-
- News
- Books
Featured Books
- design007 Magazine
Latest Issues
Current IssueProper Floor Planning
Floor planning decisions can make or break performance, manufacturability, and timelines. This month’s contributors weigh in with their best practices for proper floor planning and specific strategies to get it right.
Showing Some Constraint
A strong design constraint strategy carefully balances a wide range of electrical and manufacturing trade-offs. This month, we explore the key requirements, common challenges, and best practices behind building an effective constraint strategy.
All About That Route
Most designers favor manual routing, but today's interactive autorouters may be changing designers' minds by allowing users more direct control. In this issue, our expert contributors discuss a variety of manual and autorouting strategies.
- Articles
- Columns
- Links
- Media kit
||| MENU - design007 Magazine
Estimated reading time: 6 minutes
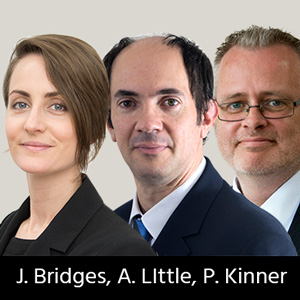
Sensible Design: How to Increase the Reliability of Conformal Coatings
For this month’s column, I’m going to examine the main methods for achieving the best outcome for your conformal coating process, ultimately increasing the protection afforded by your coating and lifetime of your product.
Let’s start at the very beginning, at the design stage, factoring in careful consideration for coatings and highlighting the potential for problems during production. This will have a positive impact in the long term and avoid excessive time and expense, resolving problems at a later stage. Another important factor for successful coating is selecting the right coating for the job. This could be an acrylic, a polyurethane, a silicone, a UV cure, a two-part (2K) system, or even a water-based coating. Whilst the design of the board doesn’t directly affect the choice of coating material, it will determine which methods can be used to apply the coating. Certain materials, such as moisture curing, 2K or UV curable materials, are difficult to use in a dip process due to the material curing prematurely, so it could be said that the choice of coating is indirectly related to the board design. Similarly, board design will affect the production yield. Consider maximising the distance between components that must be coated and those that must not. The greater the distance between them, the more the production staff will thank you. As a rule, 2 mm is the absolute minimum clearance between coat/no-coat areas, but 5 mm will make an enormous difference in the coating cycle time and success.
Factors such as operating temperature range, temperature excursions (such as thermal shock and thermal cycling), corrosion, condensation, and resistance to chemicals, solvents, and water are all key in determining the successful outcome for a coating.
How Important is Coating Application?
Do not underestimate this element. Probably the single biggest influence on coating success is as a direct result of how well the coating is applied. The application method of a conformal coating is as important, if not more important, than the selection of the right material. I can’t stress this enough, because even the best coating, when applied poorly, may not provide the level of protection required or that it is capable of. Significant elements to consider include the thickness the coating is applied, the level of coverage achieved and how well the coating adheres to the board and its components. It is imperative to choose the best method for applying the coating.
There are numerous methods to apply coatings, which include hand applications such as brush, aerosol and atomised spray, and machine applications such as dip and selective coating. When applied correctly they form a thin film that conforms to the contours of the PCB and its components, as well as the exposed metal of component leads and solder joints. Typically, conformal coatings are applied in the 25–250-micron range.
The application method chosen for a particular assembly will depend upon which existing equipment is available to the manufacturer, the coating processes in use, the takt time (the average time interval between the start of production of one unit and the start of the next), and the design of the assembly. This includes those areas of the circuit, which must be coated and those which must not, connectors, switches and so forth. In addition, it is incredibly helpful to define don’t care areas, which may or may not be coated. The best application method will ensure that each board coated receives good coverage on all required metal surfaces at a sufficient thickness to afford protection against the environment. These requirements will change from board design to board design, and environment to environment, and invariably they need to be tested and verified ahead of the production run.
Coating Thickness
Achieving the correct coating thickness is essential; bear in mind that if the coating is too thick it can lead to entrapment of solvents which can result in blow-out bubbles, delamination, or lack of adhesion. Similarly, it can cause the coating to crack as it cures or as the result of changes in temperature, or due to mechanical shock and vibration. Conformal coatings should not be applied at thicknesses greater than necessary and should never exceed the maximum thickness they were designed to be applied at.
Is it Necessary to Clean Prior to Coating?
The potential presence of residues on the substrate can have a critical impact on coating performance. If the substrate is not clean, the residues present may interfere with the curing mechanism, lead to poor adhesion of the coating to the substrate, and/or trap conductive/ionic materials under the coating. Without meticulous attention to preparation or pre-coat cleaning regimes, corrosive residues bridging the PCB’s conducting tracks can cause failures over time. It is important to test the reliability of no-clean flux residues from your assembly process with your coating process, to ensure compatibility and adequate performance in your design.
What Will the PCB Board Layout Be?
The design of the board should include consideration of the placement of components that should not be coated. Selective spray equipment or the application of a peelable coating mask can be used to help avoid such areas. Alternatively, gel materials can be used to form a “dam” to contain the coating and avoid capillary effects transferring material to unwanted areas, such as connectors. Another aspect to consider is how close together the components are. If there is not a sufficient gap between the components, it can lead to the coating bridging the gap rather than correctly conforming to the board. This can have several effects including the coating building up to become too thick and crack, or it can leave pockets under the coating where solvent can gather and cause corrosion.
By placing connectors and components that must not be coated along one edge of the assembly, the conformal coating application process will be simplified. It is also advisable to avoid large arrays of discrete components, which can pose a huge coating challenge due to the high levels of capillary forces present. Tall components can also present challenges of their own by the creation of shadowed or hard to reach areas. Splashing is another associated problem. The trick is to avoid placing tall components next to “must-coat” components to avoid this eventuality.
Know Your Component Zones
Lastly, it’s worth noting that being aware of what kinds of components should be coated or should not be coated will provide more flexibility to the coater in assembly operations. When a component will not be coated, it becomes a “keep out” zone. The engineering drawing should not only identify components but identify the tolerance on that keep out zone. It is important to be very specific on the tolerance. The manufacturer needs to know exactly where you do and don’t want coatings. It is best practice to specify the areas that need to be coated and the areas that don’t, as well as the “don’t care” areas, to help the coating process run as smoothly as possible. Avoid vague statements at all costs in an engineering drawing. This is especially true when specifying coating around connectors.
Over the following months I hope to provide more useful tips and design advice that will help make life a bit easier for those who are responsible for making the decisions on protecting components and circuitry. I hope the foregoing will help you with your coating process. Look out for my next column where I will be exploring more coating tips and techniques.
This column originally appeared in the September 2021 issue of Design007 Magazine.
More Columns from Sensible Design
Sensible Design: Automotive Conformal Coating ApplicationsSensible Design: Green Coats Are In
Sensible Design: Encapsulation Resins—PU vs. Epoxy
Sensible Design: Avoiding Conformal Coating Pitfalls
Sensible Design: Comparing Traditional and Bio-based Resins
Sensible Design: All Resins Are Not Created Equal
Sensible Design: Can Solvent-free UV-cure Coatings Increase Stability and Throughput?
Sensible Design: Optimize Your Thermal Management