another. That was one way of dealing with the assembly challenges of a shrinking PCB real estate. However, with PoP, OEMs and manufacturers are struggling with stability and reliability.
But now, the industry is taking another stab at further reducing PCB real estate. The technologies that advanced PCB microelectronics assembly offers these days provide medical electronics OEMs and others an array of different options to optimize their product designs, whether they are portable, wearable, insertable, or ingestible devices.
It’s highly important to know which technology best fits your medical electronics application. Take wire bonding and chip on board (CoB) as examples. Each has its advantages and disadvantages. Let’s take a look at both to point out what might be best for your medical electronics device while undergoing PCB microelectronics assembly.
Wire Bonding
Wire bonding is old technology. It has been around since the invention of the transistor; therefore, it’s an established process. Some of the considerations involving wire bonding are wire thickness, length, and type of wire to be used. There’s a variety of types, such as aluminum, gold, silver, copper, platinum, and nickel.
Now, as far as the wire loop radius of bonded wires is concerned, this feature requires even closer scrutiny because the wire loop affects reliability. The smaller the loop is, the more reliable it is going to be, generally speaking.
But when it comes to higher-speed, higher-frequency RF, and microwave applications, you need to assure 100% that wire length is as short and as direct as possible, and the loop is as small as possible. Keeping the loop very short avoids, among other things, the inductance that’s created in these RF applications.
If the loop for RF or microwave devices using high frequencies is higher, line losses would be higher, and the transmission of the signal would not be as robust. Also, wire bonding made of non-traditional materials like platinum, nickel, and copper is possible. However, some bonding parameters need to be adjusted accordingly.
But these are typically reserved for specialized applications, especially when it comes to copper because it has a tendency oxidize at room temperature. To avoid oxidation, an inert atmosphere, such as nitrogen, is needed for assembly. Typically, gold wire is used because it has exceptionally good thermal conductors; it’s extremely reliable, and it possesses multiple characteristics like decent heat dissipation capability.
On the downside, it is a bit expensive with gold prices fluctuating constantly, making it difficult to predict true cost, especially when it comes to production runs. Moreover, gold wire bonding has to be assembled at a higher temperature versus aluminum wedge bonding, which can be assembled at room temperature.
Then, there’s the protection aspect. Keep in mind that we’re talking about very fine and thin one- to two-mil wire. One-mil gold wire is considerably thinner than a human hair. There are multiple options available for protecting wire bonding. If you’re using five- to 10-mil wire, you may or may not need to protect it because that is sufficiently thick for mechanical sturdiness.
But one- to three-mil wire mostly needs protection. Three methods for protecting thin wire bonds are glob top, dam and fill, and in some optical applications, partial glob topping is used because vision-related lens or sensor area needs to be kept open for vision clarity.
Wire bond stacking is yet another area that needs special consideration for medical electronics applications that feature considerable input and output signaling. The stack could be double, triple, or quadruple. The biggest challenge associated with three to four stack wire bonding is keeping the wire loop intact without breaking or intermingling with other loops. The reason for that is because the loop for the first set of wire bonds would be the smallest compared to the second, third, and fourth.
For example, let’s say the fourth stack has the longest loops, and you have to protect those. You need to make sure they are not intersecting or touching each other. If they are, shorts are created, which ruins the assembly that has taken so much time, energy, and effort. There are also insulated wires, especially for multi-stack wire bonding. Regardless if wires are touching, no problem exists since insulated covering is there for protection. Even if they are touching, they are not shorting. That way, wire bond integrity and complete circuitry are intact.
Chip on Board
Again, the assembly challenge we’re facing is the simple fact too much real estate is consumed by packaged dies. These packages could be glass, ceramic, metal, aluminum, and in some cases, gold. But now, with CoB, we are removing the package, and it can be directly attached to the board.
Flexibility is a major advantage CoB has over wire bonding. That allows you to make changes in the interconnection. If you’re connecting from Point A to Point B, and if it’s not working, you can change it from Point A to Point C and D during the design stages. This gives you the flexibility needed in making the changes within the interconnect. This is not possible with wire bonding.
Aside from eliminating a package and its flexibility, CoB is excellent for higher thermal application product projects where the heat needs to be out and dissipated. Moreover, fanning out of CoB is easier and less complicated compared to wire bonding. Also, the form factor is especially important since, in many cases, a package is larger than the die, and there is the flexibility of epoxies to be used for heat dissipation as well.
But if you’re designing the CoB fanout, you can optimize your traces coming out. When you’re designing the CoB, you can make those interconnects a lot more optimal compared to wire bonds. That’s one of the key beauties of CoB and a top reason CoB is used over wire bonding.
One more thing, when it comes to high-speed, high-frequency applications, wire bonding is not as effective as a solution because of the capacitance and inductance it can create. In this case, CoB is used. It works much more optimally in the higher-frequency, high-speed ranges because it’s a characteristic of not having as much capacitance or inductance along the path of current during the forward and return path back.
As we see here, medical electronics OEMs and other OEMs have to take a close look at PCB microelectronics assembly for their advanced small and portable devices. It’s always best to partner with your EMS provider to discuss the variety of technologies that are best suited to their applications. Two of those technologies are wire bonding and CoB, and they need close scrutiny to make sure one or the other is best suited for their applications.
Zulki Khan is the president and founder of NexLogic Technologies Inc.
More Columns from Zulki's PCB Nuggets
Zulki's PCB Nuggets: Cleanliness is Next to ReliabilityZulki’s PCB Nuggets: Thermal Compression Bonding for Extra Fine Pitch Flip Chips
Zulki’s PCB Nuggets: WBAN Steps Into PCB Microelectronics Assembly
Zulki’s PCB Nuggets: Photonics Comes to PCB Microelectronics Assembly
Zulki’s PCB Nuggets: Sub-Micron Die Bonding—Don’t Be Misled by Five Micron Placement Standard
Zulki’s PCB Nuggets: Meet the New Player in PCB Microelectronics Assembly—Interposers
Zulki’s PCB Nuggets: How Effective Is Your PCB Microelectronics Assembly?
Zulki’s PCB Nuggets: Five Key Benefits for Onshoring PCB Microelectronics Assembly