-
- News
- Books
Featured Books
- pcb007 Magazine
Latest Issues
Current IssueInventing the Future with SEL
Two years after launching its state-of-the-art PCB facility, SEL shares lessons in vision, execution, and innovation, plus insights from industry icons and technology leaders shaping the future of PCB fabrication.
Sales: From Pitch to PO
From the first cold call to finally receiving that first purchase order, the July PCB007 Magazine breaks down some critical parts of the sales stack. To up your sales game, read on!
The Hole Truth: Via Integrity in an HDI World
From the drilled hole to registration across multiple sequential lamination cycles, to the quality of your copper plating, via reliability in an HDI world is becoming an ever-greater challenge. This month we look at “The Hole Truth,” from creating the “perfect” via to how you can assure via quality and reliability, the first time, every time.
- Articles
- Columns
- Links
- Media kit
||| MENU - pcb007 Magazine
Estimated reading time: 3 minutes
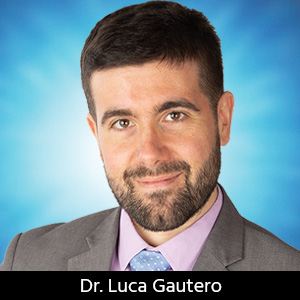
Additive Reality: Green Drops, White Drops or Both: Do Solder Mask and Legend Make a Good Team?
Combining solder mask printing and legend printing seems like an obvious and attractive solution, sort of like bringing chocolate and vanilla together. Still, the gain relies on obtaining both functionalities without adding complexity. However, from the summary consideration in my December column on the equipment construction, two separate printhead arrays would best match the different requirements of legend and solder mask. In this column, the story continues.
One favorable advantage of a one-tool configuration is a single alignment step serving both coating processes. In the common configuration of printers, the alignment step bounds the table position to the substrate position. This means one substrate, one table. Even when the single tool has two printhead arrays, if a single table services the printing processes, parallelizing solder mask and legend coating remains unfeasible. Furthermore, the legend printing starts only after the solder mask coating is completed. Therefore, these two processes are strictly sequential on the same substrate.
Figure 1 represents a possible sequencing of processing steps. It shows explicitly how each of the two configurations—first, the one tool that integrates solder mask and legend coating, and second, the two separate tools, one for each process—would process several substrates (made visual using different colors). The time assigned to each process follows reasonable assumptions: solder mask printing takes slightly longer than legend printing, alignment time is the same, the load/unload time stays below processing time, and finally, the timing of these steps is common to both configurations.
Figure 1: Simplified example of process sequencing. For the one tool configuration, process time (dashed arrow) and TACT time (full arrow) are equal by design. Meanwhile, the two tools configuration sees an increase of the process time for the benefit of a shorter TACT time.
The total average cycle time (TACT) is an important tool and process description. In a production floor with several tools, it is the highest TACT that defines the throughput of the complete production line. For this reason, the design of a line has a given target throughput for all incoming tools. This simplifies the optimization of the sequencing since all tools have a similar TACT.
For the one tool configuration, the TACT and the process time are the same. Only investments in additional tools will result in throughput increases. For the two tools configuration instead, it might suffice to invest in the slower of the two. The latter is most convenient; each of the two tools is cheaper than the all-capable one tool and its more complex printhead setup.
Once again, it is about which investment strategy better fits the PCB manufacturer. I’m writing this column during the holidays, which is a good time to finally get to read my bookmarked PCB007 articles and give them the attention they deserve. On my (digital) shelf is the October 2021 CapEx issue. I want to better understand the industry’s customary approach to investment and its way of approaching novel trends imposed by legislation, PCB geopolitics, or the ongoing pandemic.
Reading the concluding words of Sunny Patel, who has just introduced to his company an additive manufacturing tool for solder mask (and legend), is refreshing. Furthermore, it shows that although TACT considerations might be sound, a small shift in the requirements, for example lower pattern fidelity, brightens the picture for a one tool solution. In the interview with Peter Bigelow, he brings fairness to the investment decision process, sharing with us his experience, partitioning, and timeline of typical investment plans for the PCB industry. Both give validity to this Additive Reality column. The best investment is the one where all information is at hand. For this reason, my columns this year will continue by illustrating several technological advantages of inkjet solder mask. Some will be demonstrated facts and others will be potential advantages.
I offer my warmest wishes for a wonderful 2022, and I’ll see you in this space again next month.
Luca Gautero is product manager at SUSS MicroTec (Netherlands) B.V.
More Columns from Additive Reality
Additive Reality: Drop It, and Enjoy the GreenbackAdditive Reality: Let's Drop a Line About PCB Cross Section
Additive Reality: Drop-forging Solder Mask Thickness With Inkjet
Additive Reality: Isolated Raindrops Announce the Storm
Additive Reality: A Report From 2021 (Drop)tronica
Additive Reality: Your Company Drops Open the Inkjet Printer Box, Now What?
Additive Reality: Drop Your (Solder) Mask, It's Sampling Time
Additive Reality: Solder Mask Patterning at the Edge Between Drops and Bricks