-
- News
- Books
Featured Books
- design007 Magazine
Latest Issues
Current IssueProper Floor Planning
Floor planning decisions can make or break performance, manufacturability, and timelines. This month’s contributors weigh in with their best practices for proper floor planning and specific strategies to get it right.
Showing Some Constraint
A strong design constraint strategy carefully balances a wide range of electrical and manufacturing trade-offs. This month, we explore the key requirements, common challenges, and best practices behind building an effective constraint strategy.
All About That Route
Most designers favor manual routing, but today's interactive autorouters may be changing designers' minds by allowing users more direct control. In this issue, our expert contributors discuss a variety of manual and autorouting strategies.
- Articles
- Columns
- Links
- Media kit
||| MENU - design007 Magazine
Estimated reading time: 4 minutes
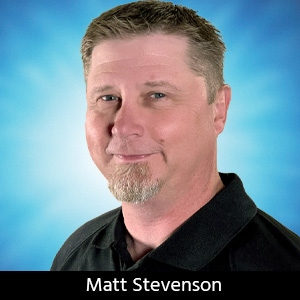
Connect the Dots: Best Practices for Solder Mask Application
Today’s PCBs increasingly must operate in challenging conditions. Whether it’s an iPad hot to the touch after several hours of gaming or a drone slicing through smoke and debris to monitor a wildfire, boards need protection from the elements.
That’s where solder mask comes in. Solder mask isn’t just the stuff that makes PCBs green and protects the copper from the elements; it is an increasingly vital part of boards that have to do more in less hospitable environments.
Solder mask coats your whole board (apart from the solder pads) so the PCB doesn’t react with the atmosphere and lose chemical properties through oxidation. It also prevents contamination from dust and debris that may settle on the board and create shorts. Solder mask prevents bridging between features during wave reflow assembly, limits external conductive influences, and helps ward off voltage spikes.
Don’t Skimp on Solder Mask
Some board fabrication houses offer reduced prices if you order your boards without solder mask and that can work for some designs, but not always. If you choose to use a stencil to apply solder paste and run the board through a reflow oven, the solder will spread back on the exposed copper traces. This may leave your parts without enough solder on the pins to create a reliable connection or, worse yet, bridge adjacent conductors creating shorts. Solder mask will increase reliability and reduce cost in the long run.
All in all, solder mask is a critical element when it comes to sustained performance. How it gets on the PCB matters, making it important to remember best practices for its application.
Breaking Down the Solder Mask Process
The solder mask process is much like the imaging process. First, a photoimageable polymer is applied to the manufacturing panel. There are several types of solder mask polymers, including liquid epoxy and dry film, but the most common in use today is liquid photoimageable solder mask (LPI). Liquid polymer can be applied through several different techniques including spraying, flood coating, and screening. Direct printing is another option that is gaining adoption in the industry, but it follows a different process than the other three methods and should not be considered as part of the process outlined here.
Once the panel is coated in the LPI on both sides, it is heated to remove some of the solvents, making the deposit illiquid and tacky to the touch, but not cured either. With the semi-hardened liquid polymer coating, the solderable surfaces can now be imaged onto the panel. The majority of the LPI is exposed to a high intensity light source, cross-linking the polymer, and chemically changing that portion of the solder mask.
During this part of the process, solderable surfaces such as pads, through-holes, and contact points are masked from the light source—leaving the LPI in its tacky and liquid form. The exposed panels are then “developed” through a chemical process that removes the unexposed LPI from the panels and leaves the parts that were exposed intact, creating all the pads and fiducials.
For most PCB designs there is much more solder mask left remaining on the board than the amount removed. This gives the PCB its familiar green coloring. Creative choice of solder mask color can also add some personality to your boards. Red, blue, yellow, and even pink are among the options for those who want a PCB to stand apart from the crowd. After developing the panels, they are again heated to drive off the remaining solvents from the LPI. This cures the solder mask coating into a hardened epoxy that protects the board.
Application of the legend or nomenclature to the panels before final thermal curing will enhance the bonding between the two epoxies. Doing so at this point in the process creates a very strong bond between the solder mask and the silkscreened nomenclature. The chemical bond created at this stage makes it much less likely that the nomenclature will wear off or chip away from the solder mask than if it was applied later in the process after the final thermal curing.
The silkscreen application process uses a printer to apply the silkscreen ink to a manufacturing panel in much the same way that an inkjet printer applies ink to paper. It comes directly from the digital data and is aligned directly to the panel image, improving registration and quality while lessening the process’s impact on the waste treatment process.
More precise application of nomenclature can also improve component placement accuracy during automated assembly. Without nomenclature, machine assembly won’t be as reliably accurate. Unfortunately, Gerber files do not tell the assembly machines exactly where each part is supposed to go and what angle and orientation is required. Footprint errors are common, as are components with ambiguous marking.
The addition of solder mask and legend to your PCB design will go a long way toward protecting your design from external factors and give your assembly team the best foundation to be successful: a clear roadmap of the parts and enough barriers to prevent solder shorting between components.
This column originally appeared in the December 2021 issue of Design007 Magazine.
More Columns from Connect the Dots
Connect the Dots: How to Avoid Five Common Causes of Board FailureConnect the Dots: Sequential Lamination in HDI PCB Manufacturing
Connect the Dots: The Future of PCB Design and Manufacturing
Connect the Dots: Proactive Controlled Impedance
Connect the Dots: Involving Manufacturers Earlier Prevents Downstream Issues
Connect the Dots: Stop Killing Your Yield—The Hidden Cost of Design Oversights
Connect the Dots: Designing for Reality—Routing, Final Fab, and QC
Connect the Dots: Designing for Reality—Surface Finish