-
- News
- Books
Featured Books
- pcb007 Magazine
Latest Issues
Current IssueThe Hole Truth: Via Integrity in an HDI World
From the drilled hole to registration across multiple sequential lamination cycles, to the quality of your copper plating, via reliability in an HDI world is becoming an ever-greater challenge. This month we look at “The Hole Truth,” from creating the “perfect” via to how you can assure via quality and reliability, the first time, every time.
In Pursuit of Perfection: Defect Reduction
For bare PCB board fabrication, defect reduction is a critical aspect of a company's bottom line profitability. In this issue, we examine how imaging, etching, and plating processes can provide information and insight into reducing defects and increasing yields.
Voices of the Industry
We take the pulse of the PCB industry by sharing insights from leading fabricators and suppliers in this month's issue. We've gathered their thoughts on the new U.S. administration, spending, the war in Ukraine, and their most pressing needs. It’s an eye-opening and enlightening look behind the curtain.
- Articles
- Columns
- Links
- Media kit
||| MENU - pcb007 Magazine
Alex Stepinski: Taking Control of Input Costs
February 23, 2022 | I-Connect007 Editorial TeamEstimated reading time: 3 minutes
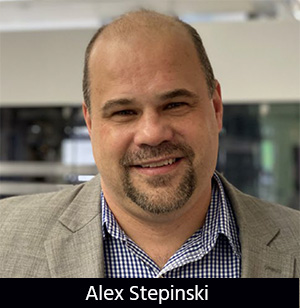
Barry Matties and Nolan Johnson talk with Alex Stepinski about strategies to lower costs in brownfield facilities. Alex has extensive experience designing and optimizing manufacturing processes and is currently helping companies implement straightforward step-by-step solutions to move into smarter manufacturing across different industries.
Barry Matties: Alex, brownfield factories are stuck with space limitations and automation is a challenge. What could be a different way of thinking about a brownfield site and why it makes sense?
Alex Stepinski: First, I want to address a fundamental bias. Many people associate me with the greenfield sites that I’ve architected over the past years, and which became an Industry 4.0 example in the United States. It’s not because that was the only way to do it, but because that was the business case. The business plan at the time was to build new facilities for OEMs that didn’t have any PCB fab capabilities.
Brownfields do not follow the same plan to implement Industry 4.0. The investments to do so can be done over a longer period based on available monies and can be done to address the biggest opportunities first. I think there’s a little bit of a roadmap that any brownfield can follow.
The first step is serializing your products, and there are many options to do this. The best ones, in my experience, are laser based, using lasers from some of the sensor suppliers in the market, and many of the suppliers can integrate this for you into a piece of equipment so you don’t have to increase your footprint. It’s probably one of the only things that you might need to add. It doesn’t increase your footprint.
Once you serialize your products individually, then everything turns into a sensor-and-software problem, and this doesn’t add to the footprint in most cases. Industry 4.0 is about correlating data and making decisions based on interpolations of data, doing regressions, and things like this. It’s not advanced artificial intelligence. Advanced AI in business is when you do image recognition, natural language processing; this is the forefront right now, as well as very advanced algorithms that are dealing with B2C sales, marketing analytics, self-driving, and so forth. This is where AI is focused because it is the biggest return. You can buy equipment that even has some of these features. You don’t have to touch the concept of AI.
But on the PCB and EMS side, it’s more “AI light,” or ”more-than-Excel algorithms.” Something we called just a normal algorithm 20 years ago is now called AI. It’s a sexy term. Robots aren’t taking over the world any time soon. The fundamental things to do in a brownfield to tease out value from a planning perspective is just a step-by-step approach, one process at a time.
It’s probably a one- or two-person engineering job. You give them subject matter expertise, availability, make sure they know how to do some basic coding, understand sensor options, and then they go process by process. What are some of the interpolations you can do? Well, just getting a time stamp. All you need is a photo sensor to know something went through the machine, and then you can also code at some point when it went through, when it came out. You could do this in one step or multiple steps.
The sensor kit for most processes is generally $5,000 to $10,000 per tool to get time and basic settings, and then you save their recorded data, which is just the serial number that you scanned, the times it went through the machine; you save it into a database. If you can pull the error codes by time out of your machine and put that in a data table, then you can correlate the two together and you can know something happened: “I heard an alarm while this panel was being processed.” Making an API to your other systems adds further interpolations that can then lead to predictive recipes/decisions.
To read this entire conversation, which appeared in the February 2022 issue of PCB007 Magazine, click here.
Suggested Items
Specially Developed for Laser Plastic Welding from LPKF
06/25/2025 | LPKFLPKF introduces TherMoPro, a thermographic analysis system specifically developed for laser plastic welding that transforms thermal data into concrete actionable insights. Through automated capture, evaluation, and interpretation of surface temperature patterns immediately after welding, the system provides unprecedented process transparency that correlates with product joining quality and long-term product stability.
Smart Automation: The Power of Data Integration in Electronics Manufacturing
06/24/2025 | Josh Casper -- Column: Smart AutomationAs EMS companies adopt automation, machine data collection and integration are among the biggest challenges. It’s now commonplace for equipment to collect and output vast amounts of data, sometimes more than a manufacturer knows what to do with. While many OEM equipment vendors offer full-line solutions, most EMS companies still take a vendor-agnostic approach, selecting the equipment companies that best serve their needs rather than a single-vendor solution.
Keysight, NTT, and NTT Innovative Devices Achieve 280 Gbps World Record Data Rate with Sub-Terahertz for 6G
06/17/2025 | Keysight TechnologiesKeysight Technologies, Inc. in collaboration with NTT Corporation and NTT Innovative Devices Corporation (NTT Innovative Devices), today announced a groundbreaking world record in data rate achieved using sub-THz frequencies.
Priority Software Announces the New, Game-Changing aiERP
06/12/2025 | Priority SoftwarePriority Software Ltd., a leading global provider of ERP and business management software announces its revolutionary aiERP, leveraging the power of AI to transform business operations.
Breaking Silos with Intelligence: Connectivity of Component-level Data Across the SMT Line
06/09/2025 | Dr. Eyal Weiss, CybordAs the complexity and demands of electronics manufacturing continue to rise, the smart factory is no longer a distant vision; it has become a necessity. While machine connectivity and line-level data integration have gained traction in recent years, one of the most overlooked opportunities lies in the component itself. Specifically, in the data captured just milliseconds before a component is placed onto the PCB, which often goes unexamined and is permanently lost once reflow begins.