-
- News
- Books
Featured Books
- design007 Magazine
Latest Issues
Current IssueProper Floor Planning
Floor planning decisions can make or break performance, manufacturability, and timelines. This month’s contributors weigh in with their best practices for proper floor planning and specific strategies to get it right.
Showing Some Constraint
A strong design constraint strategy carefully balances a wide range of electrical and manufacturing trade-offs. This month, we explore the key requirements, common challenges, and best practices behind building an effective constraint strategy.
All About That Route
Most designers favor manual routing, but today's interactive autorouters may be changing designers' minds by allowing users more direct control. In this issue, our expert contributors discuss a variety of manual and autorouting strategies.
- Articles
- Columns
- Links
- Media kit
||| MENU - design007 Magazine
Estimated reading time: 4 minutes
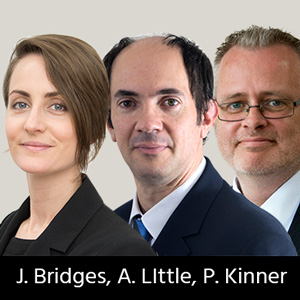
Sensible Design: Are Encapsulation Resins Suitable for EV Applications?
In this month’s column, I will be exploring how resin chemistries can be incorporated by design engineers facing ever increasing new challenges from e-mobility applications—for instance, motors and generators offering higher levels of power output, noise reduction, and reliability. One of the biggest areas of concern for designers is the issue of heat impact on battery performance, particularly as drivers crossing over from traditional fuel vehicles to electric will expect no compromise in performance from their new electric/hybrid vehicle. Let’s take a closer look at how resin systems can be implemented to improve performance, safety, reliability, and ultimately, lifetime.
Key Benefits of Using Resins in EV Applications
Protecting the electronics is vital to ensuring long-term performance and reliability. Encapsulation resins benefit e-vehicles in numerous ways, including improving thermal conductivity to dissipate heat away from hot spots, improved thermal endurance and stability in chemicals, and fast gap filling to provide resistance towards crack propagation. Encapsulation resins can also prevent costly maintenance and repair.
Why Encapsulate Electric Motors?
Historically, varnishing of the rotor and stator windings was common to achieve a minimum level of insulation; such varnishes were solvent-based and contained a high percentage of volatile organic compounds (VOCs). However, with increasing environmental awareness, legislation restricts the use of VOCs due to their emissions into the environment. Such varnishes do not fulfil the higher requirements of e-motors in the automotive industry where the challenges are higher power density caused by size reduction, increased power output, reliability, and endurance in harsh environments. This means there are now even more reasons to use encapsulation resins and they deliver plenty of value-added benefits:
- All-around protection: Acting as a barrier to the external environment, encapsulation resins provide physical, chemical, and thermal protection. They can physically dampen the impact of shock vibrations or dampen noise produced by the motor. Some encapsulation resins also benefit from flame retardant properties.
- Electrical insulation: Air and voids can create partial discharges between ground and primary insulation. Encapsulation resins can be used to completely fill all internal spaces, often helped by vacuum-potting methods to fill all the tiny spaces to guarantee electrical insulation.
- Thermal dissipation: Some encapsulation resins have high thermal conductivity and are extremely effective at dissipating heat away from hot spots and improve the overall thermal endurance.
- Noise, vibration, and harshness (NVH): Although e-motors are quieter than traditional internal combustion engines, and have fewer moving parts, electric vehicles create higher frequency noise that can be annoying over a long period of time. Resins are used to handle the NVH and add perceived value for any vehicle owner.
What Types of Resin Solutions Are Available?
Unlike aerospace applications, where two or three layers of redundancy may be built into systems, automotive designs typically must work the first time, every time, throughout the life of the product. There are a variety of expansive resin solutions that improve performance and reliability. By way of example, resin solutions for EV applications would include black epoxy resin, which is frequently chosen as the resin material to electrically insulate the coil ends of stator windings found in electric vehicles. This resin is highly resistant toward immersion in chemicals found in electric and hybrid vehicles, including cooling fluids, and has extremely wide operating temperature ranges. Its low viscosity also allows for easy potting of all the tiny spaces between the winding coils.
EV batteries produce vast amounts of heat during operation and whilst charging. To achieve prolonged battery life and higher efficiency, a potting material with a highly thermally conductive resin with low viscosity is ideally suited for potting cells within electric vehicle batteries. It also assists with securing cells in place whilst dissipating the heat away to the surroundings. The resin effectively creates a protective shield around the battery, enables adhesion, high temperature resistance, high thermal conductivity, and retention of characteristics throughout the thermal cycling process.
Are Changing Customer Requirements in Line?
There is clearly a change in customer requirements in line with the trend for EVs, such as improved range, faster charging times, and wider availability of charging stations. With each new iteration, a next generation of design typically means components get smaller in size and their power output increases. This normally means that the heat generated from higher density power output components increases. In turn, both short- and long-term operating temperatures of resins need to increase to perform sufficiently. Since resins are used in many areas on a vehicle, from sensors and displays to the motors themselves, a lot of development by Electrolube is focused on pushing the limits of thermal performance and thermal conductivity to remain as the solutions provider of choice for the ever-changing automotive industry.
E-mobility is an evolving market, where the various performance criteria for vehicle components is constantly changing to keep up with the latest developments in technology. Encapsulation resins capable of dissipating heat away from hard working components clearly add value to the automotive electronics industry. I hope this has been of interest to those of you involved in EVs and helps make life a bit easier for those who are responsible for making the decisions on protecting components and circuitry. In my next column I will be exploring resin systems in more detail.
This column originally appeared in the October 2021 issue of Design007 Magazine.
More Columns from Sensible Design
Sensible Design: Automotive Conformal Coating ApplicationsSensible Design: Green Coats Are In
Sensible Design: Encapsulation Resins—PU vs. Epoxy
Sensible Design: Avoiding Conformal Coating Pitfalls
Sensible Design: Comparing Traditional and Bio-based Resins
Sensible Design: All Resins Are Not Created Equal
Sensible Design: Can Solvent-free UV-cure Coatings Increase Stability and Throughput?
Sensible Design: Optimize Your Thermal Management