-
- News
- Books
Featured Books
- design007 Magazine
Latest Issues
Current IssueProper Floor Planning
Floor planning decisions can make or break performance, manufacturability, and timelines. This month’s contributors weigh in with their best practices for proper floor planning and specific strategies to get it right.
Showing Some Constraint
A strong design constraint strategy carefully balances a wide range of electrical and manufacturing trade-offs. This month, we explore the key requirements, common challenges, and best practices behind building an effective constraint strategy.
All About That Route
Most designers favor manual routing, but today's interactive autorouters may be changing designers' minds by allowing users more direct control. In this issue, our expert contributors discuss a variety of manual and autorouting strategies.
- Articles
- Columns
- Links
- Media kit
||| MENU - design007 Magazine
Estimated reading time: 3 minutes
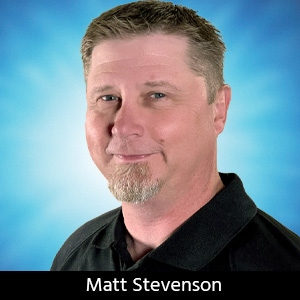
Connect the Dots: Diving Into the Chemical Processes of PCB Manufacturing
I have always been fascinated with chemistry and chemical processes. My first degree was in chemistry and my first job out of college was in the PCB manufacturing shop in the analytical chemistry lab. During my initial tour I was so surprised with just how many chemical processes there were in PCB manufacturing. I discovered that some of the most critical elements of PCB manufacturing involve chemical processes.
Chemicals clean the copper in preparation for the coating that prevents oxidation, and again to remove contaminants before solder resist application. The etching itself uses chemicals to remove excess copper. Chemicals are also used to electroplate metals such as copper, nickel, gold, and tin. In addition, there are many electroless and immersion plating chemicals that are used to protect exposed copper ahead of the soldering process.
Keeping all these chemical baths, sprays, rinses, and processes operating in a tight operating window to maintain quality and predictable results is a key component in PCB manufacturing.
Best Practices for Chemical Process Control
There are enough methods available to test and analyze chemical processes in a factory to make your head spin. Here is a short primer on the most common, effective methods of testing chemical processes:
Titrations
There are quite a few chemical components that can be measured in a working chemical bath by a titration. Titration is the process of adding one chemical of a known concentration to a small sample of the bath until a target pH is obtained.
There are several ways to catch this pH endpoint. Indicators can change color at a given endpoint. You can track pH with a meter during titration. Some reactions will provide answers by creating a precipitate (a solid) at the desired pH. If you know precisely how much chemical has been added, a simple calculation will tell you the concentration of the component in the bath.
Colorimetric Tests
Another common testing method uses ultraviolet-visible (UV-Vis) spectrophotometry. We use a UV-Vis spectrophotometer to analyze a sample of a bath at a given wavelength of light. As we do, the absorption or transmittance of the light as it passes through the sample will give a reading. When this reading is applied to a calibrated curve of known concentrations, it can provide the bath concentration.
Elemental Analysis
Elemental analysis is a sound method for finding concentrations of various types of metals in a chemical sample. Common elements found in PCB manufacturing include copper, gold, nickel, silver, tin, and lead. One of the most accurate ways to detect metal is through flame atomic absorption analysis (FAAS). Using this method, a sample of the chemical bath is burned in an atomic absorption flame, and it measures the absorption of light at specific wavelengths to detect gas phase elements. This absorption value is compared to a standard curve of known concentrations to determine the composition of the solution.
Functional Tests
Functional testing is a type of black box testing that bases its test cases on the specifications of the component being tested. These tests are especially useful in electroplating because they can help you understand how some components are functioning. One example of a functional test is a grain refiner in a copper bath tested using a special bench top unit called a Hull cell. A sample of the plating bath is added to a Hull cell, along with an anode and a brass plating coupon. Next, current is applied. This causes an electroplating reaction to occur, and a metallic deposit will accumulate on the brass Hull cell coupon. Allowing the Hull cell to sit for a period will ensure that there is adequate metallic deposit to analyze.
This type of test can cover a variety of plating current densities. You can also add standard additions of grain refiner to the plating cell and compare it to the plating bath. This will help you to understand appropriate additives that will achieve the desired copper deposit.
All these tests and the results they produce will help you to maintain the chemical processes within their given operating ranges. You will also be better able to quickly identify problems with equipment or chemistry to ensure that an expected outcome is the result of every chemical process.
This column originally appeared in the November 2021 issue of Design007 Magazine.
More Columns from Connect the Dots
Connect the Dots: How to Avoid Five Common Causes of Board FailureConnect the Dots: Sequential Lamination in HDI PCB Manufacturing
Connect the Dots: The Future of PCB Design and Manufacturing
Connect the Dots: Proactive Controlled Impedance
Connect the Dots: Involving Manufacturers Earlier Prevents Downstream Issues
Connect the Dots: Stop Killing Your Yield—The Hidden Cost of Design Oversights
Connect the Dots: Designing for Reality—Routing, Final Fab, and QC
Connect the Dots: Designing for Reality—Surface Finish