-
- News
- Books
Featured Books
- smt007 Magazine
Latest Issues
Current IssueSupply Chain Strategies
A successful brand is built on strong customer relationships—anchored by a well-orchestrated supply chain at its core. This month, we look at how managing your supply chain directly influences customer perception.
What's Your Sweet Spot?
Are you in a niche that’s growing or shrinking? Is it time to reassess and refocus? We spotlight companies thriving by redefining or reinforcing their niche. What are their insights?
Moving Forward With Confidence
In this issue, we focus on sales and quoting, workforce training, new IPC leadership in the U.S. and Canada, the effects of tariffs, CFX standards, and much more—all designed to provide perspective as you move through the cloud bank of today's shifting economic market.
- Articles
- Columns
- Links
- Media kit
||| MENU - smt007 Magazine
Estimated reading time: 4 minutes
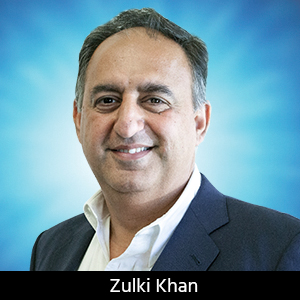
Zulki’s PCB Nuggets: Thermal Compression Bonding for Extra Fine Pitch Flip Chips
Medical OEMs and others moving toward developing and producing small, portable products may want to investigate the emerging technology of thermal compression bonding or TCB. TCB is ideally suited for miniature products that use fine pitch flip chip devices undergoing PCB microelectronics assembly.
Certainly today, regular pitch flip chips can be bonded using die attach and wire bonding. However, there is another way for bonding miniature designs that call for fine pitch flip chips. In this case, fine pitch pad size is defined as 50 to 75 microns. If that is so for your application, then it’s worth looking into thermal compression bonding.
Overview
Three factors are involved in thermal compression bonding—time, temperature, and force. This process is relatively quick-and-easy and is time tested.
There are certain advantages to flip chip bonding using thermal compression methodology, which is a diffusion process. Performing TCB on one machine or station is one of its top advantages, contrasted to a typical SMT reflow, where you have to take the PCB from pick-and-place to the reflow oven, thereby moving the product from one machine to another.
Whether that movement is a few inches, a few feet, or maybe across the hall, physical movement of the boards any distance can possibly jeopardize placement accuracy. With TCB, you basically use one machine, one station. That means placement accuracy will not be challenged since you are eliminating travel distance from one machine to another.
Moreover, TCB has excellent connection properties which improve solder joints, especially if you are talking about RF based applications that demand extremely accurate connections with low signal-to-noise ratios (SNR).
TCB can also be used for proof-of-concept application because it can be developed with relative ease by experienced process engineers, using the factors of force, time, and temperature. Moreover, for TCB, wire diameter is important, which is in the range of typically 25-micron.
Seasoned process engineers working with TCB review an application to define and improve process parameters. They then define and design the temperature range the process requires for the bonding. At the same time, they define and design the level of force that needs to be applied and the necessary time needed to maintain that temperature for a perfect bond.
Disadvantages
TCB has challenges and disadvantages, as well. This type of bonding requires high placement accuracy, meaning two to three microns. Moreover, it needs to have some flexibility and wiggle room that allow process engineers to define placement accuracy according to the machine being used for TCB process. 1-2 micron wiggle room is plenty to work with, if you have a sub-micron placement capabilities
Further, according to die size, which is being flip chip bonded, there is a disadvantage due to the high placement accuracy required. If you are using a large size die, then certain machines would not be able to perform TCB because of field-of-view (FOV) limitations. A limited field of view is a direct consequence to that high placement accuracy. If placement is extremely accurate, then you cannot flip chip a bigger size die, let’s say more than half an inch in size with a typical TCB machine.
Another disadvantage is high equipment cost. Not only does TCB require a machine that has top and bottom heaters for heating from both sides, but it also needs a very high accurate placement tolerance, which doesn't come easy without spending a lot of money. Extra cost is associated with such other items as tools and fixtures, which could differ from project to project.
Also, one has to keep in mind that a conventional substrate like FR-4 must stay below certain temperatures. The extra costs here go toward using a non-organic substrate, like alumina or aluminum nitrate. Such a substrate provides better results because it is considerably more co-planar and can handle higher temperature levels.
Specifics: Time, Temperature and Force
Typical time is from 30 to 60 seconds at 275–300°C for the TCB to be accurately performed. Keep in mind that the amount of time required to bond using the TCB process depends on ball size of a flip chip device, size of the die, as well as its thickness.
Temperature
TCB requires a high temperature such as 300°C. In this case you need a heating tool for device placement and a sophisticated automatic bonder for performing the thermal compression bonding. For TCB to be properly performed, heating comes from two sides, from the top to the bottom of the bonding machine. The higher temperature is more from the top side than bottom side. Typically, from the top side of the machine it is 250–300°C and on the bottom side, 90°C to about 150°C. But, again, it must have the heating temperature from both sides.
Force
As for bond force, the lowest you can go is 0.05 Newton, and the highest is typically 1,000 Newton. The force range is going to be defined by the die size. The bigger the die size, the bigger the bond force that will be required. Bond force holds the die on top of the substrate. The required load force is dependent on die size. Also, during this TCB process, melting of device package balls requires a small period of time, 30 to 60 seconds. But the process engineer needs to make calculations for intricate details and adjust parameters for that.
Verify
Lastly, like any other process, you need to verify the bonding performed by three different methodologies. Those are visual, X-ray, and shear pull test verification inspections. And when you're doing that, then you have to assure that you are performing the pull test as per the parameters defined by the customer or the process application.
In summary, TCB may be a niche for the near term. However, with the increasing interest in smaller, miniature medical products, the likelihood is greater that TCB becomes more prominent in PCB microelectronics assembly. So, it’s a good tool for EMS provides to have in their arsenals.
Zulki Khan is the president and founder of NexLogic Technologies Inc.
More Columns from Zulki's PCB Nuggets
Zulki's PCB Nuggets: Cleanliness is Next to ReliabilityZulki’s PCB Nuggets: WBAN Steps Into PCB Microelectronics Assembly
Zulki’s PCB Nuggets: Photonics Comes to PCB Microelectronics Assembly
Zulki’s PCB Nuggets: Sub-Micron Die Bonding—Don’t Be Misled by Five Micron Placement Standard
Zulki’s PCB Nuggets: Meet the New Player in PCB Microelectronics Assembly—Interposers
Zulki’s PCB Nuggets: How Effective Is Your PCB Microelectronics Assembly?
Zulki’s PCB Nuggets: Five Key Benefits for Onshoring PCB Microelectronics Assembly
Zulki's PCB Nuggets: Onshoring for PCB Microelectronics Production?