-
- News
- Books
Featured Books
- design007 Magazine
Latest Issues
Current IssueAll About That Route
Most designers favor manual routing, but today's interactive autorouters may be changing designers' minds by allowing users more direct control. In this issue, our expert contributors discuss a variety of manual and autorouting strategies.
Creating the Ideal Data Package
Why is it so difficult to create the ideal data package? Many of these simple errors can be alleviated by paying attention to detail—and knowing what issues to look out for. So, this month, our experts weigh in on the best practices for creating the ideal design data package for your design.
Designing Through the Noise
Our experts discuss the constantly evolving world of RF design, including the many tradeoffs, material considerations, and design tips and techniques that designers and design engineers need to know to succeed in this high-frequency realm.
- Articles
- Columns
- Links
- Media kit
||| MENU - design007 Magazine
Predicting a ‘Roaring Twenties’ Innovation Boom
February 24, 2021 | Hailey Lynne McKeefy, Freelance Journalist and Supply Chain SpecialistEstimated reading time: 8 minutes
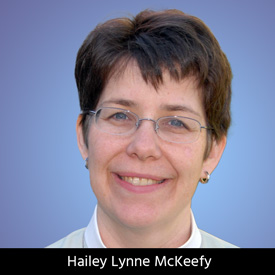
The 2020s have not started as anyone would have wished. The COVID-19 pandemic has exposed weaknesses in supply chains and in global manufacturing, yet this could still be the most innovative decade ever.
COVID-19 exposed the need for evolution and perhaps even a revolution in the manufacturing and supply chain industries. Many founders and CEOs of technology companies, from large and small EMS players, to those that supply them with software and equipment are predicting a period of rapid innovation and digital transformation. A group of the most interesting and influential founders and c-suite executives in the manufacturing world offered their own insights.
Accelerating Toward Factories of the Future
It seems likely that the 2020s will see more adoption of Industry 4.0 and smart factory solutions as part of the general digital transformation of manufacturing. Carl Hung, CEO of The Season Group and SG Wireless, expects “a continuing adoption of Industry 4.0 technologies such as IoT, first for data collection and analysis, and then subsequently 5G deployments for no-latency control of manufacturing equipment. We’re designing products for customers to collect data and remotely manage their business.”
Anna-Katrina Shedletsky, founder and CEO of Instrumental, says, “For many engineering teams, the pandemic has clarified exactly what is most urgent about digital transformation. Having siloed product and process data, or no data, or data that’s only accessible from the factory floor, is a huge problem. Trying to engineer remotely through cell phone photos, Facetime and Zoom is untenably slow. There’s a clear data availability and access problem that digitization can solve, and solving it actually unlocks further innovation.”
“COVID-19 has shone a light on the importance and value of digitizing and automating factory operations,” said Amar Hanspal, CEO and co-founder of Bright Machines. “I am most excited about the potential of this digital transformation to speed up innovation by enabling localized production and removing barriers to entry to get great products made. I believe the days of leaning on globalization—finding cheap pools of labor—has run its course. Software-defined manufacturing democratizes product innovation so that anyone, regardless of location or available resources, can turn a great idea into a product, on-demand.”
Dave Evans, founder and CEO of Fictiv, said, “I fully expect 2021 to be a year where digital transformation really takes hold. We now know that transformation is not just a ‘nice to have,’ but essential for factories, companies, and manufacturing ecosystems. It is likely in the future that a digitally enabled manufacturing ecosystem will be table stakes for brands wishing to purchase parts or products.” Juan Arango, managing director of Koh Young America, expects 2021 to pick up where we left off, “as the industry continues to innovate on the factory floor and in its business processes. This digital transformation and shift to greater automation can serve to make the U.S. even more competitive in the future. I see a bright future of innovative people developing innovative products, supported by an equally innovative digitally enabled local manufacturing industry.”
“Even before the pandemic started, Cogiscan had defined a long-term strategic business plan that was directly related to digital transformation,” François Monette, founder and CBDO of Cogiscan, added. “We went from a company who always had employees traveling the world to sell, install and support our technology to one that performs the same functions almost 100% remotely. Similarly, most of our customers already had some form of digital transformation effort underway but these long-term plans moved to a much higher priority. The majority of CEOs have identified digital transformation as a top priority for the coming year and they have assigned more budget and resources to develop and implement their roadmap. Companies, such as Cogiscan, that provide smart factory technology will face a great challenge and opportunity to scale up their operations to keep up with the market demand.”
Pandemic Exposed Weaknesses in the Supply Chain
John Mitchell, president and CEO of IPC, sees that “COVID-19 exposed many supply chain weaknesses, illustrating just how far some companies were from being able to understand their product development ecosystem—especially remotely. The coronavirus acted as a catalyst for much of the electronics industry to accelerate their adoption of several of the transformations that were ‘nice to haves’ or good to talk about in the 2010s. Now that a company’s production was depending upon them, those Industry 4.0 platitudes needed to perform! Instead of a global ‘supply chain,’ companies are now having to understand and develop their regional ‘supply network’ or ‘supply cloud.’ Single source lowest cost supply options have been replaced with three-tier minimum suites of suppliers that offer local, regional, and global options at varying production quantities and price points.”
“I don't think supply chains have ever gotten quite this much attention!” said Yoav Zingher, founder and CEO, Launchpad.build. “In 2020 everyone found out what manufacturing insiders already know—our ability to flexibly make things, innovate, and adapt has been severely reduced in a competitive drive to lower prices. In a static world, lower prices are the easiest way to compete. But in a world of rapid change, either because of negative shocks such as a pandemic, or positive shocks such as technology innovation, the best way to compete is to be one step ahead of everyone else, by being flexible and adaptive.”
Ross Berntson, president and COO of Indium Corporation, explained, “Indium Corporation has keenly felt the challenges of COVID-19 in the toll on our people and our customers. However, through the stress, we have created systems and products that are capitalizing on the information and communication revolutions accelerated by the pandemic. As a material supplier and innovator, we are deep in the supply chain, meaning we are subject to some of the biggest bullwhip effects. In other words, demand fluctuates greatly. We are relying on communication systems and data analytics that link us to end user demand while also increasing the flexibility and velocity of our production processes to be able to surge when demand spikes.”
EMS Executive Excited About a Manufacturing Renaissance
Bruno Racault, CEO of ALL Circuits, says, “2020 was a really tough year in France, and indeed throughout Europe. Leaving aside the ongoing human tragedy, we had to be innovative and creative to continue our work as we managed supply disruptions, working conditions and, of course, a roller coaster of demand. The year has ended well for ALL Circuits with three major new contracts being awarded that will allow us to continue to grow and transform our factories. Many of the dynamics of 2020 have led brands to think long and hard about where they make their products and we’re happy that France, and indeed Europe, will likely end up winning more business as a result. I believe this trend combined with a focus on digital transformation, Industry 4.0, and automation, will lead to a renaissance of European manufacturing, particularly in France and Germany, two countries committed to becoming the smartest manufacturing region in the world.”
And Mark Wood, CEO of Microart Services, believes that “COVID also exposed the adaptability, resilience, and sheer desire to get things done in the manufacturing industry. I could not be prouder of how our team stepped up and did what had to be done to get essential products out and to provide continuity to our customers. It also exposed some issues with those over extended supply chains with too great a dependence on Asia, particularly China. We’ve seen many customers and prospects respond to this, exploring the possibility and value of sourcing closer to home, and closer to their customer. I think we’ll see more.”
According to Brad Heath, founder and CEO of Virtex, “There is a definite need to develop innovation around how we think about supply chains. There is so much concentration around Asia that domestic manufacturers are putting their businesses at significant supply chain risk due to dependence on Asia. We must develop novel ways to identify, qualify, and support domestic sources for commodities we currently source in Asia for the majority of our purchases. We need to develop innovative tools to fill gaps in the supply chain in a proactive way.
As small- to mid-size manufacturers, we also need to develop advanced software tools for quantifying and avoiding supply chain risk from force majeure-type events. This can include weather, pandemics, civil unrest, or any other unpredictable factors which are currently not part of our current toolset. This can be done through AI, machine learning or other tools that are not typically part of the SMB toolkit.
“COVID has been an extraordinary accelerant for pre-existing trends: the death of the high street, the uptake of cycling, the move to flexible remote working, the rise of retail investment,” said Theo Saville, founder and CEO of CloudNC. “We’ve seen 10 years of progress jammed into 10 months. However, manufacturing has not been a big beneficiary, quite the contrary, the sector has taken a hammering. Supply chains have been torn apart, and the global vacuum of demand continues to push poorer performing manufacturers out of business. Conversely, the strongest and most innovative companies are surviving and even thriving, and coming out on the other side leaner, meaner, and with a reduced field of competition.” In the years post-vaccine, Theo predicts that accelerated vertical integration, rapid tech adoption and consolidation will drive expansion of average revenues and margins in manufacturing’s higher mix industries.”
Marco Annunziata, consultant and senior partner at SCOOP, concludes, “I think the pandemic will trigger a major acceleration in innovation, guided by a greater awareness of where innovation can bring the greatest value. Software systems that can help reconfigure in real time operations and supply chain management; labor-augmenting technologies that give manufacturing workers better information and real-time training; manufacturing platforms that enhance resilience and flexibility at the ecosystem level. The pandemic has exposed the weaknesses of our manufacturing sectors; the recession will leave companies and governments weakened and more indebted—the imperative to accelerate innovation will be inescapable.”
Let the Twenties Roar
Having shared conversations with all the contributors and many more, I suspect 2021 could go one of two ways. It could be more of the same. More of the same pandemic panic, more of the same work from home lifestyle, more of the same Zoom meetings and virtual conferences and shows. Or it could be very, very different, with the industry accelerating toward a much newer, more relevant version of digitally transformed manufacturing and we push into a decade of rapid innovation of product, services, ecosystems and much more.
I say let the twenties roar!
Suggested Items
Intervala Hosts Employee Car and Motorcycle Show, Benefit Nonprofits
08/27/2024 | IntervalaIntervala hosted an employee car and motorcycle show, aptly named the Vala-Cruise and it was a roaring success! Employees had the chance to show off their prized wheels, and it was incredible to see the variety and passion on display.
KIC Honored with IPC Recognition for 25 Years of Membership and Contributions to Electronics Manufacturing Industry
06/24/2024 | KICKIC, a renowned pioneer in thermal process and temperature measurement solutions for electronics manufacturing, is proud to announce that it has been recognized by IPC for 25 years of membership and significant contributions to electronics manufacturing.
Boeing Starliner Spacecraft Completes Successful Crewed Docking with International Space Station
06/07/2024 | BoeingNASA astronauts Barry "Butch" Wilmore and Sunita "Suni" Williams successfully docked Boeing's Starliner spacecraft to the International Space Station (ISS), about 26 hours after launching from Cape Canaveral Space Force Station.
KIC’s Miles Moreau to Present Profiling Basics and Best Practices at SMTA Wisconsin Chapter PCBA Profile Workshop
01/25/2024 | KICKIC, a renowned pioneer in thermal process and temperature measurement solutions for electronics manufacturing, announces that Miles Moreau, General Manager, will be a featured speaker at the SMTA Wisconsin Chapter In-Person PCBA Profile Workshop.
The Drive Toward UHDI and Substrates
09/20/2023 | I-Connect007 Editorial TeamPanasonic’s Darren Hitchcock spoke with the I-Connect007 Editorial Team on the complexities of moving toward ultra HDI manufacturing. As we learn in this conversation, the number of shifting constraints relative to traditional PCB fabrication is quite large and can sometimes conflict with each other.