-
- News
- Books
Featured Books
- pcb007 Magazine
Latest Issues
Current IssueInventing the Future with SEL
Two years after launching its state-of-the-art PCB facility, SEL shares lessons in vision, execution, and innovation, plus insights from industry icons and technology leaders shaping the future of PCB fabrication.
Sales: From Pitch to PO
From the first cold call to finally receiving that first purchase order, the July PCB007 Magazine breaks down some critical parts of the sales stack. To up your sales game, read on!
The Hole Truth: Via Integrity in an HDI World
From the drilled hole to registration across multiple sequential lamination cycles, to the quality of your copper plating, via reliability in an HDI world is becoming an ever-greater challenge. This month we look at “The Hole Truth,” from creating the “perfect” via to how you can assure via quality and reliability, the first time, every time.
- Articles
- Columns
- Links
- Media kit
||| MENU - pcb007 Magazine
Estimated reading time: 6 minutes
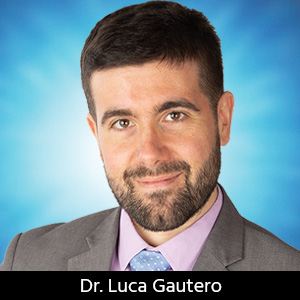
Additive Reality: Drop Your (Solder) Mask, It's Sampling Time
Reading back my last column, I didn’t like it much; it was a “straight to business” style and despite this accelerating society, I realized it might not be a good way to convey information. Your time here should be informative and pleasant. Bear with me and give today’s column another try.
Many countries nowadays are relaxing restrictions in public places. During the pandemic, supermarkets have provided continuous support for our needs, even though most of us have reduced our grocery visits to a minimum. In the future, we might come back to enjoy an occasional free sampling (“If it has a toothpick in it, it's free!” BH Simpson by Matt Groening), and our taste buds will provide us with accurate information about what we buy. Why this initial digression? Inkjet printing equipment around the world is printing solder mask on PCB half fabricates. This effort goes under the name of “sampling.” Major PCB manufacturers have been asking either equipment or material suppliers (or both) to provide a solder mask coated sample with inkjet technology to make cross comparisons.
The world may not yet know the capabilities of this technology, though; it is a fair assumption that in almost every PCB manufacturing company someone has seen a solder mask coated by inkjet printing on a design and a board of their choice. On one hand, this is the best way to demonstrate the technology; on the other hand, it is a collective waste of time. This last statement is a strong one, though one single sentence easily sustains it: There are no standards for inkjet printing of solder mask. This means that the presumed “next best thing” happens: a board is qualified with a comparison to traditional technology.
Through my columns so far, it has been shown several times that a printed solder mask can have the same pattern as a traditional solder mask coating, though its cross section is largely different. The dome shape of a dam cross section or the slow ramp from edge toward full thickness is nothing alike a vertical wall. Even more, it will never resemble the steep slope idealized by the traditional solder mask coating technology.
All samplings aim to provide information toward the acquisition of a technology, which means the bottom line is the driver. Sampling should primarily give the customer an idea of the quality of the coating; in other words, its insulation capabilities and mechanical stability against rough conditions; and then an idea of the tool cost drivers. For example, the amount of material used, the amount of operator time, the number of facilities consumed, and so on. Still, when the board is qualified compared with traditional technology, the focus quickly goes elsewhere.
Rarely, between all these designs and boards, comes a relevant one—a pattern optimized for inkjet printing, where the laminate (for example the FR-4) is not covered by solder mask to save material; where most, if not all, of the pads are solder mask defined; and where the thicknesses is clearly stated by location. A pattern defined in this way will actually bring forth interesting properties such as material saving and thickness design. The amount of samples also could provide information. One single board as a test vehicle will force the equipment supplier to use any trick in the book to make this “one shot” look like a “bull’s eye.” Instead, tens of boards, if not hundreds, will force the equipment supplier to show reproducibility and running costs of an existing baseline. These patterns and requests are relevant for the bottom line. These will show whether the much-praised merits of inkjet solder mask actually motivate the PCB manufacturer toward the acquisition of this digital additive technology.
Unfortunately, such patterns and additional requests do not yet figure in a standard document, like the ones developed by IPC or PCB assembly specifications. Therefore, perfect is not defined, good is never good enough, and opinions are stopping the inkjet technology at the gate.
Regardless, there is not much to do about it between now and tomorrow. All parties contribute to this continuous effort over time. Material and equipment suppliers, together with PCB manufacturers and their customers, will iteratively show these capabilities and eventually, improve our collective understanding, It will become obvious how inkjet should be likely to deliver a better bottom line.
Describing the Capabilities
When describing the capabilities of the inkjet equipment, the discussion often starts with the line space (or L/S). This is a measure of the minimum possible line width, and the minimum possible space between two lines. There are several reasons why this belongs in an “elevator pitch” moment. Understandably, such a number is useful to demonstrate that inkjet is an interesting technology. However, it takes for granted other aspects. The pitch receiver must assume that the positioning accuracy of the line or the space is perfect, and that any thickness is, of course, possible. Being as this is the real world, restrictions apply to these aspects. All the same, mentioning directly these two in numbers would not help PCB manufacturers to understand whether inkjet printing will create or solve any present or future challenge.
With this simple, and yet very powerful, illustration of typical solder mask dimensions (Figure 1), it is possible to explain the challenges. In Figure 1, a) shows values that relate to copper feature. These constraints define the specifications for solder mask, or vice versa, the solder mask specifications define the minimum copper feature size.
Figure 1: Illustration of a) typical copper; and b) solder mask dimensions. (Source: Eurocircuit1)
The focus now is on b), which displays values that refer to solder mask definition. Primarily, the minimum annular ring (MAR) from IPC-A-600 (7-31a) Edition 2010 is a combination of how accurately the machine can find the feature and how much control the machine and the pre-treatment offer on the edge of the jetted and cured solder mask. The MAR is crucial for PCB fabrication. When a machine cannot align to the copper layer or is not able to control the edge of the solder mask, then the pattern will fail. This specification goes also by “clearance,” “expansion,” or “freistellung” in German. Next comes the Mask SegMent (MSM), defined by the minimum trace width, which relates to the coalescence of drops. This goes also by the name of “solder mask web,” “bridge,” or “lötstoppmaskensteg” in German. Finally, we have the mask overlap clearance (MOC), which tells us about how the solder mask wraps around a copper trace. As with the previous ones, this acronym has other names: “coverage,” “cover,” or “leiterbahnabdeckung” in German.
What is missing here is the thickness. This is very understandable, since a traditional solder mask has very limited capabilities to offer any degree of thickness freedom; therefore, it is not interesting to specify any number. Once the numbers above are seen together with their thickness (Figure 2), their build up becomes evident. In my previous column, I explained how inkjet layer thickness meets such specifications as MOC, MSM, A, and B.
Figure 2: Cross section with unequal scales for height and width. (Source: SUSS JETxSM TPI)
Even when coupling these requirements (MAR, MOC, MSM) to a thickness specification, there will be interesting features that are not captured. One example is a complete solder mask bridge between pads. This would be a good compromise between the present solder mask defined (SMD) and non-solder mask defined (NSMD) designs (Figure 3).
Figure 3: Cross section of a complete solder mask bridge between pads. (Source: SMTAI Technical Conference2)
It is my opinion that sampling effort targets pioneers, curious and risk-averse companies alike. The last group is the most numerous; so much of the sampling will remain a pure exercise. Still, all this muscle flexing and iterative improvement will serve to bring a well-thought-out inkjet baseline to the attention of pioneers. I hope that future samplings will contain the questions that elucidate the improvements of the bottom-line. Such moment might anticipate the hoped for “hockey stick” adoption moment for inkjet printing of solder mask.
References
- PCB Design Guidelines, Solder Mask, Eurocircuits.
- “Varying Requirements, Same Inkjet Solder Mask Coating Tool—The Case of Inkjet Adaptability by Printing Strategies,” Bas Le Grand, Luca Gautero, Ph.D., SUSS MicroTec NL. Proceeding from SMTA International Conference and Expo, November 2021, Minneapolis, Minnesota.
Luca Gautero is product manager at SUSS MicroTec (Netherlands) B.V.
More Columns from Additive Reality
Additive Reality: Drop It, and Enjoy the GreenbackAdditive Reality: Let's Drop a Line About PCB Cross Section
Additive Reality: Drop-forging Solder Mask Thickness With Inkjet
Additive Reality: Isolated Raindrops Announce the Storm
Additive Reality: Green Drops, White Drops or Both: Do Solder Mask and Legend Make a Good Team?
Additive Reality: A Report From 2021 (Drop)tronica
Additive Reality: Your Company Drops Open the Inkjet Printer Box, Now What?
Additive Reality: Solder Mask Patterning at the Edge Between Drops and Bricks