-
- News
- Books
Featured Books
- design007 Magazine
Latest Issues
Current IssueProper Floor Planning
Floor planning decisions can make or break performance, manufacturability, and timelines. This month’s contributors weigh in with their best practices for proper floor planning and specific strategies to get it right.
Showing Some Constraint
A strong design constraint strategy carefully balances a wide range of electrical and manufacturing trade-offs. This month, we explore the key requirements, common challenges, and best practices behind building an effective constraint strategy.
All About That Route
Most designers favor manual routing, but today's interactive autorouters may be changing designers' minds by allowing users more direct control. In this issue, our expert contributors discuss a variety of manual and autorouting strategies.
- Articles
- Columns
- Links
- Media kit
||| MENU - design007 Magazine
Estimated reading time: 6 minutes
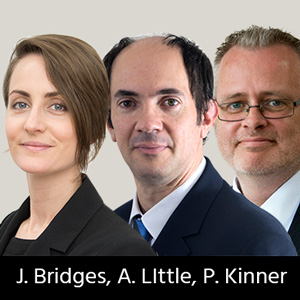
Sensible Design: How to Select the Best Resin Category for Your Application
Resin chemistries are extensively used for potting and encapsulation in the electronics and electrical industries, but not everyone gets it right the first time. With so many resin options available, deciding which resin is best suited for your application can present a challenge by itself. In this month’s column, I will look at the features and benefits found in each of the three major categories: epoxy, polyurethane, and silicone. I will highlight the different types of resin properties and applications, using examples from Electrolube’s wide-ranging resin portfolio, and provide an overview of the different chemistries available to improve product selection for various applications as well as determine which mixing and application techniques are appropriate to specific production needs.
In the first instance, production volumes need to be considered to establish whether you use manual or machine-based application methods. Will you be prototyping, delivering a short production run, or manufacturing on a much larger scale? Your answers to these questions will also define which resin types are compatible with these application techniques. For example, if you are potting prototypes or small volume runs you will most likely use manual methods, while much larger volume runs will be best served by automated, machine-based mixing and dispensing systems. Should you be looking to work up from the prototype stage to a full production run, then the differences between manual and machine mixing and dispensing will have to be taken into account when choosing your resin.
Let’s start by looking at each of the three categories and what they can bring to the table. Each category has distinctive properties and your choice will be guided by how these properties can be best incorporated to meet your particular production circumstances and application needs.
Epoxy Resins
First is the epoxy resin category. Epoxies enjoy wide popularity in the electronics industry due to their excellent electrical and mechanical properties, as well as their ability to offer protection against chemicals and high temperatures. Their use enables components to be protected against dust, moisture, and short circuits, and as standard epoxy resins have better thermal conductivity than air, they provide more efficient dissipation of heat from components, prolonging service life.
Today there are a wide range of different epoxy-based resin systems available, offering a comprehensive range of different properties. A range of different cure speeds and cured properties can be obtained using different hardeners; amines, amine modified polymers and polyamides are all available. Some reactions can be very fast, and also very exothermic, leading to the possibility of a runaway reaction, particularly with large potting volumes. This can be mitigated by modifying the hardener or by using a filler, which will help absorb the heat of reaction and can often help achieve flame retardant properties. It is important to note that the temperature at which a resin is cured will affect not only its cure speed, but also the quality of the end result. For example, post curing epoxy resins can often improve the glass transition temperative, so it is important to carry out some trials before committing to a specific cure profile.
One of our newest epoxy resins is a highly thermally conductive resin with low viscosity, ideal for potting cells within electric vehicle batteries. The UL94 V-0 approved epoxy potting compound can withstand long durations at high temperatures and can assist with securing cells in place whilst dissipating the heat away to the surroundings. This particular epoxy resin creates a protective shield around the battery and enables strong adhesion, high temperature resistance, and retention of characteristics throughout the thermal cycling process.
This epoxy resin portfolio includes a variety of clear, opaque, one- and two-part products with a host of useful properties to meet most requirements from potting and sealing to dipping, including exceptional electrical and thermal characteristics, flame retardancy, and resistance to chemicals and fuels. Optically clear resins may be desirable for applications such as LED lighting fixtures, as the cured resin will obviously need to retain its clarity for the life of the unit. Colourless resins are also useful for prototyping applications as the encapsulated components are easily viewed during and after environmental and mechanical testing. On the other hand, coloured/opaque potting and encapsulation resins conceal what lies beneath the encapsulant surface, providing an effective foil against counterfeiters or those wishing to copy a circuit layout, helping you to protect your intellectual property.
Polyurethane Resins
While epoxy resins are hard encapsulants when cured, polyurethane resins are typically elastomeric—more rubber-like—in their cured state, which is particularly useful if the circuit to be potted contains delicate components. Like epoxy resins, polyurethane resins provide chemical, dust, and moisture resistance, as well as excellent electrical insulation and good adhesion to most substrates, both metal and plastic. Unlike their epoxy counterparts, polyurethanes have a lower exotherm during cure, even for fast cure systems. Polyurethane resins typically have a lower continuous operating temperature range and should not be allowed to rise above 130°C for the majority of its lifetime.
One of our newest polyurethane resins has successfully been deployed in a car park sensor application, where the resin requirement needed to avoid RF interference and provide a dielectric constant of between 3-4 at 50Hz. It has a low viscosity ensuring sufficient flow in small gaps, as well as a wide temperature range of –60 to +125°C and a low exotherm (<35°C). With a Shore hardness of A80, the resin is suitable for protecting delicate components whilst providing good impact resistance to the external environment. It is a high-demand resin for IoT applications, due to its proven capability of protecting RF transmitters, sensors, and circuitry from harsh environments, vibration, temperature extremes, and water ingress.
It is much easier to tailor the cure speed with polyurethane systems, and the usable life and gel time of these can be adjusted to suit customer requirements, leading to faster process times and less work in progress. Polyurethanes show lower exotherm during cure than epoxies, and the heat generated is not usually a problem, even for fast cure systems.
Silicone Resin Chemistry
Though not as popular as epoxy and polyurethane resins, silicone resins do offer some distinct advantages when used as an encapsulating resin because the cured products have a high degree of flexibility across a wide temperature range, excellent chemical, dust and moisture resistance, and good electrical insulating properties. Silicone resins tend to be more expensive than epoxies or polyurethanes, but are ideally suited where high continuous operating temperatures (above 180°C) are required. Moreover, the exothermic temperature when working with silicone systems is very low indeed, ensuring compatibility with heat-sensitive components.
One product I work with is a two-part silicone potting and encapsulating resin which was primarily developed for the protection of LED drivers, however, its properties make it ideally suited for EV battery protection. The thermal conductivity is 1 W/mK, making it suitable for use in applications where the operating temperature will be up to 200°C. Its good flow characteristics make it an excellent choice for extremely tight spaces or difficult geometries.
What You Need to Know
As a rule of thumb, silicone resins have the broadest temperature range (-50 to +250°C), are generally soft resins, and are not as chemically resistant as some of the other chemistires. Some polyurethanes have a low glass transition temperature and are suited to lower temperatures than silicones (-60°C). Epoxies are more designed for higher temperature applications (-40 to +200°C), but have excellent adhesion to a wide range of substrates and excellent chemical resistance.
The majority of resins I use are two-part systems that, when mixed together in the correct ratio, react to form polymeric materials. By careful formulation, the properties of the cured resin can be tailored to meet individual customer requirements. If you foresee any challenges with matching resin types to your production procedures, be sure to contact your supplier’s technical support team for further advice. In my next column, I shall be taking an in-depth look at some of the most frequently asked questions we get asked as resin experts and will be exploring various options in response to these enquiries.
This column originally appeared in the February 2022 issue of Design007 Magazine.
Download your free copy of Electrolube's book, The Printed Circuit Assembler's Guide to… Conformal Coatings for Harsh Environments, and watch the micro webinar series “Coatings Uncoated!”
More Columns from Sensible Design
Sensible Design: Automotive Conformal Coating ApplicationsSensible Design: Green Coats Are In
Sensible Design: Encapsulation Resins—PU vs. Epoxy
Sensible Design: Avoiding Conformal Coating Pitfalls
Sensible Design: Comparing Traditional and Bio-based Resins
Sensible Design: All Resins Are Not Created Equal
Sensible Design: Can Solvent-free UV-cure Coatings Increase Stability and Throughput?
Sensible Design: Optimize Your Thermal Management