-
- News
- Books
Featured Books
- pcb007 Magazine
Latest Issues
Current IssueInventing the Future with SEL
Two years after launching its state-of-the-art PCB facility, SEL shares lessons in vision, execution, and innovation, plus insights from industry icons and technology leaders shaping the future of PCB fabrication.
Sales: From Pitch to PO
From the first cold call to finally receiving that first purchase order, the July PCB007 Magazine breaks down some critical parts of the sales stack. To up your sales game, read on!
The Hole Truth: Via Integrity in an HDI World
From the drilled hole to registration across multiple sequential lamination cycles, to the quality of your copper plating, via reliability in an HDI world is becoming an ever-greater challenge. This month we look at “The Hole Truth,” from creating the “perfect” via to how you can assure via quality and reliability, the first time, every time.
- Articles
- Columns
- Links
- Media kit
||| MENU - pcb007 Magazine
Estimated reading time: 6 minutes
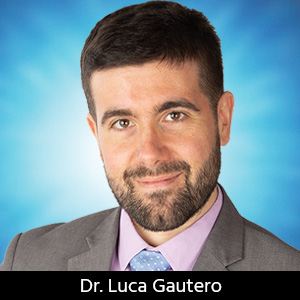
Additive Reality: Your Company Drops Open the Inkjet Printer Box, Now What?
The moment will come when some of you readers will advance from interest to complete involvement with the technology. This will be a fun ride as you will experience first-hand the concepts seen so far in this column. However, we all know that any reliable technology relies on one healthy, not so exciting, good habit: preventive maintenance.
Preventive maintenance and incidental repairs are not the same, though they might follow the same instructions. Still, this does not mean that these are interchangeable. The last section will mention incidental repairs and why, in my opinion, this is the right technological age to be less averse to these issues.
For now, the focus will be on the good old preventive maintenance, as a habit—or even better—a tiny habit.1 As a tiny habit, the focus should be on the ability to perform the action or behavior, and on the prompt. The clearer the prompt, the easier it is to begin a task. The more able the person is, the less motivation is needed.
This is why equipment manufacturers write manuals (which facilitate ability) and provide a scheduling routine (facilitating a prompt). A simple copy-paste of the SÜSS MicroTec maintenance manual would fit this column nicely, though this would not be fair to the technology and to the many valuable competing inkjet printing solutions out there. So, here are independent tool maintenance considerations.
The manuals will support the service and the operator engineer alike with descriptions of the activities. These can target the tool itself with the usual: everything that moves, everything that flows (water, ink and CDA), and everything that perishes. The first will need calibration and lubrication, the second will need operational procedures to commissioning and decommissioning as well as replacing consumables (filters, printheads, sensors, valves, etc.), and the third will have either a schedule or warning messages to heed.
As motivation, here is a brief summary of past topics that touched maintenance in one way or the other. My first column highlighted the importance of the calibration procedures for accuracy. The second column reviewed the materials involved in the printing and their essential role; the printer must therefore deliver materials (actually, only the ink) in a preserved state to the substrate. Furthermore, maintenance can be a criterion for the printhead and ink material combination (third column) since the lifetime of each single nozzle will be crucial in the reproducibility of production. The fourth column detailed the importance the UV light is as a solidification mechanism. Indeed, UV lights are an example of scheduled check. This avoids size shifts on the printed feature.
These items need illustration for each machine brand, and soon enough these will be second nature for the skilled service engineer owning one of them. So far, we have been enumerating common sense and it has been good to review it. Amongst these was the delicate, and unique to inkjet, printhead maintenance.
A Few Points of Attention
Material compatibility as a first reference for maintenance
It is an equipment manufacturer’s duty to ensure material compatibility between functional ink and printhead. Ink suppliers and equipment suppliers collaborate by aging a set of materials. These represent the printhead and other components in direct contact with the ink. All material must pass the criteria: during the aging (performed at the ink operating temperature), the growth in volume or weight must be below the threshold (for example, 5%). Failure results in a replacement with a more suitable material candidate. This repeats until the whole ink system is inert to the ink material. This procedure will ensure a minimal number of sudden and inexplicable performance shifts, breakages, and leaks. There can also be cases in which this procedure gives insight on the maximum operational lifetime of components. Therefore, solid knowledge justifies scheduled replacement.
Figure 1: Several candidate alternative materials and the original system material undergo the test in parallel, sometimes, even the alternatives selected are a compromise. These materials will be addressed by a scheduled check or replacement.
Printhead priming
Filling a beaker with a liquid is simple, though when you look closely, you are likely to find air bubbles or remainders from a previous liquid. The severity of these misses depends on the use of the beaker. When the beaker is instead a pressure driven system (a printhead), air bubbles lead to failures. Furthermore, unwanted remainders of immiscible liquids can create havoc in a printhead. These issues mostly show themselves as jet failures. The challenge is clear; the preventing action is a correct printhead priming: a series of actions that ensure absence of air and immiscible liquids.
Once again, suppliers collaborate to create a safe operating procedure for priming. Printhead suppliers, ink suppliers, and equipment suppliers define a sequence of miscible solvents. These will flush the printhead out of its “travelling liquid” (the liquid inside the printhead while on the shelf at the printhead supplier’s stock). The flushing out procedure continues until the flushing liquid fills the printhead. Then the functional liquid, in our case a solder mask ink, follows it. The ink supplier indicates or formulates the dedicated flushing liquid for the priming. Since the priming of a printhead can be done in advance, the complexity of this operation is normally not an issue, as long as the goal is achieved. It is then a choice of the supplier and the customer on who performs such operation. The maintenance manual will reflect such a choice.
Wiping and purging
My third column detailed the choice of the heads to facilitate operation as (manual) wiping. Since production rhythms impose multiple heads, having a seamless nozzle plate composed of multiple heads will make the wiping easier and more consistent. Still, these two operations—wiping and purging— should be the exception more than the rule. A diligent preparation work, as described in the previous two paragraphs, result in weekly or monthly wiping and purging operations. One personal thought: I question the profitability of purging expensive ink and I strongly doubt that purged inks are re-usable.
Expiration date
All inks, and flushing liquids, come with an expiration date. Keep your stock in check.
Incidental Repairs: What Happens When We Throw in Data?
While a lot happens, we still have the ground rule: preventive maintenance is here to stay. Knowledge will complement it without replacing. Data is the buzzword of the decade. I am an amateur data scientist; my opinion is that six-sigma methodology, and especially DMAIC approaches, have become too cheap to skip. Therefore, incidental maintenance moves from “what happened,” which is a human-driven root cause finding based on visual and instrumental off-line inspection, to other levels. Nowadays, the intensive logging already available on the tools delivers “what is happening now”. This supports the root cause finding and makes it smarter. A bigger step will be moving to predictive and prescriptive maintenance. In these steps, respectively, the tool has a built-in algorithm that recognizes situations by inspecting the data according to a structure derived from previous root cause analyses or, in a prescriptive case, it will detect complex anomalies from unstructured data. This chapter of maintenance might not be far ahead, especially for digital technologies as inkjet printing.
References
1. Fogg, B. J., “Tiny Habits: The Small Changes that Change Everything,” Houghton Mifflin Harcourt, 2019.
Luca Gautero is product manager at SÜSS MicroTec (Netherlands) B.V.
More Columns from Additive Reality
Additive Reality: Drop It, and Enjoy the GreenbackAdditive Reality: Let's Drop a Line About PCB Cross Section
Additive Reality: Drop-forging Solder Mask Thickness With Inkjet
Additive Reality: Isolated Raindrops Announce the Storm
Additive Reality: Green Drops, White Drops or Both: Do Solder Mask and Legend Make a Good Team?
Additive Reality: A Report From 2021 (Drop)tronica
Additive Reality: Drop Your (Solder) Mask, It's Sampling Time
Additive Reality: Solder Mask Patterning at the Edge Between Drops and Bricks