-
- News
- Books
Featured Books
- pcb007 Magazine
Latest Issues
Current IssueInventing the Future with SEL
Two years after launching its state-of-the-art PCB facility, SEL shares lessons in vision, execution, and innovation, plus insights from industry icons and technology leaders shaping the future of PCB fabrication.
Sales: From Pitch to PO
From the first cold call to finally receiving that first purchase order, the July PCB007 Magazine breaks down some critical parts of the sales stack. To up your sales game, read on!
The Hole Truth: Via Integrity in an HDI World
From the drilled hole to registration across multiple sequential lamination cycles, to the quality of your copper plating, via reliability in an HDI world is becoming an ever-greater challenge. This month we look at “The Hole Truth,” from creating the “perfect” via to how you can assure via quality and reliability, the first time, every time.
- Articles
- Columns
- Links
- Media kit
||| MENU - pcb007 Magazine
Estimated reading time: 4 minutes
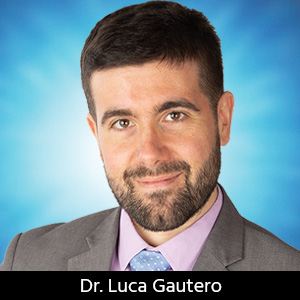
Additive Reality: Drop Placement Accuracy
When Gessler sentenced William Tell to shoot an apple placed on the head of his son, he accepted it with both confidence and some uncertainty. In fact, he had more arrows prepared: a misfire, aside from ending his son’s life, would have brought Mr. Tell to shoot the cruel Swiss commissioner Gessler with a second dart.
Let us take an engineering spin to this story. William had on his side an apple and the experience of all previous shots. Not only did he have to hit the apple, but he also had to be sure that his variation around the goal was always smaller than the apple. Such sureness can only come from taking many thousands of shots. The infinite love of a father for an offspring makes us believe that he took the challenge because he had that kind of experience. We know how the story goes: split apple and son saved.
How does this relate to inkjet equipment for solder mask coating? As a rough explanation, inkjet is a multitude of shots of tiny liquid drops to form a pattern. The shooting distance is approximately one millimeter, and the drop placement accuracy is tight, preferably well within the drop size upon landing. At a smaller scale, every shot is the Swiss story all over again. Therefore, the equipment is, all at the same time, William Tell, his crossbow, and the darts. It alone solves the challenges toward the accuracy.
In the following, each paragraph illustrates what ensures accuracy with every shot, using a few basic concepts; therefore, here is a brief introduction of trueness and precision (as defined by ISO5725). Trueness is the average difference of the real value from the desired value, precision is the range of variation while measuring the same value. William Tell not only hit the apple, but he split it in two, so both trueness and precision are much smaller than an apple as pictured below.
Figure 1: A visual explanation of how trueness and precision affect accuracy.
Every inkjet printing tool reports its stage trueness (also called “accuracy” due to the common technical definition before the ISO standard) and precision. The first indicates how close the movement stage can bring the printing unit to the desired location, the second indicates how well the movement stage can return to the same point close to the desired location. The only requirement is an environment (temperature, humidity, and vibrations) kept within operating range. Normally, precision is better than trueness, and both are well below the size of a drop on the surface. Furthermore, when alignment procedures are used, the trueness no longer affects the result. Only the ability to come back to the same spot is important.
Unfortunately, the stage does not represent the whole drop placement error budget, so what is left?
The shooting device–the printing unit–will also introduce trueness and precision. This unit, in industrial tools, is composed of an array of printheads and their reciprocal alignment is crucial for image printing. This alignment is a six-dimensional challenge: three perpendicular axes and three rotational axes. Additionally, since printheads are consumables, they need to be quickly replaceable. The common choice is a quick release system with tight mechanical references, together with a calibration procedure. The coarse mechanical alignment ensures a reasonably small trueness. Still, the calibration will finely remove the trueness left by informing the image rendering algorithms. The skill of the machine supplier is to wisely combine mechanical and digital correction toward fast maintenance and quick computation time.
A well-defined printing unit, which moves to the desired place, is a good start. However, two more layers need explanation: the shooting and the apple.
The shooting, appropriately named “jetting,” relies heavily on the ink rheology. For the sake of this description, we assume a combination of ink and waveform that delivers a high-speed drop without satellites or long tails. What is then left are the variation of jetting speed and straightness. Each drop comes out of a nozzle in a printhead. The equipment supplier will combine and tune the printheads and the stage movement to obtain a predictable landing position on the substrate. Once again, accurate calibration removes any trueness introduced by even tiny inevitable mismatches between printheads. Luckily, specialized companies supply such parts to the inkjet tool manufacturer. These parts benefit from the huge development in inkjet graphics over the last few decades. As an example, MEMS printheads benefit from a nanometric lithographic definition of the nozzle plate. Thousands of nozzles within a single printhead have tight position margin and homogeneous jetting capabilities.
Finally, the apple or, in this case of an inkjet tool for solder mask coating, the “PCB substrate.” Two identical apples do not exist; the same is true about PCB substrates. The alignment procedure has the task to find the substrate as well as reveal its own uniquely deformed shape. The latter is compared to the computer aided manufacturing definition to quantify the trueness. Therefore, its compensation is readily at hand: the image rasterization process considers the alignment and deformation information and prepares the right artwork for each board.
Now that the major accuracy challenges and their solutions are detailed, it is easier for the reader to understand why an inkjet tool can achieve such high fidelity despite its complexity. The challenge of the apple repeats itself several billion times over for each board by relying on the described technologies. A single board alone carries a valid proof of the process repeatability.
Luca Gautero is product manager at SÜSS MicroTec.
More Columns from Additive Reality
Additive Reality: Drop It, and Enjoy the GreenbackAdditive Reality: Let's Drop a Line About PCB Cross Section
Additive Reality: Drop-forging Solder Mask Thickness With Inkjet
Additive Reality: Isolated Raindrops Announce the Storm
Additive Reality: Green Drops, White Drops or Both: Do Solder Mask and Legend Make a Good Team?
Additive Reality: A Report From 2021 (Drop)tronica
Additive Reality: Your Company Drops Open the Inkjet Printer Box, Now What?
Additive Reality: Drop Your (Solder) Mask, It's Sampling Time