-
- News
- Books
Featured Books
- design007 Magazine
Latest Issues
Current IssueAll About That Route
Most designers favor manual routing, but today's interactive autorouters may be changing designers' minds by allowing users more direct control. In this issue, our expert contributors discuss a variety of manual and autorouting strategies.
Creating the Ideal Data Package
Why is it so difficult to create the ideal data package? Many of these simple errors can be alleviated by paying attention to detail—and knowing what issues to look out for. So, this month, our experts weigh in on the best practices for creating the ideal design data package for your design.
Designing Through the Noise
Our experts discuss the constantly evolving world of RF design, including the many tradeoffs, material considerations, and design tips and techniques that designers and design engineers need to know to succeed in this high-frequency realm.
- Articles
- Columns
- Links
- Media kit
||| MENU - design007 Magazine
Alex Stepinski: A Philosophical View
November 30, 2021 | I-Connect007 Editorial TeamEstimated reading time: 3 minutes
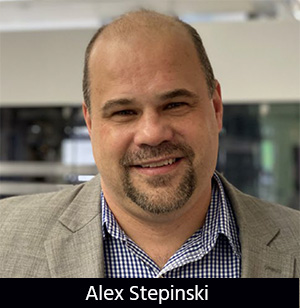
Alex Stepinski gives his thoughts on how test and inspection should be linked and reflects on how the process controls in fabrication are likely to change in the future.
Barry Matties: Alex, as you know, there are two levels of test inspection: product and process. What is your philosophy around test and inspection? I think you have approached it differently.
Alex Stepinski: The industry traditionally has relied on time zero testing. Defects that are 100% there, not latent defects; this is where things started in our industry. As time went on, methods were developed for latent defects. For instance, IBM originally started decades ago doing CAF testing, shorts testing in chambers. They simulated reflow testing in chambers. As a big OEM, this drove reliability to their products.
Gradually, these philosophies spread through the industry and more methods have been developed. Now, we do this OM test method on IPC D coupons for via reliability. The CAF method hasn’t improved too much. It’s slow and steady, but it’s much more prevalent. But time zero is still what most people do. You generally do reliability through regression. It’s not direct measurement, so there’s a lot of inferences that need to be made; with the time zero work, you have a probe tester and a fixture tester. It runs against your parameters, whatever they are—whether they’re some advanced military parameters, IPC standard parameters, or something special.
This is what people do. My philosophy is to rely less on this and more on sensors throughout the process to measure things non-destructively, then build a model for how you’re going to perform, and just validate against the model. It’s the next step slowly happening worldwide. For instance, we’ve had 2D AOI for many years. Sometimes, this is complemented with electrical tests. Now, you start to see more 3D AOI happening. You see them putting more sensors on the AOI equipment for direct measurement. Then, you also have the traditional signal integrity testing. The challenge with that is it’s never been fully industrialized with automation. There are some tools in the market, but you don’t see them spread everywhere.
It comes down to whether it’s much better to do quick microscopy, or to use a 3D back drilling technology that will sense the location of the plane layers internally.
If you take these methods and integrate them with serialization using QR codes and things like that, you can map a whole panel and find out how thick your prepreg and your cores are, and know the width and height of the features. It’s all about taking this information, throwing it into a data lake like they do in many other industries, then running your analytics, forecasting, predicting what will happen, and doing some spot validation.
It’s the next phase in the market. Digital transformation is a very common topic in many industries, but not so much in PCB. There’s a lot of other sensors out there as well. There are gravimetric techniques that can be used. We hardly use any gravimetric tools to do process control. There are imaging methods to look at roughness on the surface, to make sure things are clean. These things have all been developed for other industries, and you see us just starting to incorporate them.
Matties: Who drives this in the organization? It’s not going to be the quality manager, and it’s probably not a skill set that already exists inside a fabricator. You’re special in that you went out to create something new, fresh, and innovative, whereas everybody else is in a business cycle, if you will. How do they exchange that mentality, and what do they need to do?
Stepinski: From my perspective, this is generally a low-margin business and that’s a fundamental challenge. R&D is expensive, and there always needs to be some dedicated R&D resources to evaluate these technologies. There is some R&D overseas; one of the biggest PCB shops with R&D is AT&S, with a large organization based in Austria.
To read this entire conversation, which appeared in the November 2021 issue of PCB007 Magazine, click here.
Suggested Items
Intervala Hosts Employee Car and Motorcycle Show, Benefit Nonprofits
08/27/2024 | IntervalaIntervala hosted an employee car and motorcycle show, aptly named the Vala-Cruise and it was a roaring success! Employees had the chance to show off their prized wheels, and it was incredible to see the variety and passion on display.
KIC Honored with IPC Recognition for 25 Years of Membership and Contributions to Electronics Manufacturing Industry
06/24/2024 | KICKIC, a renowned pioneer in thermal process and temperature measurement solutions for electronics manufacturing, is proud to announce that it has been recognized by IPC for 25 years of membership and significant contributions to electronics manufacturing.
Boeing Starliner Spacecraft Completes Successful Crewed Docking with International Space Station
06/07/2024 | BoeingNASA astronauts Barry "Butch" Wilmore and Sunita "Suni" Williams successfully docked Boeing's Starliner spacecraft to the International Space Station (ISS), about 26 hours after launching from Cape Canaveral Space Force Station.
KIC’s Miles Moreau to Present Profiling Basics and Best Practices at SMTA Wisconsin Chapter PCBA Profile Workshop
01/25/2024 | KICKIC, a renowned pioneer in thermal process and temperature measurement solutions for electronics manufacturing, announces that Miles Moreau, General Manager, will be a featured speaker at the SMTA Wisconsin Chapter In-Person PCBA Profile Workshop.
The Drive Toward UHDI and Substrates
09/20/2023 | I-Connect007 Editorial TeamPanasonic’s Darren Hitchcock spoke with the I-Connect007 Editorial Team on the complexities of moving toward ultra HDI manufacturing. As we learn in this conversation, the number of shifting constraints relative to traditional PCB fabrication is quite large and can sometimes conflict with each other.