-
- News
- Books
Featured Books
- pcb007 Magazine
Latest Issues
Current IssueInventing the Future with SEL
Two years after launching its state-of-the-art PCB facility, SEL shares lessons in vision, execution, and innovation, plus insights from industry icons and technology leaders shaping the future of PCB fabrication.
Sales: From Pitch to PO
From the first cold call to finally receiving that first purchase order, the July PCB007 Magazine breaks down some critical parts of the sales stack. To up your sales game, read on!
The Hole Truth: Via Integrity in an HDI World
From the drilled hole to registration across multiple sequential lamination cycles, to the quality of your copper plating, via reliability in an HDI world is becoming an ever-greater challenge. This month we look at “The Hole Truth,” from creating the “perfect” via to how you can assure via quality and reliability, the first time, every time.
- Articles
- Columns
- Links
- Media kit
||| MENU - pcb007 Magazine
Estimated reading time: 4 minutes
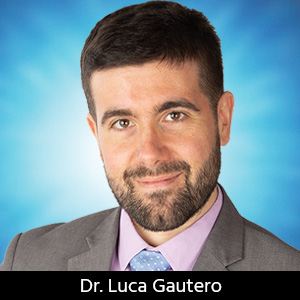
Additive Reality: Drop It, and Enjoy the Greenback
The columns so far have brought up the technical aspects of inkjet solder mask and made readers more familiar with this technology. This last column instead will show how the technical aspects match the commercial ones. It will start by introducing the main change in the manufacturing compromise and then the general details on payback period1.
Presently, traditional solder mask has been a balance between accuracy and throughput. Inkjet brings one more dimension: the copper thickness (Figure 1). A single print coating process by inkjet can handle thick or thin copper, in other words, the same inkjet tool is able to coat this thicker copper with fidelity to narrow features, fast, or a compromise between the two.
Figure 1: a) A traditional compromise, what do you want? Accuracy or throughput?; b) Inkjet compromise, still a choice to make, though, a useful one.
Of course, traditional technology can create thick solder mask and therefore sufficiently cover thick copper traces. However, solder mask coated with inkjet would be conformal (Figure 2); additionally, it would require much less solder mask material compared to traditional solder mask deposition methods.
Figure 2: Example of a thick, solder mask coated, copper trace (91µm, ~3.58mil, ~3 ounce). In this situation, the inkjet coating technology targets 24 µm on copper and on laminate. Traditional coating technologies for solder mask, like curtain, spray, or screen printing, would be able to achieve the desired thickness on copper, and especially its edges, by “wasting” a large amount of solder mask on the laminate. This is the perfect example of the advantages of additive manufacturing for electronics.
In Figure 1b, any compromise is within the green factor. Any chosen configuration will bring reduction of CO2emission, direct (by lowering energy consumption) or indirect (by diminishing consumable usage). An eye on the future tells you that such emission will become expensive. The focus on now tells you how easy it is to market a low CO2 emission board to your customers.
The traditional coating of solder mask is a well-established manufacturing technology. Intensive and long-lived market competition fully optimized production costs, both on the investment (CAPEX) and the consumables (OPEX). Any company can generate the numbers:
- Running costs as energy, consumables, and waste treatments
- Floor space and the related permits
- Labor will show up as the drivers for the payback period
Present configuration can expect a return within few years. The companies running production with inkjet solder mask welcome the reduction in consumables of approximately 80% and the reduction of floor space (with its facility) down to a tenth. Additionally, they see that labor evolves. The skills level needed better matches the staff qualifications and the production floor environment is healthier, thanks to the lower amount of solder mask material and its virtual absence of volatile organic components (VOC). This makes OPEX only a fraction. This means more return per board.
However, the intelligence placed in the match between inkjet and solder mask together with the technological hardware reflects in the CapEX. Luckily, the one investment in inkjet replaces several ones: coater, driers, LDI tools, wet lines, and more. In the end, it all comes down to numbers. These numbers make the Total Cost of Ownership (TCO) calculation. Such calculation can provide a comparison between traditional technology and inkjet and boil it down to a single number: the number of years of the payback period.
The more accurate the numbers, the better the insight, so I cycled to a nearby PCB manufacturer and obtained the numbers with a scenario of a few hundred thousand panels per year. Of course, in these numbers, there is much of the SUSS machine running costs, so, for the unbiased character of this column, I will not disclose numbers, only aggregated trends. It was evident that inkjet investment is higher; thanks to the low OPEX, the Net Present Value (NPV) reaches zero one year before the traditional technology. Not only payback period is one year better, since OPEX is lower, every year means less cost for the same boards produced. In view of these numbers, it is a no-brainer.
Before closing, let me go back to the green factor. The production of the boards is more independent from fluctuation in electricity price and waste disposal. These forecasted factors cannot enter the TCO, though the fact remains that each board will have a smaller CO2 footprint. The only logical step then will be to inform the marketing department and get a nice “green factor” logo done.
As mentioned at the beginning, this is the last column. I will take a creative break. If you enjoyed the column so far, you might find the upcoming FED conference in Potsdam and its digital solder mask panel very interesting. I will be glad to welcome you there.
P.S. My usual bike stroll is a few kilometers more than you might think. I am currently training for a charity activity that involves biking.
References
- “Payback Period,” by Julia Kagan, Feb. 7, 2022, Investopedia.com.
Luca Gautero is product manager at SUSS MicroTec (Netherlands) B.V.
More Columns from Additive Reality
Additive Reality: Let's Drop a Line About PCB Cross SectionAdditive Reality: Drop-forging Solder Mask Thickness With Inkjet
Additive Reality: Isolated Raindrops Announce the Storm
Additive Reality: Green Drops, White Drops or Both: Do Solder Mask and Legend Make a Good Team?
Additive Reality: A Report From 2021 (Drop)tronica
Additive Reality: Your Company Drops Open the Inkjet Printer Box, Now What?
Additive Reality: Drop Your (Solder) Mask, It's Sampling Time
Additive Reality: Solder Mask Patterning at the Edge Between Drops and Bricks