-
- News
- Books
Featured Books
- pcb007 Magazine
Latest Issues
Current IssueInventing the Future with SEL
Two years after launching its state-of-the-art PCB facility, SEL shares lessons in vision, execution, and innovation, plus insights from industry icons and technology leaders shaping the future of PCB fabrication.
Sales: From Pitch to PO
From the first cold call to finally receiving that first purchase order, the July PCB007 Magazine breaks down some critical parts of the sales stack. To up your sales game, read on!
The Hole Truth: Via Integrity in an HDI World
From the drilled hole to registration across multiple sequential lamination cycles, to the quality of your copper plating, via reliability in an HDI world is becoming an ever-greater challenge. This month we look at “The Hole Truth,” from creating the “perfect” via to how you can assure via quality and reliability, the first time, every time.
- Articles
- Columns
- Links
- Media kit
||| MENU - pcb007 Magazine
Estimated reading time: 6 minutes
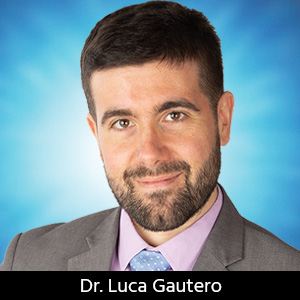
Additive Reality: A Report From 2021 (Drop)tronica
After months of social distancing, productronica brought people and ideas together in a single place. Its most pragmatic demonstrations were the tools on the floor of the B3 Hall at the München Messe. The fair had representations for almost all equipment needed for PCB manufacturing and inspection. Three of these tools were solder mask inkjet printers from different brands, as was the case in 2019—a sign that business has continued, albeit at a slow pace, through the pandemic period. However, this year there was another vibe, this time about additive manufacturing. At the entrance, an animation on a giant screen showed how a company is delivering a bottom-up approach for PCB prototyping—an inspiring manufacturing frontier on display at the doors.
This was a good start, although the real positive vibe about inkjet came from the many discussions with interested companies, technological partners, and competitors. From the companies, we learned that the production pressure of the past few months is good for business even though it leaves little room to put attention on future technologies. From the technological network, we learned that, even if the attention was limited, inkjet was the hottest discussion topic for the week. Even technology suppliers that have ground in solder mask, both traditional and additive, reported this overwhelming enthusiasm for the inkjet option.
When we had a discussion at our booth, we asked for a business card and entered that information on a sheet. These entries helped to organize follow-up discussions, in agreement with GDPR laws. However, an interesting perspective emerged when looking at them in an aggregated manner. What emerged were expansions and green field operations. All these plans had one contingency in mind: securing a PCB board supply in Europe. It’s easy to look at recent events, such as trade wars, the Suez Canal obstruction, and the pandemic, but in my view these are linear events. When you look at it through the perspective of exponential growth, it’s important to note the two technologies of energy and computing.1 In other words, the future fleet of electric cars will not build itself and the FAANGs2 of the world are not going anywhere; instead, they might get company. Incredible as it might be, these all start with a PCB board. It seems the right time to ask, “Are PCB boards becoming a newfound geopolitical topic?”
I’ve digressed, so let’s come back to the fair and its discussions. One recurring topic was the request for coupling solder mask printing with legend printing. It looks as simple and as good as chocolate and vanilla ice cream together. Just the idea of coupling these to reap twice the benefit is a no brainer. In the end, it’s inkjet printing anyway, so what could be so difficult about it?
During productronica, I cut short this thinking by mentioning the consequences of throughput, in part due to the theory of constraint.3 I will share some thoughts now but will follow up in a future column.
Indeed, both tools—a solder mask printer and a legend printer—use inkjet technology. It promises to have one tool that performs both coating with the same total average cycle time (TACT) as the original two tools. There are several approvals (pros) and disapproval (cons) to this approach. The pros, in general terms, are that one tool means one investment, potentially less labor, and potentially a lower footprint. In process terms, the advantage would be a single alignment operation for two processes. It’s as sweet and concise as chocolate and vanilla.
The cons come about when looking at the “nutritional facts,” or the math behind these good flavors. The single investment would reflect the complexity of having two systems with different requirements under the same hood. While the solder mask focus is precision and feature fidelity, the legend’s focus is readability and high contrast. The first is achieved with expensive hardware4 while the latter relies on special printheads that are compatible with a high load of dyes, pigments, and particles at the cost of higher drop volume and less precision. When the same printhead assembly must do both, that constrains the choice, resulting in either a high cost for a single, expensive, all-mighty printhead (array) or a double printhead array still at a higher price. The tool might still be less expensive than the sum of an inkjet tool for solder mask and one for legend, though it is a larger single investment that will have a larger effect on the financial books in a single year.
The labor needed for a single tool might be less; still, the operator needs to be highly alert, as the interruption of the all-capable tool will stop both solder mask and legend production; the oven will stay empty for a while. Even the production of solder-mask-only boards is on halt while the tool is down.
These are the other side of the medal for each initial pro, each company will have to assess how these affect them. My next column will continue describing other aspects, especially looking in more detail at TACT.
As a closing note, after having taken away the chocolate and vanilla ice, here are a couple funny events to lighten the mood:
The tool received most of the stickers on Monday, the day before the show. The last sticker, the “International No Pacemaker Prohibition Symbol” came on Tuesday morning, thanks to the effort of some of my colleagues at SUSS MicroTec in Garching, near Munich, just in time for the fair opening. This is a safety measure; the tool has magnets in its linear motors. Without such sticker, the tool would have been standing still, a bit of bummer after the whole preparation.
We had some fun playing rock-paper-scissors at every encounter when acknowledging a visitor at our booth. Now that the classic handshake (paper) is questionable, you might prefer a fist touch (rock). Still the other person might have the opposite idea. The phrase, “paper beats rock,” best described such a situation. Some people felt confident enough to always shake hands (paper), either thanking their third booster shot or thinking that the worst of the pandemic is over now. Personally, I am a rock person (fist touch). Nobody went for scissors; I wonder how that would have worked out.
Finally, on Friday, which some had named “student day,” many university students visited the show and witnessed the technologies. Three students came to our booth and asked what we were presenting. They got from me the inkjet litany, which was unexpectedly well received. I guess they enjoyed the fact that someone spent time providing them with information. However, their golden question, the one that will also conclude this column, was: “Why is this machine so special? Isn’t direct print of solder mask the way it is normally done?”
References
- “Exponential: How the Next Digital Revolution Will Rewire Life on Earth,” by Azeem Azhar, United Kingdom: Penguin Random House, 2021.
- FAANG refers to the stocks of Meta (Facebook), Amazon, Apple, Netflix, and Alphabet (Google).
- “The Goal: A Process of Ongoing Improvement,” by Eliyahu M. Goldratt and Jeff Cox, United Kingdom: Taylor & Francis, 2016.
- “Additive Reality: Drop Placement Accuracy,” by Luca Gautero, I-Connect007, June 20, 2021.
More Columns from Additive Reality
Additive Reality: Drop It, and Enjoy the GreenbackAdditive Reality: Let's Drop a Line About PCB Cross Section
Additive Reality: Drop-forging Solder Mask Thickness With Inkjet
Additive Reality: Isolated Raindrops Announce the Storm
Additive Reality: Green Drops, White Drops or Both: Do Solder Mask and Legend Make a Good Team?
Additive Reality: Your Company Drops Open the Inkjet Printer Box, Now What?
Additive Reality: Drop Your (Solder) Mask, It's Sampling Time
Additive Reality: Solder Mask Patterning at the Edge Between Drops and Bricks