-
- News
- Books
Featured Books
- pcb007 Magazine
Latest Issues
Current IssueInventing the Future with SEL
Two years after launching its state-of-the-art PCB facility, SEL shares lessons in vision, execution, and innovation, plus insights from industry icons and technology leaders shaping the future of PCB fabrication.
Sales: From Pitch to PO
From the first cold call to finally receiving that first purchase order, the July PCB007 Magazine breaks down some critical parts of the sales stack. To up your sales game, read on!
The Hole Truth: Via Integrity in an HDI World
From the drilled hole to registration across multiple sequential lamination cycles, to the quality of your copper plating, via reliability in an HDI world is becoming an ever-greater challenge. This month we look at “The Hole Truth,” from creating the “perfect” via to how you can assure via quality and reliability, the first time, every time.
- Articles
- Columns
- Links
- Media kit
||| MENU - pcb007 Magazine
Estimated reading time: 3 minutes
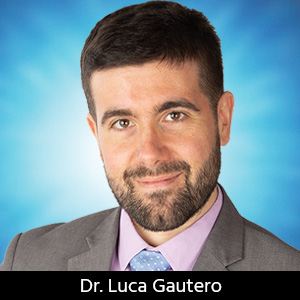
Additive Reality: Let's Drop a Line About PCB Cross Section
My article in the April 2022 issue of Design007 Magazine, titled “Additive Manufacturing Requires Additive Design Techniques,” presented several cross sections of solder mask coated with an inkjet technology. However, the choice of the cut’s location, and therefore the highlight of the picture, is slightly different from the usual dam or copper edge coverage. This illustrated my point and most structures of solder mask showed in the figures would not be anything new to my readers. Several articles have explained lateral definition and stacking principles.
Still, when the knowledge used as a starting point to examine these cross sections is from traditional solder mask (which mostly resembles rectangles), it is difficult to trust right away that any other shape will be as reliable.
The best way to highlight this difference is not necessarily with a cross section, but with a top view.
Figure 1: Comparison of traditional vs solder mask. The tapering of the solder mask thickness towards the edge of the pattern is especially visible on copper. (Source: ACB-Atlantec SAS)
Figure 1 shows one of the concepts explained in my March 2022 column titled, “Drop-forging Solder Mask Thickness With Inkjet.”
The usual questions refer to the solder mask adhesion to copper or laminate, its inertness to chemical attacks of post-treatments at high processing temperatures, and temperature stability during further manufacturing or product ageing.
The wetting behavior of the surface, controllable by the pre-treatment choice, has a wide process window1. The contact angle imposed by the wetting behavior, when combined with the low viscosity of the ink, fills any intricate roughness created by pre-treatments. This ensures the mechanical bonding of the anchor effect. Additional to the safety of this mechanical bonding is the inherent tapering of the solder mask thickness towards its edge. This ensures an increasing ratio between bonding and volume to bond. In other terms, the anchoring is always the same for any point where the solder mask is present, though the volume of solder mask anchored is less, which means that any mechanical action to remove solder mask will not find a convenient spot to leverage. The thickness tapering of the solder mask can raise doubts of chemical inertness with respect to typical chemistry of post-treatments or environmental stress during the lifetime of the PCB product (for example, skin sweat for a smartwatch). However, the solder mask material counteracts this stress by plain chemical inertness, not by means of thickness. Material suppliers ensure a negligible chemical interaction with coated solder mask. Therefore, any thickness, as long as it’s continuous, is enough. Just to make the point with absurd logic, if thickness were the protecting mechanism against chemical attack, when would it ever be thick enough?
Figure 2: Comparison of edge definition after ENIG post-treatment. (Source: ACB-Atlantec SAS)
A pragmatic proof of such adhesion is visible on ENIG-treated boards. The chemistry used to apply such metal finishing relies on aggressive substances at high bath temperatures. Inkjet solder mask, thanks to its profile and the properties defined before, ensures that its edge is the real ENIG edge. Traditional solder mask, due to negative foot situation, might not be able to grant the same precision of definition. It is not necessarily bad, but it is one point where process control isn’t as strong.
The holy grail of perfect definition with traditional solder mask technology is the “zero foot.” A fine-tuning of the coating process and its several steps will result in such a situation. Still, a lot can change during production. In the end, few micrometers of positive or negative foot will most likely not negatively affect the overall design, unless the board is an HDI type. However, a negative foot situation might especially facilitate the trapping of chemistry. Despite heavy rinsing, the sheer length of solder mask contour in a board increases trapping chances. This situation will lead to failures, since an active chemistry is left where it’s not supposed to be.
Inkjet follows the pattern definition to establish its edges. These are not positive feet; the edge is exactly where it should be. The coated pattern therefore benefits from improved edge adhesion, accurate definition and improved control on reliability.
References
Additive Reality columns by Luca Gautero: “Drops of Technology” (July 2021) “Printhead Selection or ‘Shop ‘Til You Drop’” (August 2021).
Luca Gautero is product manager at SUSS MicroTec (Netherlands) B.V.
More Columns from Additive Reality
Additive Reality: Drop It, and Enjoy the GreenbackAdditive Reality: Drop-forging Solder Mask Thickness With Inkjet
Additive Reality: Isolated Raindrops Announce the Storm
Additive Reality: Green Drops, White Drops or Both: Do Solder Mask and Legend Make a Good Team?
Additive Reality: A Report From 2021 (Drop)tronica
Additive Reality: Your Company Drops Open the Inkjet Printer Box, Now What?
Additive Reality: Drop Your (Solder) Mask, It's Sampling Time
Additive Reality: Solder Mask Patterning at the Edge Between Drops and Bricks