-
- News
- Books
Featured Books
- design007 Magazine
Latest Issues
Current IssueProper Floor Planning
Floor planning decisions can make or break performance, manufacturability, and timelines. This month’s contributors weigh in with their best practices for proper floor planning and specific strategies to get it right.
Showing Some Constraint
A strong design constraint strategy carefully balances a wide range of electrical and manufacturing trade-offs. This month, we explore the key requirements, common challenges, and best practices behind building an effective constraint strategy.
All About That Route
Most designers favor manual routing, but today's interactive autorouters may be changing designers' minds by allowing users more direct control. In this issue, our expert contributors discuss a variety of manual and autorouting strategies.
- Articles
- Columns
- Links
- Media kit
||| MENU - design007 Magazine
Estimated reading time: 6 minutes
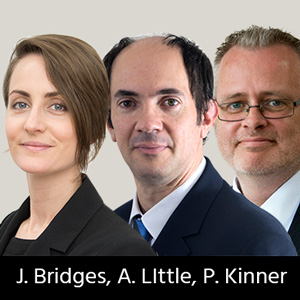
Sensible Design: Growth and Trends in the Thermal Management Market
The ongoing trend for product miniaturisation combined with more modern, higher-powered devices has ensured that reliable thermal management is an essential part of both modern and future electronics design. The LED lighting market is just one example of where thermal management is critical to the durability of the unit. Thermal management products are also offering solutions for greater efficiency in green energy development; photovoltaic inverters, which are known to be particularly sensitive to temperature; connections between the heat-pipe and water storage tank for solar-heating applications; hydrogen fuel cells; and wind power generators.
Is the thermal management market growing now? Yes, it certainly is, due to the ever-increasing number of electronic devices and applications entering the market. Demand has risen for higher performance and greater reliability in products with the added requirement of making electronics more discreet to fit into more challenging locations and environments. Let’s explore some of the reasons why the market is growing.
Is product performance or product reliability deemed most important by manufacturers when producing their products for market?
Both! It depends on the product in most cases. For example, everyone will want their product to perform the best, but each product will have a different expected lifetime. For something with a small turnaround time, i.e., a device that is expected to be updated every one to two years, the performance of that product is most likely going to be the most important factor. It may be competing against many other similar devices on the market and therefore must be both reliable and high performing but with an emphasis towards the latter. For a safety-critical device, you absolutely need reliability. It may not be “all singing and dancing” but as long as it does the job it is intended to do without failure, it will be acceptable. There is usually a trade-off with the properties of any design but remember, by considering thermal management from the start, it should be possible to achieve highly in both areas.
Is there a drive for higher and higher levels of thermal conductivity?
Yes, you could say that there is a drive for increased levels of thermal conductivity. However, if you were to investigate each response in detail, thermal conductivity may not actually be the desirable factor engineers are looking for. In all applications, everyone is striving for improved performance and greater efficiency. Simply increasing the level of thermal conductivity alone may not offer you these improvements.
When specifying the thermal conductivity required, it should be based on the end application conditions and requirements. It should also consider the design of the unit/substrate and the application method of the thermal management compound. If the product is not applied correctly—for instance, if air voids are present—then the product cannot offer the full level of thermal dissipation it is capable of.
In general, when you increase the thermal conductivity you must adjust the amount or type of fillers used in the thermal management material and that could impact the viscosity of the product, which in turn affects the overall performance of the product in the end use application. This change may also impact other properties, such as electrical conductivity/insulation, the material’s behaviour in changing temperature conditions, etc. Therefore, while most will say that with electronics becoming more powerful and being used in more challenging environments (and so higher thermal conductivities are needed), each application should be reviewed holistically to make sure that you achieve the best performance from the thermal management material, not just rely on the thermal conductivity value alone.
Heat generation rises in line with miniaturisation and the desire for higher performing components—what are the solutions?
Look at the design of the unit/PCB; are there any ways in which heat could be distributed more effectively? For example, if all heat-generating components are now in one area and close together, could they be relocated? This sounds simple to do but in practice it is not always possible. Other ways to effectively dissipate the heat away from certain areas is to ensure you have the best thermal interface material for your application. That means checking the thermal resistance at the interface, or more simply, checking the temperature of components or areas of the board. When you have this starting information, you can look at ways to improve heat dissipation by adjusting the thermal interface material used, for example. This could be moving to a product with higher thermal conductivity, however, make sure it can still be applied correctly to enable it to perform as expected.
As well as looking at the interface materials used, you could also look into the gaps around the board. Are there any areas where hot air could gather whilst the unit is in operation? Does the outer case offer any heat dissipation, i.e., is it made of metal? If so, could you utilise a gap-filling product to help remove these localised pockets of air? There are many ways to reduce heat dissipation but again it is important to look at the unit/PCB as a whole, as an action taken in one area of the board may lead to issues elsewhere.
What new trends are expected in global thermal management?
Due to developments in the electronics industry, the introduction of smaller and smarter products is increasing. These advancements in the industry have led to an increased need for innovative thermal management technologies to improve system performance and reliability by eliminating the heat generated by devices. Trends driving growth in this market include the increasing popularity of smartphones and tablets, which have seen considerable growth in the past decade. Due to mounting sensitivity toward weight and price, the need for advanced thermal management solutions is increasing.
Artificial intelligence (AI) is growing rapidly for the next generation of smartphone, smart home device, and smart speaker categories. This is expected to drive the thermal management technologies market further.
Increasing awareness of environmental issues combined with potential performance advantages is propelling the adoption of electric vehicles and a more widely available charging infrastructure, both of which rely heavily on thermal management predominantly for increasing the reliability and performance of battery systems. Also, the increasing adoption of renewable energy resources is a major factor driving the thermal management market.
Due to escalating industrialization across the world, demand has risen for continuous power supplies, which has positively impacted the growth of the thermal management market to ensure maximum reliability. For instance, capacitors are used to temporarily store electricity where required, or in off-grid applications batteries may be required to store power for more widespread use. In such cases, these electronic devices will require protection from the elements but will also be required to operate at higher temperatures and offer some form of thermal dissipation, due to the heat emitted during operation. Depending on the design, thermal management products will be used to help dissipate heat away from devices to maintain efficient, continual power.
I hope the points covered this month have been helpful and please look for my next column, where I’ll be covering more issues on thermal management to get the best heat protection for your circuitry requirements. In the meantime, please contact me if you have any questions. We also have numerous technical resources available for your interest, such as how-to videos on our youtube channel, and articles and blog stories on newly updated, application-focused website at www.electrolube.com.
This column originally appeared in the April 2021 issue of Design007 Magazine.
More Columns from Sensible Design
Sensible Design: Automotive Conformal Coating ApplicationsSensible Design: Green Coats Are In
Sensible Design: Encapsulation Resins—PU vs. Epoxy
Sensible Design: Avoiding Conformal Coating Pitfalls
Sensible Design: Comparing Traditional and Bio-based Resins
Sensible Design: All Resins Are Not Created Equal
Sensible Design: Can Solvent-free UV-cure Coatings Increase Stability and Throughput?
Sensible Design: Optimize Your Thermal Management