-
- News
- Books
Featured Books
- design007 Magazine
Latest Issues
Current IssueProper Floor Planning
Floor planning decisions can make or break performance, manufacturability, and timelines. This month’s contributors weigh in with their best practices for proper floor planning and specific strategies to get it right.
Showing Some Constraint
A strong design constraint strategy carefully balances a wide range of electrical and manufacturing trade-offs. This month, we explore the key requirements, common challenges, and best practices behind building an effective constraint strategy.
All About That Route
Most designers favor manual routing, but today's interactive autorouters may be changing designers' minds by allowing users more direct control. In this issue, our expert contributors discuss a variety of manual and autorouting strategies.
- Articles
- Columns
- Links
- Media kit
||| MENU - design007 Magazine
Estimated reading time: 5 minutes
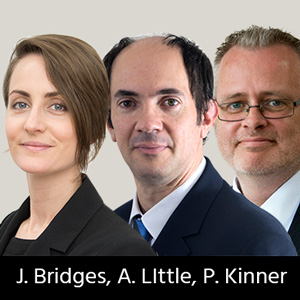
Sensible Design: How to Avoid Problematic ‘Blushing’ and ‘Bubbling’ in Conformal Coatings
The performance requirements of conformal coatings continue to become ever more challenging as electronic assemblies are becoming smaller and smaller and subjected to increasingly hostile operating environments. The perfect conformal coating would retain high elasticity at both high and low temperature extremes and would maintain its properties at high temperatures with no out-gassing. It would also provide an excellent barrier to moisture, both in terms of humid environments and where there is a risk of liquid water splash. It would be highly resistant to solvents and corrosive gases but be easy to remove when repairs or modifications need to be carried out. Ultimately, the perfect coating would be intelligent, self-applying and, of course, free of charge—but then that’s a whole different ball game.
In this month’s column, I will revisit a couple of general enquiries we have received about “bubbling” as well as the less common appearance of cloudy white patches following the application of a conformal coating.
Blushing
Naturally, we are all aware of the many potentially problematic encounters that can occur when using conformal coatings. The usual suspects tend to be contamination leading to corrosion, cracking, blistering, fisheyes, de-wetting, and so forth. However, one of the rarer problems that can occur is “blushing.” If you have the misfortune of discovering that your coating isn’t as clear or transparent as it should be, and instead, looks dull and cloudy white, then the chances are you have stumbled upon this particular coating issue.
The main reason why coatings can become milky is largely due to moisture absorption. High levels of atmospheric moisture can create havoc with certain solvent-based materials. As the solvents evaporate from the coating, a cooling effect is experienced. If this cooling effect drops the coating below the dew point, then water will condense onto and into the coating as it dries. This can range from a reversible cosmetic effect (heat it up and the discoloration should disappear) to problems with the coating developing adhesion, or its full protective properties. Blushing can be identified when the conformal coating becomes cloudy, hazy, or milky in appearance. Humidity is a big issue, especially if it exceeds 65%. Equally, low temperatures can also wreak havoc at lower than 15oC. Issues that arise from assemblies/components stored in environments with excessive moisture can be addressed by baking the boards.
Some of the problems that can arise from blushing include:
- Surface tackiness
- Poor adhesion
- Incomplete cure
- Poor adhesion with second coating
- Dull, matte finish
Blushing can occur when using aerosol coatings. To avoid blushing when coating via aerosol, there are some important points to remember. Firstly, there is no need to shake the aerosol can before use, as this can add bubbles to the mixture which can then be transferred to the board. The board should be at a 45-degree angle to the can, (e.g., if the board is flat, the can should be at 45 degrees) and around 20-30 cm away from the can. Spray the board in a continuous steady Z motion, coating evenly. The board should then be rotated 90 degrees, the coating applied again using the same motion, and the board rotated again, repeating the process until you have rotated the board a full 360 degrees. This allows an even coating of the correct coating thickness and ensures the coating can cover raised components and leads from different angles, thus ensuring the best coverage possible. A turntable can be used to aid this process.
Other factors to help prevent blushing include maintaining a stable humidity and temperature in the production environment. At Electrolube, we recommend humidity between 50-65% and an ambient temperature environment between 15oC and 25oCto help combat blushing. Ensuring adequate time between coating and cure is also advisable to allow solvents to evaporate fully. The use of slower thinners can also assist with the potential reduction of evaporation/condensation to reduce blushing incidences. Baking assemblies following the cleaning process can also eliminate moisture, as well as ensuring all storage atmospheres and containers are sufficient against moisture.
The quality and performance of a conformal coating material could also be compromised according to the method of application. This is commonly encountered when a product is transferred from one circuit manufacturer to another; for example, a product may be dip-coated in one country but selectively coated in another with the specification requiring that the same material be used at both sites. The problem that arises here, however, is that using a material formulated for dip coating in selective coating equipment can result in poor yield due to it being excessively fast drying, leading to bubble entrapment. You want fundamentally different behaviour from a material in a dip-coating application than in a selective spray application. One of my customers spent six months trying to solve a bubble issue internally, without realising that the root cause of this problem lay in the material formulation. Working with the customer, it became clear that by changing the solvent blend, the bubble entrapment issue could easily be resolved. Moreover, this solution simplified the process and reduced the cycle time significantly. And since the non-volatile formulation remained the same, there was no need to re-qualify.
Bubbling
When solvents or air become trapped and can't escape the coating material, the chances of bubble formation are more than likely. Bubbles in a conformal coating can lead to product reliability issues further down the line and even possible failures. The IPC specification allows a dry film thickness of 30–130 microns, the greater thickness being achieved by the application of multiple coating layers. Trying to achieve a 130-micron dry film thickness from a single selective-coating process with a solvent-based acrylic material is a recipe for disaster and is likely to result in excessive bubble formation, film shrinkage, coating de-lamination and additional stress on components. The result is poorer protection, rather than an improved overall level of circuit protection. Aiming for a uniform 30-50 microns and focusing on achieving perfect coverage at each application is a much better approach to improving the protection of electronic circuits. Achieving the correct coating thickness is important. Bear in mind that if the coating is too thick it can lead to entrapment of solvents in areas where the coating does not fully cure. Similarly, it can cause the coating to crack as it cures, as the result of changes in temperature, or due to mechanical shock and vibration.
Conformal coatings protect electronic assemblies from harsh environments by sealing off the electronics from contaminants and environmental factors that can lead to reliability issues and failures. For coatings to be effective, they need to uniformly cover the entire component without moisture, fluid, or outside impurities present. While it might be tempting to use shortcuts either to reduce costs or to speed up production, there will inevitably be a price to pay. Know the limitations and/or special properties of the materials you use to coat electronic assemblies and abide by the correct procedures. Still have doubts? There are experts on hand at Electrolube who have seen it all before and who can steer you in the right direction.
This column originally appeared in the February 2021 issue of Design007 Magazine.
More Columns from Sensible Design
Sensible Design: Automotive Conformal Coating ApplicationsSensible Design: Green Coats Are In
Sensible Design: Encapsulation Resins—PU vs. Epoxy
Sensible Design: Avoiding Conformal Coating Pitfalls
Sensible Design: Comparing Traditional and Bio-based Resins
Sensible Design: All Resins Are Not Created Equal
Sensible Design: Can Solvent-free UV-cure Coatings Increase Stability and Throughput?
Sensible Design: Optimize Your Thermal Management