-
- News
- Books
Featured Books
- design007 Magazine
Latest Issues
Current IssueProper Floor Planning
Floor planning decisions can make or break performance, manufacturability, and timelines. This month’s contributors weigh in with their best practices for proper floor planning and specific strategies to get it right.
Showing Some Constraint
A strong design constraint strategy carefully balances a wide range of electrical and manufacturing trade-offs. This month, we explore the key requirements, common challenges, and best practices behind building an effective constraint strategy.
All About That Route
Most designers favor manual routing, but today's interactive autorouters may be changing designers' minds by allowing users more direct control. In this issue, our expert contributors discuss a variety of manual and autorouting strategies.
- Articles
- Columns
- Links
- Media kit
||| MENU - design007 Magazine
Estimated reading time: 4 minutes
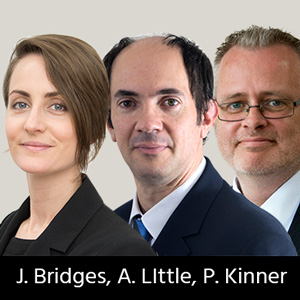
Sensible Design: Conformal Coating Vs. Encapsulation Resin
Without a doubt, the biggest question we get asked regularly at Electrolube is, “When is it suitable to use a conformal coating or an encapsulated resin?” There are several considerations that will determine the answer; however, it depends largely on how the circuit will be housed within the assembly as well as the type of environment in which it will operate. For instance, if the PCB housing design is intended to deliver the primary environmental protection, we would recommend using a conformal coating as it will act as the second line of defence in the event of any housing seal failure.
Alternatively, where there is no separate housing or capacity to provide primary environmental protection, then an encapsulation resin is likely to be the better choice. Clearly, there will be applications where the choice of technology is obvious, for example, where duty in a harsh environment demands the highest level of protection. In this case, a potting and encapsulation resin will provide the necessary long-term protection—so long as the correct resin has been selected, tested, and approved for the prevailing environmental conditions.
Where ease and speed of processing are important, conformal coatings will always be the preferred choice, particularly as the thin cured film of a modern, well-formulated coating can provide a high level of protection in any case. Most of these coatings are single-part systems that are easy to apply and quick to cure with little temperature rise. On the downside, single-part coatings are solvent based to modify their viscosity for application purposes, which can have environmental repercussions.
Conformal coatings can be applied manually using a paint brush, a spray gun, or simply by dipping the circuit board into a bath containing the coating material. Where large numbers of circuits must be treated in a fast-moving production line, coatings are more likely to be applied by closely controlled robotic selective-coating systems for maximum consistency. Conformal coatings are applied in their liquid state as thin films which cure to provide a dry film thickness of between 25 and 100 microns, adding minimal weight increase to the assembly. These coatings are usually clear and allow rework, so coated components are visible and easy to replace. The level of chemical resistance and thermal protection that conformal coatings provide is generally good for short exposures.
Encapsulation resins and potting compounds can be applied in thicknesses from 0.5 mm, but are generally applied much thicker than this, which can lead to a significant weight gain for the assembly. Weight gain aside, this increased thickness does mean that the PCB is far better protected against chemical attack, particularly in cases of prolonged immersion. Depending upon the formulation, a resin can also provide superior protection against physical shock since its bulk will help to dissipate the forces across the PCB, rather than allowing them to be concentrated. A bonus for protecting your intellectual property and design advantages, a layer of dark-coloured resin can obscure the circuit layout and components from prying eyes. One thing to remember, though, is that attempting to remove the resin will damage the PCB, severely limiting opportunities for component replacements.
Compounds and resins are generally two-part systems, in which a resin is mixed with a hardener in a precise ratio to form a cross-linked polymer when cured. It’s also possible to add mineral substances (fillers) to resins to improve their performance under certain operating conditions. Like conformal coatings, most resins will cure at room temperature, and while this can be a relatively slow process in the case of potting resins, cure time can be reduced by applying heat.
It might interest you to learn that, in certain applications, where a two-part resin formulation may have been the first choice for circuit protection, a two-part conformal coating may turn out to be the better approach, thanks to its superior mechanical properties, as compared with one-part coatings. For example, Electrolube developed the 2K range of solvent-free coating materials, based on similar two-part chemistry to resins, but designed to be applied by selective coating equipment in the 200–400-micron range, combining many of the advantages of both technologies and minimising many of the drawbacks of each. Moreover, switching from a resin to a conformal coating will eliminate the weight penalties of the former, which may be critical to some applications. Two-part conformal coatings can be applied relatively thickly without risk of cracking, giving a sharp edge coverage that performs somewhere between where a conventional conformal coating fails, and potting is required. A two-part conformal coating’s environmental protection capability is also rather impressive.
For example, in environmental chamber trials simulating highly condensing conditions, while a urethane resin potted assembly gave the highest overall values in terms of circuit protection—and showed the least change during condensing events—the very large difference in thickness between it and a two-part conformal coating didn’t show a large increase in performance. Indeed, the two-part coating achieved much the same results as the potting compound at one-tenth the thickness.
Despite these advances in conformal coating chemistries, potting and encapsulation resins will always offer the highest level of protection for PCBs, whether used to protect against mechanical shock and vibration, thermal cycling, chemical attack, or the presence of high voltages where maximum dielectric strength is needed to avoid damaging discharges and leakage currents. The trade-offs are added weight, loss of rework capability, longer processing times, and high cure temperatures.
If you do experience problems choosing between these methods of circuit protection, remember, there are experts out there to help. And it is always worthwhile taking the trouble to test alternative methods of protection, preferably at the prototype stage, before you make your final choice; the experts are ready to help you with this task as well.
This column originally appeared in the May 2021 issue of Design007 Magazine.
More Columns from Sensible Design
Sensible Design: Automotive Conformal Coating ApplicationsSensible Design: Green Coats Are In
Sensible Design: Encapsulation Resins—PU vs. Epoxy
Sensible Design: Avoiding Conformal Coating Pitfalls
Sensible Design: Comparing Traditional and Bio-based Resins
Sensible Design: All Resins Are Not Created Equal
Sensible Design: Can Solvent-free UV-cure Coatings Increase Stability and Throughput?
Sensible Design: Optimize Your Thermal Management