-
- News
- Books
Featured Books
- design007 Magazine
Latest Issues
Current IssueProper Floor Planning
Floor planning decisions can make or break performance, manufacturability, and timelines. This month’s contributors weigh in with their best practices for proper floor planning and specific strategies to get it right.
Showing Some Constraint
A strong design constraint strategy carefully balances a wide range of electrical and manufacturing trade-offs. This month, we explore the key requirements, common challenges, and best practices behind building an effective constraint strategy.
All About That Route
Most designers favor manual routing, but today's interactive autorouters may be changing designers' minds by allowing users more direct control. In this issue, our expert contributors discuss a variety of manual and autorouting strategies.
- Articles
- Columns
- Links
- Media kit
||| MENU - design007 Magazine
Estimated reading time: 5 minutes
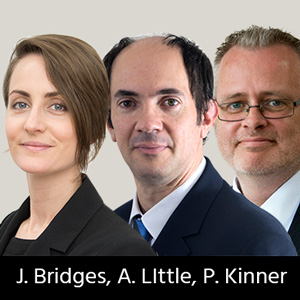
Sensible Design: What Can Manufacturers Expect from Bio-based Conformal Coatings?
Globally, managing finite resources is imperative as we strive to achieve a more innovative and lower emission economy. Reducing dependency on fossil fuels in the chemical industry has led to the emergence of new bio-based alternatives, but what do these bring to the table for electronics manufacturers? Bio-based materials, obtained from biological resources (biomasses, feedstock, plants, and biological waste), deliver a viable and sustainable alternative to materials derived from petrochemicals.
We have developed a new coating incorporating 75% bio-organic content from renewable sources. It’s a global first for the industry and is completely free from solvents. It meets the needs of both manufacturers and consumers, essentially based on ethics, performance and process. So, how will bio-based coatings impact performance and what can you expect? Let’s explore bio-based coatings in more detail.
1. What are the benefits of bio-based coatings?
First, it goes without saying that bio-coatings have significantly less impact on the environment and meet the ethical needs of manufacturers and end users. However, the most surprising benefit observed during the development of this bio-coating was the improvement in terms of performance that were achieved. The bio-based polymers we developed showed improved condensation resistance, thermal stability, flexibility, and adhesion over many petrochemical-derived polymers that we developed. Nature truly is an amazing source of inspiration. More or less every single ingredient in a typical formulation can be formulated from either completely bio-based or high degree of bio-containing raw materials, with the current exception of flame retardants. The bio-coating has performance in abundance and top environmental credentials to match, making it a win-win solution. We are also “future-proofing” at the same time; for instance, if the government says to introduce new environmental measures in a couple years’ time, then manufacturers are covered.
2. What is the financial impact for a bio-based coating over a traditional chemistry?
Currently, many of the supply chains of these new raw materials are developing scale economies, so the raw materials are more expensive than their mature, petroleum-derived alternatives. Therefore, the improvement in performance of the bio-based coating material, over a more traditional petrochemical material, can come at an increased cost. However, as electric vehicles become more commonly adopted and the internal combustion engine (ICE) becomes more economical and less widely used, oil production is likely to slow and become increasingly expensive, so at some point in the near future, the bio-based materials are likely to become more economical than oil-based feedstock.
3. Which conformal coatings are the most popular and why?
This is a tough question and one we get asked a lot. In general, I would say that acrylic materials and UV-curable materials are amongst the most popular. Acrylic materials remain amongst the most popular class of coating due to their ease of application, rapid drying by solvent evaporation, and ease of re-work—immerse them in solvent, wash with solvent, et voila, no coating remaining. However, acrylic coatings provide less adequate levels of protection in more demanding applications, such as condensation and high environmental impact. Many end users are beginning to realise that they will need to move away from acrylic materials due to both of these factors. Especially prevalent is the requirement of many automotive OEMs to pass a condensation test (e.g. K15-19 from BMW GS95024-3-1). Even in aerospace applications, there is an increased focus on condensation resistance in coated assemblies due to the rapid environmental changes experienced during descent from 40,000 feet to a hot and humid runway, for example.
As for UV-cure materials, the rapid nature of the primary UV cure, as well as the polymerisation process itself, tend to cause significant amounts of shrinkage, which creates a lot of stress in the coating that is commonly alleviated by stress-cracking during thermal cycling. The materials must also contain a secondary curing mechanism to ensure material beneath components, or otherwise shadowed from UV radiation by taller components, develops hardness, and cross-links. This is commonly a moisture-initiated cure reaction and can take weeks, months, or even years to complete, due to the fact that the outside of the material is partly cured from exposure to UV radiation; moisture must permeate through this membrane and CO2 gas produced during this curing process must permeate back out through the same membrane.
The benefit of a 2K UV-curable material is that once the two components are mixed, the reaction will proceed to completion in less than 24 hours in these shadowed areas that are not exposed to UV radiation. Also, the additional cure nature of the reaction ensures significantly less shrinkage and less stress, resulting in more flexible coatings that can better survive thermal shock.
4. Why did we decide to include bio-content in our conformal coatings and how did we test them?
We are very committed to the ISO 14000 obligations. It is an entirely logical and natural progression to look at how we can reduce the carbon footprint of our materials. The only surprising factor was the degree of performance improvement achieved with these innovative new materials.
Whilst the development focus is very much on meeting the highly demanding requirements of automotive and aerospace applications, the high-performance levels of these materials make them a great choice for any application. The materials really come into their own whenever thermal shock cycling and condensation resistance are the two main failure mechanisms. As for testing the bio-based coating, much of the development work focussed on doing a lot of work in harsh environments, testing and demonstrating improved condensation resistance due to the combined improvements of thickness and coverage provided by the material, further to the usual automotive requirements of thermal shock and max continuous operating temperatures with long term thermal humidity ageing.
5. Are there possibilities to increase the amount of bio-content within a coating and are more bio-based coatings in the pipeline?
There could be opportunities to increase bio-content in coatings but I don’t see it as a binary equation. We are developing more bio-based coatings (and bio-based encapsulation resins) so the industry can expect more high-performance, green solutions to come from Electrolube—now part of MacDermid Alpha Electronics Solutions. Having proven what this new product can do in terms of the environmental and performance benefits, we’re aiming to include bio-based materials in all our new product developments moving forward.
In years to come, more policies could be introduced to make fossil-fuel counterparts less appropriate and more expensive, perhaps through a carbon tax. Such future incentives would boost the demand for bio-based alternatives across all market segments. I hope you have enjoyed this month’s column and learned more about the benefits of bio-based coatings. In my next column, I’ll be exploring more conformal coating related topics.
This column originally appeared in the March 2022 issue of Design007 Magazine.
Download your free copy of Electrolube's book, The Printed Circuit Assembler's Guide to… Conformal Coatings for Harsh Environments, and watch the micro webinar series “Coatings Uncoated!”
More Columns from Sensible Design
Sensible Design: Automotive Conformal Coating ApplicationsSensible Design: Green Coats Are In
Sensible Design: Encapsulation Resins—PU vs. Epoxy
Sensible Design: Avoiding Conformal Coating Pitfalls
Sensible Design: Comparing Traditional and Bio-based Resins
Sensible Design: All Resins Are Not Created Equal
Sensible Design: Can Solvent-free UV-cure Coatings Increase Stability and Throughput?
Sensible Design: Optimize Your Thermal Management