-
- News
- Books
Featured Books
- smt007 Magazine
Latest Issues
Current IssueSupply Chain Strategies
A successful brand is built on strong customer relationships—anchored by a well-orchestrated supply chain at its core. This month, we look at how managing your supply chain directly influences customer perception.
What's Your Sweet Spot?
Are you in a niche that’s growing or shrinking? Is it time to reassess and refocus? We spotlight companies thriving by redefining or reinforcing their niche. What are their insights?
Moving Forward With Confidence
In this issue, we focus on sales and quoting, workforce training, new IPC leadership in the U.S. and Canada, the effects of tariffs, CFX standards, and much more—all designed to provide perspective as you move through the cloud bank of today's shifting economic market.
- Articles
- Columns
- Links
- Media kit
||| MENU - smt007 Magazine
Estimated reading time: 5 minutes
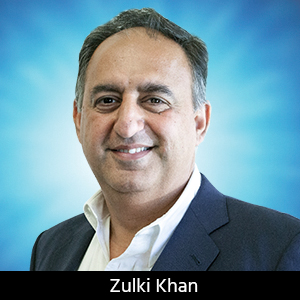
Zulki’s PCB Nuggets: Sub-Micron Die Bonding—Don’t Be Misled by Five Micron Placement Standard
OEMs launching micro-miniature products and relying on PCB microelectronics assembly and manufacturing to help produce those products may find themselves in a quandary.
Let’s think about this. The industry standard for accuracy right now for placement of MEMS devices, sensors, biosensors, or other kinds of pressure sensors is five-micron placement accuracy on a very small rigid or rigid-flex board. If you place a die on a tiny circuit board, it will be placed with plus or minus five-micron accuracy based on the majority of die bonding machines on today’s assembly and manufacturing floors.
But the thing about technology is that it doesn’t stand still; it is dynamic. That is highly applicable to these particularly miniature devices because they are continually shrinking in size to the point where five-micron accuracy may not be sufficient for state-of-the-art products such as small medical insertable, implantable, or wearable products. Or, for that matter, any other miniature OEM product.
In cases like these, you must use extremely high-end placement devices, which have less than a micron, or in other words, sub-micron placement capabilities because these devices are so sensitive. Pad sizes are so small. The wire bond attach angles are so tight that you need the wire bonds to be placed on adjacent bond pads with next to nothing tolerances available to play around when doing these placements.
It is critical for an EMS company or microelectronics service provider to have the capabilities to design, define, implement, and assemble sensor, biosensor, and MEMS device placement with sub-micron accuracy. Not only should they be able to do that with high accuracy, but, they should be able to quantitatively verify that accuracy. There are two aspects to it. One is the accuracy itself. The machines should be so sophisticated that they are able to place those fine dies, sensors, and MEMS devices with sub-micron accuracy.
But the second part, which is equally as important is to be able to quantitatively prove to customers and others that accuracy is there. For example, at NexLogic, as shown in Figure 1, we have a highly sophisticated digital microscope that accurately measures what is being placed, and it verifies the accuracy of the placement.
Figure 1: A highly sophisticated digital microscope that accurately measures what is being placed.
On top of those high-end camera systems and digital microscope, you should also have a backup methodology or technique to be able to verify placement accuracy and that backup or secondary source is X-ray. You should have an X-ray machine highly sophisticated enough to be able to recognize the images at sub-micron level and verify the voids. When placing the fine pitch devices like µBGAs or QFNs there are budget allowances allocated for IPC class one, two and three, when it comes to voids. Also an X-ray image can verify the robustness and accuracy of these wire bonds by critically reviewing these images, under high magnifications.
An X-ray has a certain budget for the voids to be allowed for BGA balls. And if it's class two assembly, typically the voids sizes in 25–30% are in acceptable range. More than that, it pushes that product into unacceptable limits. So not only should an assembly house with microelectronics capability be able to place those components with extreme accuracy at sub-micro level, it should also be able to accurately and quantitatively verify them by showing the measurement in microns.
If your miniature products call for extremely tiny dies and devices, the only way accurate board placement is possible is with a sophisticated sub-micron die bonding system. However, if your PCB microelectronics assembly and manufacturing house remains with the standard five-micron placement standard, then there are certain products that cannot be effectively assembled.
Number one, a standard five-micron accuracy die bonder will not properly place a new state-of-the-art die, simply because it’s not completely capable of performing such minute and accurate placements. Number two, if you “brute force” your way into performing placement at the five-micron level when accuracy requirements are one to two microns, and in some cases, sub-micron, die placements will not be optimal. This means die attach will not be properly performed, which results in a marginal product when it is assembled. Worst-case, it can either fail in the field or in the lab during testing, as the best-case scenario.
What’s Required for Sub-Micron Die Bonding
Two new technologies are the underpinnings of sub-micron die bonding. One is fixed beam splitter; the other is thermocompression. Fixed beam splitter, also known as diffractive beam splitter, as the name implies, takes one beam of light and splits it into two.
So, rather than having one point of reference for performing a function, you have two different perspectives. In effect, those split beams of light create greater die placement accuracy. During the wire bonding operation, the sub-micron die bonder triggers the split beams of light. One looks at the die from the top side, the other from the bottom side to assure a highly accurate wire bonding.
Thermocompression, on the other hand, is a function of time, force, and temperature. These are the key factors involved in sub-micron die bonding when a die is attached using wire bonding. In cases like these, die balls have a pitch or distance between balls of five mils or less.
Conversely, traditional BGA ball pitch is between 300 to 400 microns or 10 to 15 mils of ball pitch. Wire bonding is relatively easy using the traditional reflow methodology, which is well-proven, reliable, and time tested since it’s been used for decades.
However, reflow is extremely limited for fine pitch applications. In effect, there is no force to attach the die. As a result, the very tiny die doesn’t align automatically and moves in the center due to surface tension. Also, since these are fine pitch devices, there is a high probability they get shorted to the pad, if proper assembly techniques are not followed.
So, as our industry moves more into micro-miniature PCBs and microelectronics assembly and manufacturing, the prudent OEM will take a closer look at the key elements of sub-micron die bonding. Currently, it’s highly important to gain a better understanding of the consequences incurred by naively taking the five-micron placement route instead of the sub-micron die bonding one.
Zulki Khan is the president and founder of NexLogic Technologies Inc.
More Columns from Zulki's PCB Nuggets
Zulki's PCB Nuggets: Cleanliness is Next to ReliabilityZulki’s PCB Nuggets: Thermal Compression Bonding for Extra Fine Pitch Flip Chips
Zulki’s PCB Nuggets: WBAN Steps Into PCB Microelectronics Assembly
Zulki’s PCB Nuggets: Photonics Comes to PCB Microelectronics Assembly
Zulki’s PCB Nuggets: Meet the New Player in PCB Microelectronics Assembly—Interposers
Zulki’s PCB Nuggets: How Effective Is Your PCB Microelectronics Assembly?
Zulki’s PCB Nuggets: Five Key Benefits for Onshoring PCB Microelectronics Assembly
Zulki's PCB Nuggets: Onshoring for PCB Microelectronics Production?