-
- News
- Books
Featured Books
- pcb007 Magazine
Latest Issues
Current IssueInventing the Future with SEL
Two years after launching its state-of-the-art PCB facility, SEL shares lessons in vision, execution, and innovation, plus insights from industry icons and technology leaders shaping the future of PCB fabrication.
Sales: From Pitch to PO
From the first cold call to finally receiving that first purchase order, the July PCB007 Magazine breaks down some critical parts of the sales stack. To up your sales game, read on!
The Hole Truth: Via Integrity in an HDI World
From the drilled hole to registration across multiple sequential lamination cycles, to the quality of your copper plating, via reliability in an HDI world is becoming an ever-greater challenge. This month we look at “The Hole Truth,” from creating the “perfect” via to how you can assure via quality and reliability, the first time, every time.
- Articles
- Columns
- Links
- Media kit
||| MENU - pcb007 Magazine
Estimated reading time: 7 minutes
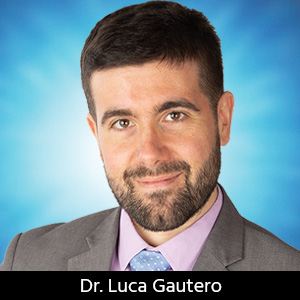
Additive Reality: Solder Mask Patterning at the Edge Between Drops and Bricks
The digital form of inkjet printing technology operates on files containing a rasterized image; these bitmaps, in their simplest form, contain information about the presence (or absence) of drops. Additionally, the resolution brings in the drop’s pitch. This represents a 2D view of a pattern. Such a pattern might, once printed, have a thickness, however, the rasterized image does not carry this information. For pure 3D printing, the solution is to assign a fixed height step to each printed layer. Elegant and simple: each drop approximates a brick of fixed length, width, and height. This works reasonably well when the approximated drop dimensions are far below the tolerance needed for the application.
For solder mask requirements, however, this is not the case. Features in PCB designs span several orders of magnitude with their length and width. The smallest feature is only one, two, or three times the size of a drop depending on the hardware choice (see my August column “Printhead Selection or ‘Shop ‘Til You Drop’”). As a bridge between the bitmap definition and the final pattern, it is useful to define the outflow length of a drop (Lof). This length is the difference between the bitmap pattern length and the final length of the printed and cured feature.
Figure 1: Visual interpretation of the outflow length.
In Figure 1, a visual definition helps to correctly assess the role of Lof. Furthermore, it highlights the impact of such length on small size features by visually comparing a single pixel feature with a larger feature.
Since the digitally defined bitmap provides control of the pattern, adding a reproducible Lof extends the reproducibility all the way to the printed image. The proper place to implement this extension is between the vector format CAM definition of the pattern and the subsequent generation of the rasterized image. At this moment, geometrical features defined by coordinates become bitmaps. The Lof length becomes the resizing length for features that need to be printed. Similar intervention on vector formats are already common to compensate under-etch or over-etch during wet processing for etching.
From previous columns, it is now clear that a printing strategy can independently adopt a printing resolution and a drop size. On the one hand, the resolution is a printer parameter and its inverse, L1 pix, represents the length of a pixel; on the other hand, both ink physical properties and the surface define the drop size. This makes the drop size a slightly more indirect process parameter. In between these two independent parameters lies Lof
2Lof = Ddrop - L1 pix
Where Ddrop is the diameter of a single drop. With this definition, Lof depends on the chosen physical properties of the drop and the selected resolution.
Figure 2: Comparison of different resolution "R" and "2R" on the discretization of feature size.
When the resolution approaches infinity, any feature bigger than two times Lof is feasible. Then again, at a low resolution, where its inverse, L1 pix, is almost as big as Ddrop,will lead to a small Lof and a discretization of the feature sizes. As seen in Figure 2, when feature sizes are small (near the single drop limit) a larger resolution will not allow creation of a continuum of feature sizes. The minimum gap between printable feature sizes is L1 pix. This is why high resolution for a solder mask applications is preferred.
A clear understanding Lof and its reproducibility is indeed key to the success of patterning. Few equipment suppliers use concepts that are even more refined than the single Lof . In an attempt to simplify the user experience, they present a front-end interface directly at the CAM station. This approach is very similar to the everyday office experience, where the text that is on the screen appears identical on paper when printed. Much of what happens in the background goes behind the concept of “what you see is what you get” or WYSIWYG.
The keen-eyed reader may have spotted that the overlapping drops do not create a justifiable height in the sketches presented so far. This serves as an easy explanation of the Lof concept. In the following paragraph the attention will shift to height building. This will bring into view the bricks of solder mask inkjet printing.
The promise of inkjet solder mask is to deliver complete control over the thickness, not only as a single parameter for the whole board, but also as a topographical design choice. Inkjet allows the addition of a dimension (height) for each point of the pattern.
The simplest interpretation is a layer stackup. When a pattern is created and printed, the resolution and the drop size are enough to calculate the thickness of a single layer. Printing such a layer twice would double the thickness. When the resolution is high enough to allow large drop overlap, another tool, dithering, allows tune thickness. Dithering removes, at regular intervals, black pixels from the image at a defined percentage rate. Since drops are large enough to touch each other even when some are missing, a thinner, continuous layer will form. The dithering parameter drives the final thickness.
The solution presented by the previous paragraph is valid for large features, several times the size of a drop. As we have seen before, when the feature size compares to a single drop, their size and thickness control becomes more challenging. The refined concept of the front-ends offered by the tool supplier tackle such challenges. These concepts might not be public knowledge, so the best approach is to challenge the equipment supplier directly with the right questions or even better, ask for a sample, and verify if the experience is close to a WYSIWYG.
Previous columns (July 2021 and August 2021) have detailed the typical shape of a single drop; its cross section resembles a dome with a certain contact angle. This shape is characteristic of inkjet printing and presents at any printed edge. Thickness, and especially the number of layers used to build it, influences the resulting contact angle. A favorable aspect ratio (height divided by width) for inkjet printing features ranges from 0.15 to 0.3. Lower aspect ratios are undesirable since these will lead to very thin patterns, thinner than commonly used copper thicknesses. It will still be possible to create features, though building up thickness will take a great number of layers. Engineering higher aspect ratio requires a tight control on the surface pre-treatment and solidification mechanism. It is not impossible, though it is not a robust choice since the successful process window will be small. When looking at the shear amount of surface that needs processing every day in a manufacturing line, this can be a risky bet.
The bricks of inkjet printing, near the size of the drop, will never have sharp edges. This is indeed a change from the incumbent technology, where sharper edges are the norm. Still, such edgy build up is not strictly necessary, and sometimes can even lead to failure modes, such as chemistry trapping. A dome shape might have mechanical preference when adhesion is critical by inherently offering a less firm point of anchoring. One example is the easy removal of wet chemistry for post-treatments. Entrapped residual chemistry is often the cause of failure during the lifetime of the board. The dome shape solves this issue.
The one question not addressed yet is how many bricks can be stacked? How thick can inkjet printing go and where is the advantage? Strictly speaking, there is no limit to the number of layers stacked. However, there are two prices to this: time to print and minimum feature size. Since the commercial inkjet equipment for solder mask available at this moment have similar throughput, the common “build up speed” is approximately 2µm/s. Further process fine-tuning and compromises can increase this number. About the minimum feature size, the printing strategy that accounts for the outflow length and the given aspect ratio of the stacked layers provides information on its minimum size capabilities. The equipment supplier can assist in distinguishing between reasonable expectations and purely impossible patterns. The starting point will always be the baseline printing strategy. This strategy covers mainstream PCB design needs and has the benefit of months, if not years, of tests and verifications. A branch from the baseline for specific purposes is possible as long as there is space for compromises in other aspects, such as throughput. Finally, when both the thickness and lateral dimensions will exceed by far the size of the drop, the stacking will resemble again the now commonly available 3D printing. Therefore, the fine concepts presented here will play less of a role.
Luca Gautero is product manager at SUSS MicroTec (Netherlands) B.V.
More Columns from Additive Reality
Additive Reality: Drop It, and Enjoy the GreenbackAdditive Reality: Let's Drop a Line About PCB Cross Section
Additive Reality: Drop-forging Solder Mask Thickness With Inkjet
Additive Reality: Isolated Raindrops Announce the Storm
Additive Reality: Green Drops, White Drops or Both: Do Solder Mask and Legend Make a Good Team?
Additive Reality: A Report From 2021 (Drop)tronica
Additive Reality: Your Company Drops Open the Inkjet Printer Box, Now What?
Additive Reality: Drop Your (Solder) Mask, It's Sampling Time