-
- News
- Books
Featured Books
- design007 Magazine
Latest Issues
Current IssueProper Floor Planning
Floor planning decisions can make or break performance, manufacturability, and timelines. This month’s contributors weigh in with their best practices for proper floor planning and specific strategies to get it right.
Showing Some Constraint
A strong design constraint strategy carefully balances a wide range of electrical and manufacturing trade-offs. This month, we explore the key requirements, common challenges, and best practices behind building an effective constraint strategy.
All About That Route
Most designers favor manual routing, but today's interactive autorouters may be changing designers' minds by allowing users more direct control. In this issue, our expert contributors discuss a variety of manual and autorouting strategies.
- Articles
- Columns
- Links
- Media kit
||| MENU - design007 Magazine
Estimated reading time: 4 minutes
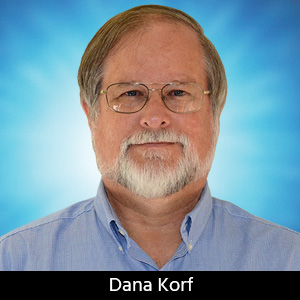
Dana on Data: Effective Front-end Engineering External KPIs
PCB fabricator front-end engineering departments are always under great pressure to be kept small, generate production tooling instantaneously from customer data, and never, ever, make a mistake. They are generally given non-black-and-white design rules from process engineering and poor data quality from customers. Key performance indicators (KPIs) emphasize internal process improvements and are generally simple in nature, such as jobs/person/day and scrap dollars/month. The department relies on expensive software to automate the process. Unfortunately, third-party software is typically not utilized effectively, or as designed. Internally generated automation is generally primitive or non-existent due to the lack of an overall architecture or lack of programmer resources.
Figure 1: Front-end engineering inputs and outputs.
An improvement area that is often overlooked are using KPIs that measure external factors that can have significant impact on the traditional KPIs. These focus on the rules and changes from process engineering and customer data quality. Process engineers and customer designers do not intentionally provide bad information. Issues arise due to communication gaps and a lack of a formal corrective action process.
Process engineering is often understaffed introducing new processes, improving processes, training, and determining how to build new variations of customer designs. This results in poorly updated design rules causing changes to be transmitted to the FEE department via part number specific engineering change orders (ECOs).
PCB layout designers are generally behind schedule before they start due to project delays. They design the PCB based on the best information that they can get from material suppliers, fabricators, and assembly houses. The most common feedback method from manufacturing is the technical query (TQ) on a part number basis. Designer efficiencies are reduced when they respond to the TQ issues.
Process engineering, sales teams, field application engineers, and customers can help reduce the tooling cycle time and improve efficiencies by jointly working together to improve using these simple, effective KPIs.
Internal ECOs/Project KPI
Create a small team consisting of process engineering, FEE, and CAM automation folks. This KPI measures the effectiveness of the engineering process design rules, FEE personnel training and automation. Track every released production tool that has an issue requiring it to be re-generated. Do not just track tools that create scrap or rework. I have seen ECO handling consume up to 30% of FEE capacity.
Treat each ECO’d tool as defective, just as you would a defective core that requires to be re-built. Example defects range from artwork re-scales, etch compensation, drill file re-scaling, routing programs, traveler notes/sequences, stackup prepreg resin percentage adjustments, etc. Collect one month of data, pareto the results and address the top five defects. Use this data to update design rules, training, and automation. A vibrant ECO handling process should consume less than 10% of FEE capacity.
TQ Questions/job KPI
Most customer data packages generate one or more technical query (TQ) questions or suggestions that are sent back to the customer for resolution. Treat each question as a defect. These issues may be for myriad reasons such as the design is beyond process capability, yield improvement suggestions, cost reduction suggestions, conflicting documentation, missing information, impedance values, design violations, etc. The goal of every fabricator is to build the data as received and not have any TQs generated. Unfortunately, up to 95% of data packages require one or more TQs to be generated.
This KPI tracks the quantity of TQs per job. A secondary proactive KPI plots TQs/job by customer. The intent is to work with your customers who require the most TQs/job to jointly reduce the quantity. Improvements generally fall into three categories:
- Customer design rules may require to be updated to match the fabricator capability.
- The designer may not be able to agree to some suggestions. These can be eliminated for future jobs.
- Existing capability can be improved or extended to match the design requirements.
DFM’s Performed/Ordered Project
DFM reviews are an interesting area. Performing DFM reviews during the design cycle is an excellent relationship builder which generates business. It also can help the designer modify the design to be more compatible to the manufacturing process capability and provide a material stackup that can be used to order material early in preparation for the prototype build.
On the negative side, when a product engineer is reviewing preliminary data, they are not creating revenue generating tooling. DFM reviews can consume 25–50% of the FEE capacity. OEM and CEM NPI processes may require one or more DFM reviews during design from all potential suppliers.
Some designers will send DFM reviews to the supplier that has the quickest response time or has available capacity. But a DFM review will not always guarantee that an order will be placed. I have seen designers request DFMs for 10 or more parts and never place the order because of business reasons, pricing, delivery, etc. This KPI provides valuable insight into this. The sales team can work to eliminate DFM reviews for OEMs that do not order these PCBs. FAEs may also be able to review the design and provide suggestions without having to use FEE capacity.
Continuous improvement should always be embedded in every FEE department. Implementing these external KPIs can increase net capacity by reducing nonvalue added work which pulls team members away from creating revenue producing tooling.
Dana Korf is the principal consultant at Korf Consultancy LLC.
More Columns from Dana on Data
Dana on Data: Best Practices in Interpreting Drawing Notes—‘Use Latest Revision’Dana on Data: The Missing AI-NPI Link
Dana on Data: Merging 2D Electrical, 3D Mechanical Worlds
Dana on Data: Resurrecting IPC Class 1
Dana on Data: The Evolution of Fabrication Drawing
Dana on Data: The Insane PCB DFM Process
Dana on Data: eCAD PCB Design Deficiencies
Dana on Data: Nuke the Netlist