-
- News
- Books
Featured Books
- design007 Magazine
Latest Issues
Current IssueProper Floor Planning
Floor planning decisions can make or break performance, manufacturability, and timelines. This month’s contributors weigh in with their best practices for proper floor planning and specific strategies to get it right.
Showing Some Constraint
A strong design constraint strategy carefully balances a wide range of electrical and manufacturing trade-offs. This month, we explore the key requirements, common challenges, and best practices behind building an effective constraint strategy.
All About That Route
Most designers favor manual routing, but today's interactive autorouters may be changing designers' minds by allowing users more direct control. In this issue, our expert contributors discuss a variety of manual and autorouting strategies.
- Articles
- Columns
- Links
- Media kit
||| MENU - design007 Magazine
Estimated reading time: 4 minutes
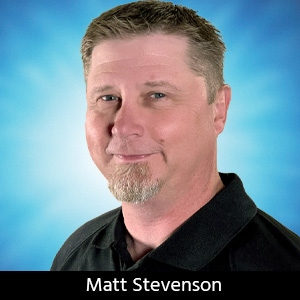
Connect the Dots: Design Tips to Avoid Part Fit Problems
"Will my parts fit on the board?" That seems like it should be a rhetorical question that needs no answer but reality tells us, as you transition from the design stage to manufacturing, issues with parts fit are one of the most frequent causes of delays and cost overruns.
We see it every day. Designs are submitted that can’t or shouldn’t be manufactured because the parts will not fit properly. This creates issues with performance and durability—effectively reducing the overall quality of the board.
Following are six methods that will help you avoid common, parts-related manufacturability pitfalls.
1. Avoid pinhole pitfalls.
It’s important to check component physical dimensions. Height is an often-overlooked portion and can create issues at or after assembly. Take dimensional tolerances into consideration and account for variation that can impact fit. Through-hole pins can be the wrong size or have the wrong spacing, and components can actually be much larger than their footprint or land pattern might indicate. Surface mount parts take the pin diameter and tolerance out of the equation, making them easier to verify. It is far easier to take the time up front and be right than to have to re-spin a design or try to find an alternate part that fits your board.
2. What to do when the land pattern and pin size differ.
One of the most frustrating mistakes with through-hole parts is when the land pattern matches, but the pin size is too large to fit reliably.
If hole sizes are too tight, pins may not fit into the holes, pins bend during insertion, or they go into the holes but may not solder well. Proper through-hole soldering requires solder to flow up through the gap between the pin and the hole barrel. If there is not enough space to allow enough solder mass to flow up through the hole, a cold solder joint can result and premature failure of your circuit is likely to occur.
To avoid this issue, make sure that when designing, you know the pin size and tolerance range for your components. Component holes should be sized correctly to allow between 12 and 16 mils diameter larger than the component pin at maximum material condition (MMC) when possible.
MMC is the condition in which the hole is drilled at the low end of the tolerance range, and the pin measures at the high end of the tolerance range. Pin locations should be placed at nominal location or the basic dimension shown on the datasheet.
3. Data sheets can disagree with CAD software.
Third-party CAD libraries can contain millions of different parts, so it should not come as a surprise that a few bad apples lurk among them. When the data sheet and the library part don't match up, your project is dead before you make the first connection. Always check any library part for accuracy before you use it the first time.
The data sheet for a part usually tells the real story, and it's usually just a few lines that provide you with the information you need to make the crucial decisions about sizing. It's important to read and comprehend the data sheets so problems in CAD don't lead to the wrong sizing and spacing on the PCB.
4. Pay attention to pinouts when using alternate vendor parts.
Even if you've paid attention to pin size and through-hole size, and you’ve made sure your solder joints are good, a part can still not work as expected. Similar parts with the same footprint might look like they should act identically, but they won't always have the same pinout. Sure, each transistor has a gate, drain and source, but different manufacturers can differ in what goes where.
A Motorola part can differ from a Texas Instruments (TI) part, and if you're just buying generics, all bets are off. The same basic component will come in multiple packages. Sometimes the variations are tossed into the back of a data sheet as an afterthought, but these can be critical. Similarly named packages can even come in different widths.
5. Be aware of mechanical fit.
It's not just the footprint and through-holes that you need to pay attention to. The physical size of your component body can keep parts from fitting into designated spaces. Again, MMC is the rule, and with maximum component body size, paying close attention to the tolerance range is critical.
As parts get larger, or you start sourcing your parts from multiple vendors, your footprint size may need to expand considerably to accommodate all the dimension and tolerance variables. When combining multiple part body dimensions, always take the largest dimension, or you could end up trying to violate the Pauli exclusion principle, which states that two identical fermions (particles with half-integer spin) cannot occupy the same quantum state simultaneously. In short, you are going to smash something.
6. Data sheets are helpful, but not a replacement for experience.
When it comes down to it, the data sheet is considered king, but that doesn’t mean you shouldn’t question it when necessary. Many problems with fit can be unintuitive or difficult to diagnose, so understanding size requirements will prevent a lot of headaches. Every dimension needs to be looked at, from pin and through-hole size, to capacitor height.
Frequently these issues will crop up when replacement components are used. Watch those tolerance ranges carefully. When you are evaluating replacements, make sure your replacement parts fall between maximum and minimum measurements stated in your original part data sheet. You could get away with parts that are smaller in some regards, but this should be carefully evaluated. And don’t forget to pay attention to pinouts and alternate packages.
This column originally appeared in the January 2021 issue of Design007 Magazine.
More Columns from Connect the Dots
Connect the Dots: How to Avoid Five Common Causes of Board FailureConnect the Dots: Sequential Lamination in HDI PCB Manufacturing
Connect the Dots: The Future of PCB Design and Manufacturing
Connect the Dots: Proactive Controlled Impedance
Connect the Dots: Involving Manufacturers Earlier Prevents Downstream Issues
Connect the Dots: Stop Killing Your Yield—The Hidden Cost of Design Oversights
Connect the Dots: Designing for Reality—Routing, Final Fab, and QC
Connect the Dots: Designing for Reality—Surface Finish